TFT LCD TV - What is TFT LCD?
History of TFT LCD
Liquid crystal was discovered by the Austrian botanist Fredreich Rheinizer in 1888. "Liquid crystal" is neither solid nor liquid (an example is soapy water).
In the mid-1960s, scientists showed that liquid crystals when stimulated by an external electrical charge could change the properties of light passing through the crystals.
The early prototypes (late 1960s) were too unstable for mass production. But all of that changed when a British researcher proposed a stable, liquid crystal material (biphenyl).
Today‘s color LCD TVs and LCD Monitors have a sandwich-like structure (see figure below).

What is TFT LCD?
TFT LCD (Thin Film Transistor Liquid Crystal Display) has a sandwich-like structure with liquid crystal filled between two glass plates.

TFT Glass has as many TFTs as the number of pixels displayed, while a Color Filter Glass has color filter which generates color. Liquid crystals move according to the difference in voltage between the Color Filter Glass and the TFT Glass. The amount of light supplied by Back Light is determined by the amount of movement of the liquid crystals in such a way as to generate color.
TFT LCD - Electronic Aspects of LCD TVs and LCD Monitors
Electronic Aspects of AMLCDs
The most common liquid-crystal displays (LCDs) in use today rely on picture elements, or pixels, formed by liquid-crystal (LC) cells that change the polarization direction of light passing through them in response to an electrical voltage.
As the polarization direction changes, more or less of the light is able to pass through a polarizing layer on the face of the display. Change the voltage, and the amount of light is changed.
There are two ways to produce a liquid-crystal image with such cells: the segment driving method and the matrix driving method. The segment driving method displays characters and pictures with cells defined by patterned electrodes.
The matrix driving method displays characters and pictures in sets of dots.
Direct vs. multiplex driving of LCD TVs.

The segment drive method is used for simple displays, such as those in calculators, while the dot-matrix drive method is used for high-resolution displays, such as those in portable computers and TFT monitors.
Two types of drive method are used for matrix displays. In the static, or direct, drive method, each pixel is individually wired to a driver. This is a simple driving method, but, as the number of pixels is increased, the wiring becomes very complex. An alternative method is the multiplex drive method, in which the pixels are arranged and wired in a matrix format.
To drive the pixels of a dot-matrix LCD, a voltage can be applied at the intersections of specific vertical signal electrodes and specific horizontal scanning electrodes. This method involves driving several pixels at the same time by time-division in a pulse drive. Therefore, it is also called a multiplex, or dynamic, drive method.
Passive and Active Matrix LCDs
There are two types of dot-matrix LCDs.
Passive-matrix vs. active-matrix driving of LCD Monitors.

In passive-matrix LCDs (PMLCDs) there are no switching devices, and each pixel is addressed for more than one frame time. The effective voltage applied to the LC must average the signal voltage pulses over several frame times, which results in a slow response time of greater than 150 msec and a reduction of the maximum contrast ratio. The addressing of a PMLCD also produces a kind of crosstalk that produces blurred images because non-selected pixels are driven through a secondary signal-voltage path. In active-matrix LCDs (AMLCDs), on the other hand, a switching device and a storage capacitor are integrated at the each cross point of the electrodes.
The active addressing removes the multiplexing limitations by incorporating an active switching element. In contrast to passive-matrix LCDs, AMLCDs have no inherent limitation in the number of scan lines, and they present fewer cross-talk issues. There are many kinds of AMLCD. For their integrated switching devices most use transistors made of deposited thin films, which are therefore called thin-film transistors (TFTs).
The most common semiconducting layer is made of amorphous silicon (a-Si). a-Si TFTs are amenable to large-area fabrication using glass substrates in a low-temperature (300°C to 400°C) process.
An alternative TFT technology, polycrystalline silicon - or polysilicon or p-Si-is costly to produce and especially difficult to fabricate when manufacturing large-area displays.
Nearly all TFT LCDs are made from a-Si because of the technology‘s economy and maturity, but the electron mobility of a p-Si TFT is one or two orders of magnitude greater than that of an a-Si TFT.
This makes the p-Si TFT a good candidate for an TFT array containing integrated drivers, which is likely to be an attractive choice for small, high definition displays such as view finders and projection displays.
Structure of Color TFT LCD TVs and LCD Monitors
A TFT LCD module consists of a TFT panel, driving-circuit unit, backlight system, and assembly unit.
Structure of a color TFT LCD Panel:
 |
- LCD Panel
- TFT-Array Substrate - Color Filter Substrate
- Driving Circuit Unit
- LCD Driver IC (LDI) Chips - Multi-layer PCBs - Driving Circuits
- Backlight & Chassis Unit
- Backlight Unit - Chassis Assembly
|
It is commonly used to display characters and graphic images when connected a host system. The TFT LCD panel consists of a TFT-array substrate and a color-filter substrate.
The vertical structure of a color TFT LCD panel.

The TFT-array substrate contains the TFTs, storage capacitors, pixel electrodes, and interconnect wiring. The color filter contains the black matrix and resin film containing three primary-color - red, green, and blue - dyes or pigments. The two glass substrates are assembled with a sealant, the gap between them is maintained by spacers, and LC material is injected into the gap between the substrates. Two sheets of polarizer film are attached to the outer faces of the sandwich formed by the glass substrates. A set of bonding pads are fabricated on each end of the gate and data-signal bus-lines to attach LCD Driver IC (LDI) chips
Driving Circuit Unit
Driving an a-Si TFT LCD requires a driving circuit unit consisting of a set of LCD driving IC (LDI) chips and printed-circuit-boards (PCBs).
The assembly of LCD driving circuits.
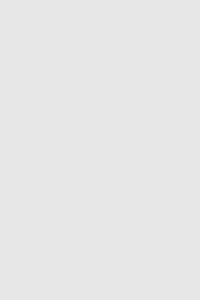
A block diagram showing the driving of an LCD panel.
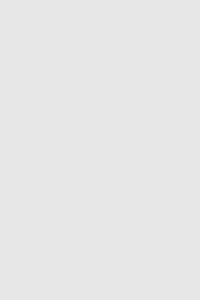
To reduce the footprint of the LCD module, the drive circuit unit can be placed on the backside of the LCD module by using bent Tape Carrier Packages (TCPs) and a tapered light-guide panel (LGP).
How TFT LCD Pixels Work
A TFT LCD panel contains a specific number of unit pixels often called subpixels. Each unit pixel has a TFT, a pixel electrode (IT0), and a storage capacitor (Cs). For example, an SVGA color TFT LCD panel has total of 800x3x600, or 1,440,000, unit pixels. Each unit pixel is connected to one of the gate bus-lines and one of the data bus-lines in a 3mxn matrix format. The matrix is 2400x600 for SVGA.
Structure of a color TFT LCD panel.
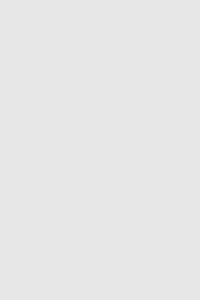
Because each unit pixel is connected through the matrix, each is individually addressable from the bonding pads at the ends of the rows and columns. The performance of the TFT LCD is related to the design parameters of the unit pixel, i.e., the channel width W and the channel length L of the TFT, the overlap between TFT electrodes, the sizes of the storage capacitor and pixel electrode, and the space between these elements. The design parameters associated with the black matrix, the bus-lines, and the routing of the bus lines also set very important performance limits on the LCD.
In a TFT LCD‘s unit pixel, the liquid crystal layer on the ITO pixel electrode forms a capacitor whose counter electrode is the common electrode on the color-filter substrate.
Vertical structure of a unit pixel and its equivalent circuit
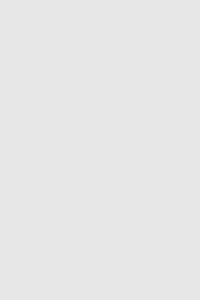
A storage capacitor (Cs) and liquid-crystal capacitor (CLC) are connected as a load on the TFT. Applying a positive pulse of about 20V peak-to-peak to a gate electrode through a gate bus-line turns the TFT on. Clc and Cs are charged and the voltage level on the pixel electrode rises to the signal voltage level (+8 V) applied to the data bus-line.
The voltage on the pixel electrode is subjected to a level shift of DV resulting from a parasitic capacitance between the gate and drain electrodes when the gate voltage turns from the ON to OFF state. After the level shift, this charged state can be maintained as the gate voltage goes to -5 V, at which time the TFT turns off. The main function of the Cs is to maintain the voltage on the pixel electrode until the next signal voltage is applied.
Liquid crystal must be driven with an alternating current to prevent any deterioration of image quality resulting from dc stress. This is usually implemented with a frame-reversal drive method, in which the voltage applied to each pixel varies from frame to frame. If the LC voltage changes unevenly between frames, the result would be a 30-Hz flicker. (One frame period is normally 1/60 of a second.) Other drive methods are available that prevent this flicker problem.
Polarity-inversion driving methods.
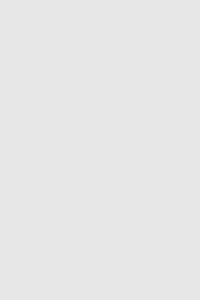
In an active-matrix panel, the gate and source electrodes are used on a shared basis, but each unit pixel is individually addressable by selecting the appropriate two contact pads at the ends of the rows and columns.
Active addressing of a 3x3 matrix
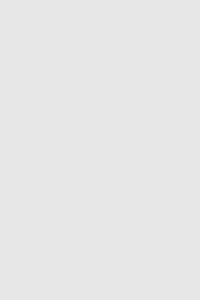
By scanning the gate bus-lines sequentially, and by applying signal voltages to all source bus-lines in a specified sequence, we can address all pixels. One result of all this is that the addressing of an AMLCD is done line by line.
Virtually all AMLCDs are designed to produce gray levels - intermediate brightness levels between the brightest white and the darkest black a unit pixel can generate. There can be either a discrete numbers of levels - such as 8, 16, 64, or 256 - or a continuous gradation of levels, depending on the LDI.
The optical transmittance of a TN-mode LC changes continuously as a function of the applied voltage. An analog LDI is capable of producing a continuous voltage signal so that a continuous range of gray levels can be displayed. The digital LDI produces discrete voltage amplitudes, which permits on a discrete numbers of shades to be displayed. The number of gray levels is determined by the number of data bits produced by the digital driver.
Generating Colors
The color filter of a TFT LCD TV consists of three primary colors - red (R), green (G), and blue (B) - which are included on the color-filter substrate.
How an LCD Panel produces colors.
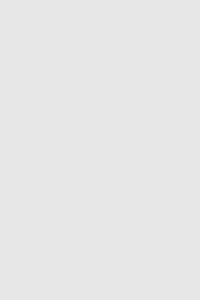
The elements of this color filter line up one-to-one with the unit pixels on the TFT-array substrate. Each pixel in a color LCD is subdivided into three subpixels, where one set of RGB subpixels is equal to one pixel. (Each subpixel consists of what we‘ve been calling a unit pixel up to this point.)
Because the subpixels are too small to distinguish independently, the RGB elements appear to the human eye as a mixture of the three colors. Any color, with some qualifications, can be produced by mixing these three primary colors.
The total number of display colors using an n-bit LDI is given by 23n, because each subpixel can generate 2n different transmittance levels.
TFT LCD - TFT Device Design
TFT Device Design
There are many structures for thin-film transistors (TFTs), with the first major distinction among them being planar CMOS structures vs. staggered amorphous-silicon (a-Si) structures.
Structure of TFT electrodes
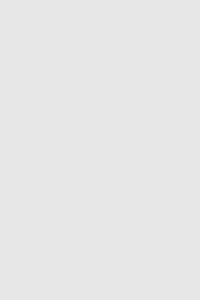
The a-Si TFTs are further divided into staggered and inverse-staggered types.
Structural difference between top- and bottom-gate TFTs
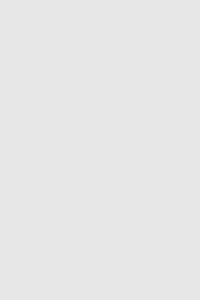
In the inverse-staggered type, the ohmic layer (n+ a-Si) in the channel region can either be etched directly (the etch-back method) or etched by forming a protective film on the a-Si thin film (the etch-stopper method). Each method has its own set of advantages and disadvantages. The inverse-staggered structure offers a relatively simple fabrication process and an electron mobility that is about 30 percent larger than that of the staggered type. These advantages have resulted in the bottom-gate TFT structure becoming more widely adopted in TFT-LCD design, despite the fact that it‘s technically an upside-down structure.
Because a-Si has photoelectric characteristics, the a-Si TFT must be shielded from incident light .The a-Si layer must also be as thin as possible to minimize the generation of photo-induced current, which can cause the TFT to malfunction.
Reduction of photo-induced leakage current in a TFT
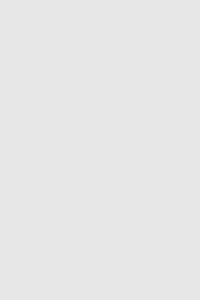
In the top-gate structure, a light-shield layer must first be formed at the region of the TFT channel The formation of this light shield may cause an extra process step. In bottom-gate TFTs, on the other hand, a gate electrode is first formed at the TFT channel region, where it also serves as a light-shield layer.
Light-shielding structures in a TFT-Array
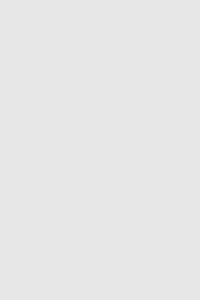
Design Parameters for TFT Arrays
The operational characteristics of a TFT are determined by the sizes of its electrodes, the W/L ratio, and the overlap between the gate electrode and the source-drain .
Design of an a-Si TFT
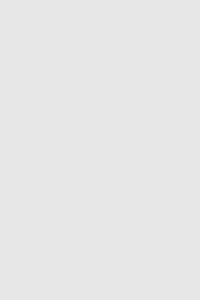
The parasitic capacitances resulting from the overlap of electrodes can not be avoided in staggered TFT structures, but the parasitic effects must be minimized to maximize the LCD‘s performance. To reduce the overlap between the electrodes, a self-align process is often implemented .
Minimizing parasitic capacitance in TFTs
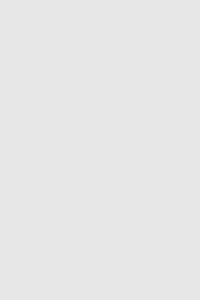
It turns out that the characteristics of the a-Si TFTs used in AMLCDs are very similar to the characteristics of the MOSFETs in semiconductor devices.
I-V Characteristics of an a-Si TFT and its operating points
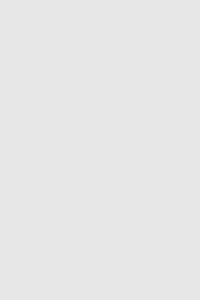
When a TFT panel is operated under real-world conditions, the gate voltage is set at either 20 V for switch-on, or at -5 V for switch-off. Under these operating conditions, the a-Si TFT is a good switching device with an on/off current ratio larger than 106. The performance of the TFT also depends on fabrication process parameters, such as electron mobility and thickness of the gate insulators. If we wish to increase the current gain of the TFT for better pixel-switching performance, and the process parameters are fixed, the only thing we can do is increase the W/L ratio. But doing this is not without a significant trade-off: The larger W/L results in a lower aperture ratio - less of the pixel‘s area is transparent to light when the pixel is ON - so the display‘s brightness and contrast are reduced.
Storage Capacitor Design
To maintain a constant voltage on a charged pixel over the entire frame cycle, a storage capacitor (Cs) is fabricated at each pixel. A large Cs can improve the voltage holding ratio of the pixel and reduce the kickback voltage, with resulting improvements in contrast and flicker, but a large Cs results in a lower aperture ratio and higher TFT load. The storage capacitor can be formed by using either an independent storage-capacitor electrode or part of the gate bus-line as a storage-capacitor electrode (Cs-on-gate method)
Example of an independent-Cs design and equivalent circuit
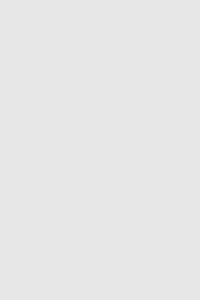
Example of a Cs-on-gate design and equivalent circuit
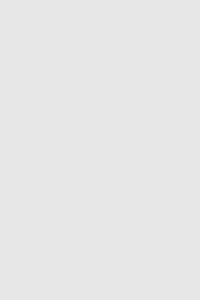
The advantages of the Cs-on-gate method are that it eliminates the need for modification in the fabrication process; it minimizes the number of processes; and it produces a larger aperture ratio than does the independent Cs method. But few things are free in TFT-LCD design. The trade-off with the Cs-on-gate method is an increase in the RC time constant of the gate bus-line, which reduces the TFT switching performance.
This RC delay problem can have serious effects on the appearance of the display.
RC delay of a gate signal and its effect on a black display
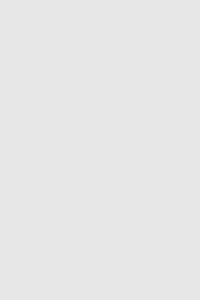
The solution lies in fabricating the gate bus-line with a low-resistance material such as aluminum (Al).
Signal Bus-line Design
The requirement that the gate bus-line must have a small RC time delay is particularly important for larger and higher-resolution LCDs. If the widths of the signal bus-lines are increased to reduce resistance, the aperture ratio of the pixels is reduced, so the preferred approach is to use a low-resistance material for the bus-lines. For this, Al offers advantage over other metals, such as Cr, W, and Ta. But, in the bottom-gate TFT process, the gate electrodes are first fabricated on the glass substrate and then subjected to high-temperature processes and various chemical etches. So, to use Al as a gate-electrode material, the Al gate electrodes must be protected from damage produced by hillock formation.
Design of low-resistance aluminum gate bus-line
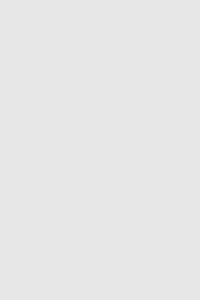
A thin film of an aluminum oxide (Al2O3), formed by anodic oxidation of the Al surface at room temperature, can protect the Al electrodes from the problems associated with hillock formation. Double-metal or clad structures over the Al electrodes - using a relatively stable material such as Cr, Ta, or W - can also be used to protect the Al electrodes. The trade-off is that these approaches require an additional process. Recently, Al alloy (such as Al-Nd), which can suppress hillock formation, has been used as a gate-electrode material to eliminate the additional process.
Aperture Ratio
As implied previously, another important design consideration is maximizing the aperture ratio of the pixel. In the unit cell, TFT electrodes, storage-capacitor electrodes, signal bus-lines, and the black-matrix material constitute opaque areas.
Opaque areas and aperture ratio of a pixel
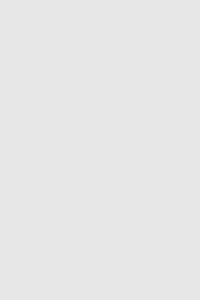
The combined areas of these elements, along with the area of the pixel aperture through which light can pass, determine the aperture ratio of the pixel. The aperture ratio is given by the area of the pixel aperture divided by the total pixel area (aperture area plus the area of the opaque elements). To increase the aperture ratio as much as possible, the size of the opaque elements must be made as small as possible, while maintaining a design that maximizes the size of the pixel-electrode area. Unfortunately, one can only go so far in reducing the opaque areas before degrading image quality and yield. As shown in Fig. 12, the light-shield area on the color-filter substrate must be extended to block the light leaking through the gap between the data-line and the pixel ITO. To do this in conventional TFT-LCD cell structures, while simultaneously providing an adequate plate-alignment margin, significantly reduces the aperture.
But far higher aperture ratios can be achieved by switching from a conventional structure to the BM-on-Array structure, regardless of the accuracy of the plate alignment. The aperture ratio of this cell structure is not determined by the BM opening at the color filter substrate, but by the BM-on-Array, which can be formed with a very high positioning accuracy.
Improvement of aperture ratio using a black-matrix-on-TFT-array
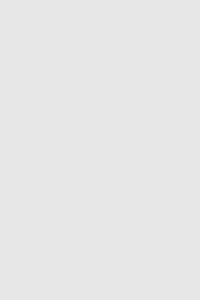
In an independent-Cs-electrode design, the aperture ratio can be increased if the storage-capacitor electrode is fabricated using ITO.
Improvement of aperture ratio using an ITO layer as a Cs electrode
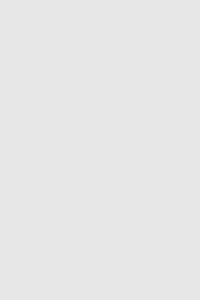
Design for Redundancy
Even when the greatest care is taken and sophisticated quality-management procedures are applied, it is not possible to make the TFT-array fabrication process so perfect that it produces only completely defect-free arrays.
Possible line and pixel defects on a TFT array
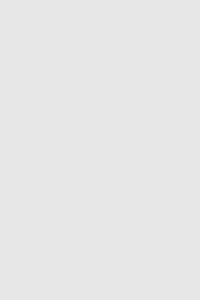
To improve the production yield in the fabrication process, redundancy design, repairable design, and fault-tolerant designs are often used. Dual-bus-line design or double-metal structure can help recover from problems of line breakage. Dummy-repair-line design can save the defective panel from data-bus-line open failures. While these redundant-design techniques can effectively improve fabrication yield, in some cases they can also reduce the aperture ratio.
The TFT-array must be protected from electrostatic discharge (ESD), which can be generated in the fabrication processes such as during the rubbing of the alignment layer and spin-drying. Design approaches for protecting the TFT-array against ESD include bus-line shorting and ESD protection circuits.
ESD protection using a bus-line shorting method
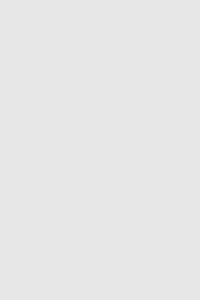
ESD protection using protection circuits
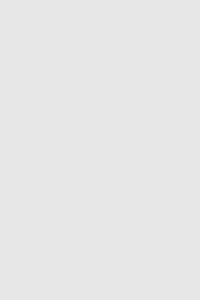
We would like to express our appreciation to Samsung Electronics for the preceding information.
|