1. 电池片隐裂

产生的原因:
a. 电池片在焊接或搬运过程中受外力造成。
b. 电池片在低温下没有经过预热,在短时间内突然受到高温后出现膨胀造成隐裂现象 。
c. 焊接时瞬间温度过高。
组件影响
a.隐裂会影响组件功率衰减。
b.隐裂长时间会导致碎片、热斑等现象直接影响组件性能。
预防措施:
a.在生产过程中避免电池片过于受外力碰撞。
b.在焊接过程中电池片要提前保温,烙铁温度要符合要求。
c.EL测试要严格分析每一张图片上的黑线。
d.图片上有隐裂时,打开背板及EVA,用手电进行确认。隐裂片及时更换。
2、EVA未溶
产生的原因:
a. EVA 材料过期。
b. 层压机加热工艺(如层压机温度低,层压时间短等)设计不合理。
c. 交联度试验未能摸索出该EVA的正确工艺参数。
预防措施:
a.加强原材料供应商的改善及原材料检验。
b.严格控制层压机温度、时间等重要参数。
c.按照要求做交联度试验,并将交联度控制在85%±5%内。
3、气泡

产生的原因:
a. 组件内有异物。
b. EVA过期。
c. 层压机故障:真空度低、密封圈有裂纹。
d. 层压机参数设定异常。
e. 助焊剂表面残留。
f. 互联条虚焊。
组件影响
组件气泡会影响脱层,严重会导致报废。
预防措施:
a.改善车间生产环境,层压前进行检查。
b.使用的EVA要在保质期内,当天使用不完的要密封保存。
c.大面积气泡突发时调整层压机参数。
d.对层压机每班做好点检,及时观察上下抽真空数值,及时检查密封圈状况,做好日常保养。
e.不同厂商的EVA 有不同的层压参数,及时调整工艺。
f.控制好助焊剂的使用,表面残留时用酒精擦洗干净。
g.尽可能减少在层叠台上对电池片的返修,防止异物落入杜绝二次污染。
h.管理人员每天对层压机设定的工艺值进行确认。
3、黑片
产生的原因:
a.正负极互联条短路。
b.互联条虚焊。
c.接线盒二极管焊反或接线异常。
d.测试机外接线异常。
预防措施:
a. 串焊接时防止电池片边缘处残留焊锡。
b. 防止温度低时造成虚焊。
c. 初测时重点检查图像。
d. 终测后异常要折框换片。
e. 黑片时检查接线盒二极管焊接及引线焊接。
f. 检查测试机外接线。
4、锡渣不良
产生的原因:
a.焊接时锡渣残留。
b.底板上粘有锡渣。
c.换片时在组件上进行焊接作业。
预防措施:
a. 焊接作业时及时清理烙铁头堆锡,防止锡渣掉下。
b. 及时清理底板卫生,杜绝锡渣残留。
c. 请勿在层叠好的组件上更换焊接电池片。
d. 串焊后及时检查电池片上是否有锡渣残留。
5、异物
产生的原因:
a.焊接人员作业时异物粘到电池片上。
b.焊接底板上的脏物。
c.层叠时玻璃底板、EVA 粘有脏物。
d.层叠人员作业时头发、脏物等掉到电池片上。
e.初测不良更换片时二次污染。
预防措施:
a. 焊接、层叠人员按规定着装,将头发包在洁净帽内。
b. 层叠人员作业时注意检查玻璃底板、EVA污染状况。
c. 焊接台、焊接底板、焊接周转盒、层叠台卫生定时清扫。
d. 焊接间、层叠区域定期用湿尘拖清扫区域卫生,保持地面无异物。
e. 人员洁净服要定期清洗干净。
6、裂片
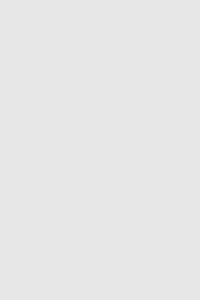
产生的原因:
a.单串焊接时手势过重致使造成。
b.互联条焊接时有点状堆锡、虚焊,造成层压裂片。
c.层叠、层压人员在抬层叠好的电池片时人员手接触压到电池片。
d.电池片本身质量,隐裂所致。
e.层压机加压阶段压力大导致。
f.EVA不平整(鼓包现象严重)。
组件影响
a.裂片部分失效影响组件功率衰减。
b.单片电池片功率衰减或完全失效影响组件功率衰减。
预防措施:
a. 层叠、层压人员在抬层叠好的电池片时手不要接触边上的电池片。
b. 层叠、层压人员在抬层叠好的电池片时要防止碰到放台车上的横杆上。
c. 焊接人员焊接时防止出现堆焊、虚焊异常现象。
d. 初测时认真分析每一个图片,杜绝隐裂片流入层压组。
7、焊带偏移(露白)
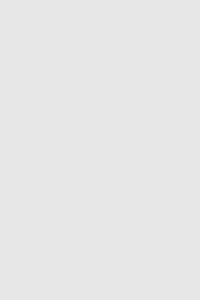
产生的原因:
a.焊接时互联条定位与电池片上的焊接印刷线位置产生偏离现象。
b.作业时互联条起点焊歪,造成偏移。
预防措施:
a.电池片在底板上位置放偏会造成焊带偏移现象。
b.电池片原材主栅线偏移会造成焊接后焊带与主栅线偏移。
c.焊带变形的互联条不能使用。
8、虚焊、过焊
产生的原因:
a.焊接温度过低。
b.助焊剂过少。
c.速度过快会导致虚焊。
d.焊接温度过高或焊接时间过长会导致过焊现象。
组件影响
a.虚焊在短时间出现焊带与电池片脱层,影响组件功率衰减或失效。
b.过焊导致电池片内部电极被损坏,直接影响组件功率衰减降低组件寿命或造成报废。
预防措施:
a.确保焊接温度参数设定,并要定期检查,焊接时间为3—4秒。
b.返修时更要确保烙铁的温度、焊接时间和使用助焊剂。
c.加强EL检验力度,避免不良漏失下一工序。
d.定期对互联条的浸泡液及时间进行管理。
9、色差
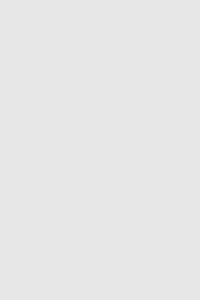
产生的原因:
a.分选人员存在颜色误区(应区分单片的浅、中、深)。
b.修复人员更换单片容易造成色差。
预防措施:
a.分选人员严格把控色差,统一分类。
b.对更换不良单片要说明色差情况。
c.单串焊人员要有自检意识,杜绝色差流入下道工序。
d.反光检验人员要仔细检查,对色差及时反馈。
e.修复人员返修前要查看其色差问题。
10、型材不良
产生的原因:
a.来料存在问题。
b.加工过程中撞击所致。
c.清理过程刀片、锉刀划伤。
预防措施:
a.操作人员对使用材料要有自检能力。
b.装框过程要注意运作,时常查看装框后的效果。
c.抬组件时要拿稳。
d.清理时用刀片、锉刀要小心。
e.技术员要对装框后的尺寸进行管理确认。
11、胶汽泡
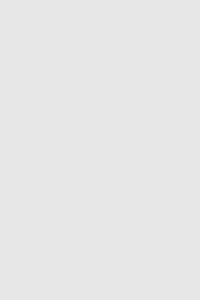
产生原因:
a.胶气泡主要是胶原材内有气泡或气枪气压不稳造成。
b.缝隙主要原因是员工手法打胶不标准造成。
组件影响
有缝隙的地方会有雨水进入,雨水进入后组件工作时发热会造成分层现象。
预防措施:
a.加强人员技能培训,增强自检意识。
b.人员打胶方法要规范。
c.清洗人员严格检验。
d.注意调整气枪压力。