车削加工废品多?这一篇正是你需要的,90条围绕车外圆、端面、切断、沟槽、镗孔、铰孔、滚花、螺纹等加工时产生的废品,分析产生原因、提供预防的小技巧: 
车外圆时产生废品的原因和预防方法 产生原因: 操作者看错图样或刻度盘使用不正确
车削时盲目进给,没有进行试切削 量具有误差或测量不正确 由于切削热的影响,使工件尺寸发生变化
预防方法: 车削前读懂图样,看清尺寸要求,正确使用刻度盘,看清格数 根据加工余量算出背吃刀量,进行试切削
量具使用前,必须进行仔细检查和调整零位,正确掌握测量方法 不能在工件温度较高时测量。 如果要测量,应该掌握工件的收缩情况,或在车削时浇注切削液,降低工件的温度
产生原因: 用一夹一顶或两顶尖装夹工件时,后顶尖轴线不在车床主轴轴线上 用小滑板进给车外圆时产生锥度 车床导轨与主轴轴线不平行 工件装夹长度较长,车削时因切削力影响使前端让刀,产生锥度 刀具中途逐渐磨损
预防方法: 车削前必须调整尾座轴线,使其位置准确,没有锥度 车削前必须事先检查小滑板上的刻线是否跟中滑板刻线的“0”对准 调整车床主轴跟床身导轨的平行度 车削时采用一夹一顶的装夹方法增加装夹刚度 根据工件材料选择合适的刀具材料或适当降低切削速度
产生原因: 车床刚度不足,如拖板镶条过松,传动零件(如带轮)不平衡或主轴太松引起振动 车刀的刚度不足或装夹不正确引起振动
工件的刚度不足引起振动 车刀的几何角度不正确 切削用量选择不当
预防方法: 消除或防止由于车床刚度不足引起的振动 增加车刀的刚度和正确装夹车刀 增加工件的装夹刚度 根据工件材料选择合理的车刀角度 进给量不宜太大,精车余量和切削速度选择适当

车端面和阶台时产生废品的原因和预防方法 产生原因: 用右偏刀从外向中心进给时,床鞍没固定,车刀扎入工件产生凹面 车刀不锋利,小滑板太松或刀架没锁紧,使车刀在切削力的作用下产生“ 让刀”,因而产生凸面 车刀装夹不正确产生凸面
预防方法: 在车大端面时,必须把床鞍的固定螺钉锁紧 保持车刀锋利,调整中小拖板的镶条,使其不能太松,车刀刀架应锁紧 车刀装夹必须正确,使主偏角≥93°
产生原因: 较低的阶台是由于车刀装夹歪斜,使主切削刃跟工件轴线不垂直 较高的阶台不垂直的原因跟端面凹凸的原因一样
预防方法: 车刀安装必须正确,使主切削刃垂直于工件的轴线;车阶台时最后一刀应从阶台里面向外车出 车削时,保持车刀切削刃锋利,调整中小拖板的镶条,使其不能太松;锁紧车刀刀架
切断和车沟槽时产生废品的原因及预防方法
产生原因: 主切削刃太宽或太窄 没有及时测量或测量不正确 尺寸计算错误
预防方法: 根据沟槽宽度刃磨主切削刃宽度 切槽及时,测量正确 仔细计算尺寸,留有磨削余量的工件,切槽时必须把磨削余量考虑进去
产生原因: 切断刀强度不够,主切削刃不平直,切削时由于侧向切削力的作用使刀具偏斜,致使切下的工件凹凸不平 刀尖圆弧刃磨或磨损不一致,使主切削刃受力不均而产生凹凸面 切断刀装夹不正确 刀具角度刃磨不正确,两副偏角过大而且不对称,从而降低刀头强度,产生“ 让刀”现象
预防方法: 增加切断刀的强度,刃磨时必须使主切削刃平直 刃磨时保证两刀尖圆弧对称 正确装夹切断刀 正确刃磨切断刀,保证两副偏角对称
产生原因: 两副偏角太小,产生摩擦 切削速度选择不当,没有加切削液 切削时产生振动 切屑拉毛已加工表面
预防方法: 正确选择两副偏角 选择适当的切削速度,并浇注切削液 采取防振措施
控制切屑的形状和排除方向
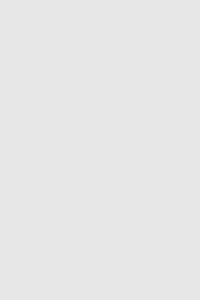
镗孔时产生废品的原因 产生原因: 车床床身导轨的不均匀磨损(靠近床头部分磨损严重)、床身水平面内产生扭曲以及车床主轴与床身导轨不平行,都会造成进给轨迹与工件轴线不平行,使镗出的孔产生锥度 镗较深的孔时,由于刀杆刚度不足,镗刀磨损,切削力增大而产生“让刀”现象,或刀杆因歪斜与孔壁相碰,都会使孔出现锥度
产生原因: 车床主轴轴承磨损,镗出的孔会呈椭圆形或棱圆形 薄壁工件在卡盘上夹持太紧,造成工件孔变形 在使用中心架镗孔时,若中心架的三个支承爪支顶工件太松或工件支承部位不圆,也会镗出椭圆或棱圆孔
产生原因: 车床主轴轴承间隙太大,镗孔时工件有振动,造成孔壁有振痕,不光洁 镗刀角度选择不合理,如后角过小、刀尖圆弧半径较大、主偏角过小等都会造成径向力增大,而使刀具产生振动,使孔不光洁 镗刀磨损、镗刀刀杆刚度不足也都会引起刀具振动,使孔壁出现振痕,表面粗糙度值加大
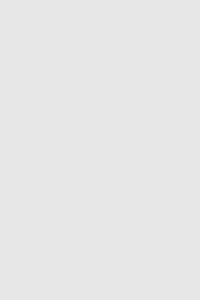
铰孔时产生废品的原因 产生原因: 车床尾座套筒中心与主轴中心不一致,尾座偏斜,使铰刀与孔中心不重合,若铰刀与尾座套筒间采用刚性连接,则铰出的孔径会扩大 铰刀刃口径向振摆过大,切削速度太高,使铰刀温度升高,产生积屑瘤等都会使孔径扩大 铰削余量过大、铰前孔不圆等都会造成铰孔铰刀振动,使孔径扩大
产生原因: 铰刀切削刃不锋利及切削刃上有裂口或崩刃,会使铰孔不光洁或铰出的孔有刮痕。 铰削余量过大或过小,铰前孔不圆,都将使铰出的孔有振痕,不光洁 铰削时如产生积屑瘤,则孔的表面粗糙度值会显著加大,所以铰削速度一定要在避免积屑瘤产生的切削速度范围内选取 冷却润滑液选取不当或没有浇到切削区域,都会增大孔的表面粗糙度值
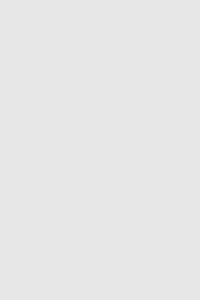
车圆锥时产生废品的原因及预防方法
用转动小滑板法车削时: 产生原因: 小滑板转动角度计算错误 小滑板移动时松紧不匀
预防方法: 仔细计算小滑板应转的角度和方向 调整镶条使小滑板移动均匀
用偏移尾座法车削时: 产生原因: 尾座偏移位置不正确 工件长度不一致 中心孔深浅不一致
预防方法: 重新计算和调整尾座偏移量 加工数量较多,各工件的长度、中心孔尺寸必须一致
用仿形法车削时: 产生原因: 装置的仿形角度调整不正确 滑板跟靠板配合不良
预防方法: 重新调整仿形装置角度 调整滑块和仿形装置之间的间隙
用宽切削刃车削时: 产生原因: 装刀不正确 切削刃不直
预防方法: 刀具安装正确后,调整切削刃的角度 修磨切削刃的直线度
铰内圆锥时: 产生原因: 铰刀锥度不正确 铰刀的装夹轴线跟工件旋转轴线不同轴
预防方法: 修磨铰刀 用百分表和试棒调整尾座轴线
产生原因: 车刀没有对准工件轴线 预防方法: 车刀必须严格对准工件轴线 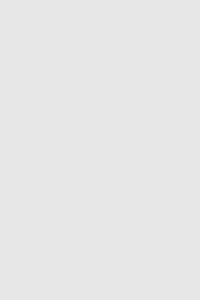
车削特形面时产生废品的原因及预防方法 产生原因: 采用双手控制法车削时,双手的配合速度(纵、横向进给)不协调 采用成形车刀车削时,切削刃形状与工件曲面轮廓不符,刀具装斜或切削刃没有严格对准工件中心 采用靠模法车削时,靠模体本身轮廓曲线有误差、安装得不正确或靠模传动机构中存在间隙。 车削过程中刀具切削刃磨损及工件切削余量不均 采用专用装置车削特形面时,如用圆筒形刀具车削,圆筒形刀具内径不符;如采用蜗杆蜗轮式车内、外圆弧,刀尖与蜗轮中心线的位置距离与圆弧半径有误差
预防方法: 分析零件上曲面各点的斜率,然后根据斜率确定纵、横进给速度 由于切削刃形状由工件曲面轮廓决定,所以,刃磨时要用样板对照找准,如果工件曲面精度要求较高,可以在工具磨床上刃磨刀具。 车刀安装正确,不能歪斜,严格对准工件中心 选择合适的靠模体、正确安装靠模装置,调整靠模传动机构中的间隙。 正确刃磨和使用车刀,保证车刀切削刃的锋利性。 加工时选择合适的切削用量及保证工件精车余量均匀 圆筒形刀具内径应按计算后实际尺寸选择及刃磨;调节刀尖与蜗轮中心线的位置,使其距离与半径相等
产生原因: 采用双手控制法车削时,双手进给速度过快、进给量过大或圆弧车刀切削刃不光滑、磨损;刀头伸出过长,车床主轴间隙过大或机床各部分的配合间隙过大,切削时产生振动 采用成形车刀车削时,刀具几何角度不合理、切削刃磨损或切削刃过宽,切削时产生振动;没有加注切削液或切削液选择不当 采用靠模法车削时,进给量过大,传动机构中存在间隙,使车削时刀具窜动 采用专用装置车削特形面时,专用装置本身传动机构有间隙误差
预防方法: 协调进给速度、采用较低的切削速度和较小的进给量,选择切削刃光滑、锋利的刀具;调节车刀刀头伸出的长度,调节主轴轴承间隙及机床各部分的配合间隙 选择合理的刀具角度,保证切削刃锋利,控制切削刃宽度;加注充足的切削液 合理选择切削用量,调节传动机构中存在的间隙 消除专用装置本身传动机构的间隙
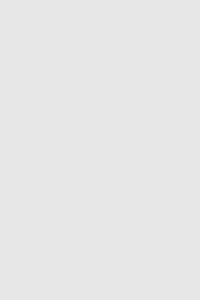
滚花时产生乱纹的原因及预防方法 产生原因: 开始滚花时,由于滚花刀滚轮和工件表面接触面较大,单位面积上径向压力较小或者因滚花刀压紧力过小,使工件表面塑性变形不明显,而使滚压出的花纹较浅,出现乱纹 滚花刀转动不灵活,滚轮与刀杆配合间隙过大或滚花刀本身齿纹中有残留的细屑及轮齿磨损都会导致乱纹 主轴转速过快,滚花刀轮齿选择不合理(过小),而使滚花刀与工件表面产生滑动,造成乱纹 滚花时,工件外圆周长不能被滚轮节距整除时而出现乱纹
预防方法: 开始滚花时,可以将滚花刀装偏一些,增大单位面积上的作用力,使工件表面塑性变形加大,从而得到较深、清晰的花纹 清洗润滑滚花刀,清除花纹中残留的细屑,必要时更换滚花刀 选择合理的主轴转速,一般取主轴转速较慢为最佳,同时选择合适的滚花刀轮齿 选择合适的外径尺寸,一旦发现更换不同轮齿的滚花刀或将工件外径车小一些,重新滚压
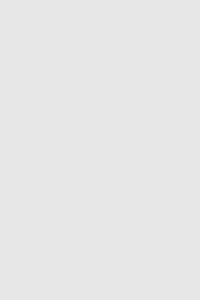
车螺纹时产生废品的原因及预防方法 产生原因: 交换齿轮计算或搭配错误或进给箱手柄位置放错,使螺纹全长螺距都不正确 车床丝杠本身的螺距误差或主轴和丝杠的轴向窜动,螺纹局部上螺距不正确,此外从主轴到丝杠之间的齿轮传动有误差也会影响螺距误差 开合螺母镶条松动,导致床鞍移动时出现窜动
预防方法: 校验,认真计算交换齿轮齿数,并进行合理搭配,根据螺距大小合理放置手柄位置 车削螺纹前,将主轴与丝杠轴向窜动和开合螺母的间隙进行调整,并将大滑板的齿轮与传动齿条脱开,使大滑板能匀速运动 调整开合螺母镶条,必要时在手柄上挂重物
车刀刀尖角刃磨误差,导致车削后螺纹牙型不正确 车刀装夹不正确,产生螺纹半角误差,导致车削后螺纹倒牙或牙型歪斜 车刀在车削过程中磨损,导致车削后螺纹牙底不清和螺纹两侧面不平直
预防方法: 正确刃磨螺纹车刀刀尖角,根据径向前角的大小对刀尖角进行修正;并用螺纹角度样板认真测量校对 正确装夹车刀,安装时采用螺纹样板对刀,车刀刀尖严格对准主轴中心线 选择合理的切削用量、切削液和及时修磨车刀
产生原因: 螺纹大径不正确,主要是由于车削螺纹前,外圆尺寸与螺纹大径的实际尺寸不符 螺纹中径不正确,主要是由于吃刀太大而又未及时正确测量,因而造成螺纹的中径误差 螺纹小径不正确,一方面是车削过程中车刀刀尖磨损过大,导致车削螺纹后中径合格、小径不合格的情况;另一方面是螺纹的总背吃刀量大于或小于牙型高度 螺纹牙底不清或有毛刺,造成实际尺寸与测量尺寸有误差 螺纹车刀装夹时偏斜,使牙型偏歪,影响尺寸 车刀刀尖角不正确,会造成车削后螺纹尺寸不正确
预防方法: 计算螺纹大径,并正确车削螺纹大径的实际尺寸 车削时认真测量螺纹中径的实际尺寸 车削时经常检查车刀,发现磨损及时修磨,严格掌握螺纹的总背吃刀量与小径尺寸,并按计算尺寸车削 测量前去除毛刺,并保证牙底清晰 正确装夹螺纹车刀,采用螺纹角度样板校对车刀装夹 正确刃磨车刀刀尖角
产生原因: 车刀切削刃不锋利,车削时切削刃上产生积屑瘤 车削时没有及时加注冷却液,排屑不当而拉毛已加工表面 车刀伸出过长或刀杆刚性不够引起振动,造成车削后螺纹表面粗糙值大 车刀后角过小,造成车削时后面与螺纹两侧面摩擦,从而影响表面粗糙度 切削用量选择不合理 车床主轴间隙过大或机床各部分的配合间隙过大
预防方法: 认真刃磨刀具,保证车刀切削刃锋利 用高速钢车刀精车螺纹时,为降低表面粗糙度值,一般加注冷却液,使排屑顺畅 刀杆不能伸出过长,选择刀杆刚性强的螺纹车刀 根据螺纹螺旋升角大小,合理刃磨车刀后角 用高速钢螺纹车刀车削时,切削速度不要过大,背吃刀量小于0.06 mm。 用硬质合金车刀高速车螺纹时,最后一刀的背吃刀量要大于0.1 mm,使切屑垂直于工件轴线方向流出 调整车床主轴及各部分的配合间隙
产生原因: 车刀装得太低 刀杆刚性差或刀杆伸出过长 主轴轴承部分和滑板塞铁太松或中滑板丝杠间隙太大 车刀径向前角太大时,径向力把车刀拉向工件 工件刚性差,切削用量选择不合理,特别是背吃刀量较大时,容易产生扎刀和顶弯工件现象
预防方法: 安装车刀时,保证车刀刀尖与主轴旋转中心等高 刀杆不能伸出过长,选择刀杆刚性强的螺纹车刀 调整好丝杠螺母间隙,调整中滑板的丝杆间隙 减小径向前角 根据工件刚性大小来选择合理的切削用量
☞来源:金属加工整理 ☞本文编辑:Jacy ☞媒体合作: 010-88379864
|