换热器在化工、石油、治金等领域中应用十分广泛,据统汁,换热器的损坏率在所有化工设备损坏的比例中所占的比重最大,而且其损坏容易引起泄露爆炸等事故。
所以一定要知道换热器存在哪些安全隐患,及时采取措施才能防止悲剧的发生。

换热器的事故类型主要有燃烧爆炸严重泄漏和管束失效三种。

自制换热器,盲目将设备结构和材质做较大改动,制造质量差,不符合压力容器规范,设备强度大大降低。
焊接质量差,特别是焊接接头处未焊透,又未进行焊缝探伤检查、爆破试验,导致焊接接头泄漏或产生疲劳断裂,进而大量易燃易爆流体溢出,发生爆炸。
由于腐蚀(包括应力腐蚀、晶间腐蚀),耐压强度下降,使管束失效或产生严重泄漏,遇明火发生爆炸。
换热器做气密性试验时,采用氧气补压或用可燃性精炼气体试漏,引起物理与化学爆炸。
操作违章、操作失误,阀门关闭,引起超压爆炸。
长期不进行排污,易燃易爆物质(如三氯化氮)积聚过多,加之操作温度过高导致换热器(如液氯换热器)发生猛烈爆炸。
过氧爆炸。
换热器设计、制造应符合国家压力容器的规范要求,图纸修改与变动必须经主管部门同意,经验收质量合格。
制造换热器时,要保证焊接质量,并对焊缝进行严格检查。
流体为腐蚀介质时,提高管材质量和焊接质量,增加管壁厚度或在流体中加入腐蚀抑制剂。
定期检查管子表面腐蚀情况和对易腐蚀损坏的设备进行检测,采取有效措施。
换热器做气密性试验时,必须采用干燥的空气、氮气和其他惰性气体,严禁使用氧气和可燃性气体试漏或补压。
严禁违章操作,严格执行操作规程。
对于易结垢的流体可定期进行清洗,将结垢清洗掉。
严格控制氧的含量。
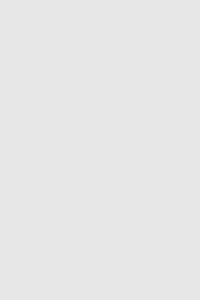
因腐蚀(如蒸汽雾滴、硫化氢、二氧化碳)严重,引起列管泄漏。
由于开停车频繁,温度变化过大,设备急剧膨胀或收缩,使花板胀管泄漏。
换热器本身制造缺陷,焊接接头泄漏。
因操作温度升高,螺栓伸长,紧固部位松动,引起法兰泄漏。
因管束组装部位松动、管子振动、开停车和紧急停车造成的热冲击,以及定期检修时操作不当产生的机械冲击而引起泄漏。
定期进行清洗;选择耐蚀管材;流体中加入腐蚀抑制剂;控制管内流速;视泄漏情况决定停车更换或采取堵漏措施。
精心操作,控制系统温度不要发生较大的波动。
保证焊接质量,对焊缝进行认真检查。
尽量减少法兰连接,升温后及时重新紧固螺栓,紧固作业要力求方便。
对胀管部位不允许有泄漏的换热器宜采取焊接装配。
换热器多用碳钢制造,冷却水中溶解的氧所致的氧极化腐蚀极为严重,管束寿命往往只有几个月或一二年。
管子与管板的接头是管束上的易损区,许多管束的失效都是由于接头处的局部腐蚀所致。
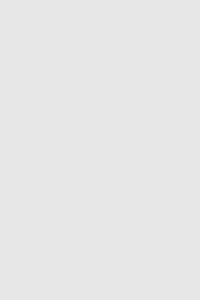
在换热器操作中,管束内外壁都可能会结垢,而污垢层的热阻要比金属管材大得多,从而导致换热能力迅速下降,严重时将会使换热介质的流道阻塞。
为强化传热和减少污垢层,通常采用增大壳程流体流速的方法。而壳程流体流速增加,产生诱导振动的可能性也将大大增加,从而导致管束中管子的振动,最终致使管束破坏。
常见的破坏形式有以下几种。
碰撞破坏
当管子的振幅足够大时,将致使管子之间相互碰撞,在碰撞中,管壁磨损变薄,最终发生开裂。
折流板处管子切开
折流板孔和管子之间有径向间隙,当管子发生横向振动的振幅较大时,就会引起管壁与折流板孔的内表面间产生反复碰撞。
由于折流板厚度不大,管壁多次、频繁与其接触,将承受很大的冲击载荷,因而在不长的时间内就可能发生管子被切开的局部性破坏。
管子与管板连接处破坏
此种连接结构可视为固定端约束,管子振动产生横向挠曲时,连接处的应力最大,因此,它是最容易产生管束失效的地区之一。
此外,壳程接管也多位于管板处,接管附近介质的高速流动更容易在此区域内产生振动。
材料缺陷的扩展造成失效
如果管子材料本身存在缺陷(包括腐蚀和磨蚀产生的缺陷),那么在振动引起的交变应力作用下,位于主应力方向上的缺陷裂纹就会迅速扩展,最终导致管子失效。
振动交变应力场中的拉应力还会成为应力腐蚀的应力源
流动诱导振动引起管子破坏,易发生在挠度相对较大和壳程横向流速较高的区域。
此区域通常是U形弯头、壳程进出口接管区、管板区、折流板缺口区和承受压缩应力的管子。
定期清洗管束;
合理选材;
在流体中加入缓蚀剂;
选择适当流速;
在流体入口设置过滤装置和缓冲结构等。
制定合理的开停工程序,加强在线监测,严格控制运行条件,在流体入口前设置缓冲板,减少脉冲;
优化结构设计,适当减小折流板间距,增大管壁厚度和折流板厚度;
折流板上的管孔与管子采用紧密配合,间隙不要过大;
改变支撑物形式,如折流板改为折流杆式,可有效消除流体诱导振动。
另外,降低壳程流体流速是防止管束振动最直接的方法,但同时传热效率也会随之降低。