简介
一、切屑的形成过程 1.变形区的划分 切削层金属形成切屑的过程就是在刀具的作用下发生变形的过程。图2-10是在直角自由切削工件条件下观察绘制得到的金属切削滑移线和流线示意图。流线表明被切削金属中的某一点在切削过程中流动的轨迹。切削过程中,切削层金属的变形大致可划分为三个区域: (1)第一变形区 从OA线开始发生塑性变形,到OM线金属晶粒的剪切滑移基本完成。从OA线到OM线区域(图中Ⅰ区)称为第一变形区。 (2)第二变形区 切屑沿前刀面排出时进一步受到前刀面的挤压和摩擦,使靠近前刀面处的金属纤维化,基本上和前刀面平行。这一区域(图中Ⅱ区)称为第二变形区。 (3)第三变形区 已加工表面受到切削刃钝圆部分和后刀面的挤压和摩擦,造成表层金属纤维化与加工硬化。这一区域(图中Ⅲ区)称为第三变形区。
图2-10 金属切削过程中的滑移线和流线示意图
| 在第一变形区内,变形的主要特征就是沿滑移线的剪切变形,以及随之产生的加工硬化。在图2-11中,OA、OB和OM等都是等剪应力曲线。P点金属在切削过程中向刀具移动,到达点1时,其剪应力达到材料的屈服强度 。过点1后,P点在继续向前移动的同时,也沿OA滑移,合成运动将使其从点1流动到点2,就是它的滑移量。随着滑移的产生,剪应变将逐渐增加,直到P点金属移动到超过点4位置后,其流动方向与前刀面平行,不再沿滑移线滑移,OA称作始滑移线,OM称作终滑移线。
 图2-11 第一变形区金属的剪切滑移
|
|

当金属沿滑移线发生剪切变形时,晶粒会伸长,如图2-12所示。晶粒伸长的方向与滑移方向(即剪切面方向)是不重合的,它们成一夹角 。据研究,在一般切削速度范围内,第一变形区的宽度仅为 ,所以可以用一剪切面来表示(图2-12)。剪切面与切削速度方向的夹角称作剪切角,以 表示。我们可以用图2-13形象地模拟塑性金属切屑形成过程,被切削金属层好比一叠卡片(图中用阴影平行四边形暗区 , , , ,…表示),刀具切入时,卡片之间发生滑移,阴影暗区 , , , ,…的金属被移到图中1,2,3,4,…的位置。卡片之间滑移的方向就是剪切面的方向。
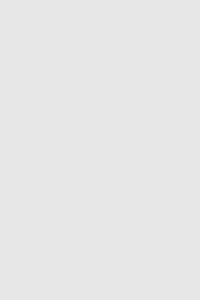
图2-12 滑移与晶粒的伸长
|
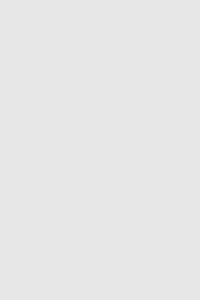 图2-13 切屑形成过程示意图
|
2.切屑的受力分析 在直角自由切削的情况下,作用在切屑上的力有:前刀面上的法向力 和摩擦力 ;剪切面上的正压力 和剪切力 ;这两对力的合力互相平衡,如图2-14所示。如将上述两对力都画在切削刃的前方,就可得到图2-15所示的力关系图。图中 是 和 的合力,称为切屑形成力; 是剪切角; 是 和 的夹角,叫摩擦角; 是刀具前角; 是切削运动方向的切削分力; 是垂直于切削运动方向的切削分力; 是切削厚度。
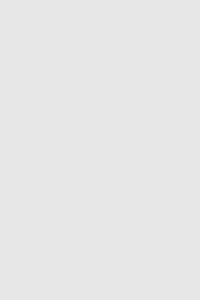 图2-14 作用在切屑上的力
|
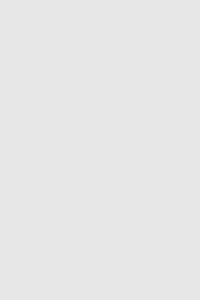 图2-15 直角自由切削时力与角度的关系
|
令 表示切削宽度, 表示切削层公称横截面积( ), 表示剪切面的面积( ), 表示剪切面上的剪应力,则
(2-8)
(2-9)
(2-10) 如用测力仪直接测得作用在刀具上的切削分力 和切削分力 ,在忽略被切材料对刀具后刀面作用力的条件下,即可由式(2-9)与式(2-10)推导求得前刀面对切屑作用的摩擦角 ,进而可近似求得前刀面与切屑间的摩擦系数μ。 以式(2-10)除以式(2-9)得
二、切削变形程度 切削变形程度有三种不同的表示方法,分述如下。 1.变形系数 在切削过程中,刀具切下的切屑厚度 通常都大于工件切削层厚度 ,而切屑长度 却小于切削层长度 ,如图2-16所示。切屑厚度 与切削层厚度 之比称为厚度变形系数 ;而切削层长度 与切屑长度 之比称为长度变形系数 。由图2-16知 (2-11)
由于切削层变成切屑后,宽度变化很小,根据体积不变原理,可求得
与 可统一用符号 表示。变形系数 的值是大于1的数,它直观地反映了切屑的变形程度, 越大,变形越大。 值可通过实测求得。 由式(2-11)知, 与剪切角 有关, 增大, 减小,切削变形减小。
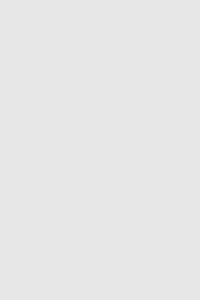 图2-16 变形系数 的计算
|
2.相对滑移 既然切削过程中金属变形的主要形式是剪切滑移,当然就可以用相对滑移(剪应变) 来衡量切削过程的变形程度。图2-17中,平行四边形OHNM发生剪切变形后,变为平行四边形OGPM,其相对滑移
(2-12)
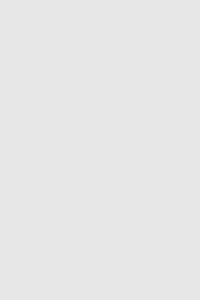 图2-17 剪切变形示意图
|
3.剪切角 由式(2-11)知,剪切角 与切削变形有密切关系,我们也可以用剪切角 来衡量切削变形的程度。 在剪切面上,金属产生了滑移变形,最大剪应力就在剪切面上。图2-15为直角自由切削状态下的作用力分析,在垂直于切削合力 方向的平面内剪应力为零,切削合力 的方向就是主应力的方向。根据材料力学平面应力状态理论,主应力方向与最大剪应力方向的夹角应为45°,即 与 的夹角应为45°,故有
则 (2-13) 分析上式可知: 1)前角 增大时,剪切角 随之增大,变形减小。这表明增大刀具前角可减少切削变形,对改善切削过程有利。 2)摩擦角 增大时,剪切角 随之减小,变形增大。提高刀具刃磨质量、采用润滑性能好的切削液可以减小前刀面和切屑之间的摩擦系数,有利于改善切削过程。
三、前刀面上的摩擦 经测定,切削钢材时,刀具前刀面对被切材料产生的正应力 和切向应力 沿前刀面的分布如图2-18所示[13]。在切屑与刀具前刀面接触的OB长度内存在两种不同的接触状态。在靠近切削刃的OA区,由于正应力值大,切屑在前刀面上形成粘结接触,在此长度上,各点的切应力 基本相同,它等于被切材料的剪切屈服强度 ;在AB区,由于正应力小,切屑在前刀面上形成滑动接触,切屑相对于前刀面的摩擦特性服从古典摩擦法则,各点的摩擦系数 相同,切应力 。
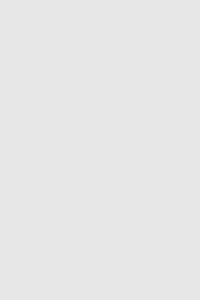 图2-18 刀屑界面上正应力和切应力的分布
|
由于在一般切削条件下,来自粘结接触区的摩擦力占前刀面上总摩擦力的85%[13],故在研究前刀面上的摩擦时,应以粘结接触区的摩擦为主要依据。 粘结接触区上各点的摩擦系数
式中 ——距切削刃 点处的正应力。 由于 随 变化,故在粘结接触区切屑与前刀面的摩擦系数是一个变值,离切削刃越远,摩擦系数越大,其平均摩擦系数
(2-14) 式中 、 ——分别为粘结接触区的摩擦力和正压力;
——切削层公称宽度;
——粘结接触区平均正应力。
四、积屑瘤的形成及其对切削过程的影响 1.积屑瘤的形成及其影响 在切削速度不高而又能形成带状切屑的情况下,加工一般钢料或铝合金等塑性材料时,常在前刀面切削处粘着一块剖面呈三角状的硬块(图2-19),它的硬度很高,通常是工件材料硬度的2~3倍,这块粘附在前刀面上的金属称为积屑瘤。 切削时,切屑与前刀面接触处发生强烈摩擦,当接触面达到一定温度,同时又存在较高压力时,被切材料会粘结(冷焊)在前刀面上。连续流动的切屑从粘在前刀面上的底层金属上流过时,如果温度与压力适当,切屑底部材料也会被阻滞在已经“冷焊”在前刀面上的金属层上,粘成一体,使粘结层逐步长大,形成积屑瘤。积屑瘤的产生及其成长与工件材料的性质、切削区的温度分布和压力分布有关。塑性材料的加工硬化倾向越强,越易产生积屑瘤;切削区的温度和压力很低时,不会产生积屑瘤;温度太高时,由于材料变软,也不 易产生积屑瘤。对碳钢来说,切削区温度处于300~350℃时积屑瘤的高度最大,切削区温度超过500℃积屑瘤便自行消失。在背吃刀量 和进给量 保持一定时,积屑瘤高度 与切削速度 有密切关系,因为切削过程中产生的热是随切削速度的提高而增加的。图2-20中,Ⅰ区为低速区,不产生积屑瘤;Ⅱ区积屑瘤高度随 的增大而增高;Ⅲ区积屑瘤高度随 的增大而减小;Ⅳ区不产生积屑瘤。
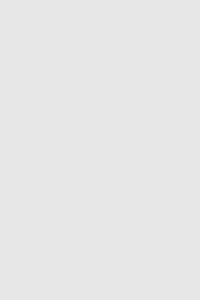
图2-20 积屑瘤高度与切削速度的关系
|
2.积屑瘤对切削过程的影响 (1)使刀具前角变大 阻滞在前刀面上的积屑瘤有使刀具实际前角增大的作用(参见图2-19),使切削力减小。 (2)使切削厚度变化 积屑瘤前端超过了切削刃,使切削厚度增大,其增量为 ,如图2-19所示。 将随着积屑瘤的成长逐渐增大,一旦积屑瘤从前刀面上脱落或断裂, 值就将迅速减小。切削厚度变化必然导致切削力产生波动。 (3)使加工表面粗糙度增大 积屑瘤伸出切削刃之外的部分高低不平,形状也不规则,会使加工表面粗糙度增大;破裂脱落的积屑瘤也有可能嵌入加工表面使加工表面质量下降。 (4)对刀具寿命的影响 粘在前刀面上的积屑瘤,可代替刀刃切削,有减小刀具磨损,提高刀具寿命的作用;但如果积屑瘤从刀具前刀面上频繁脱落,可能会把前刀面上刀具材料颗粒拽去(这种现象易发生在硬质合金刀具上),反而使刀具寿命下降。 积屑瘤对切削过程的影响有积极的一面,也有消极的一面。精加工时必须防止积屑瘤的产生,可采取的控制措施有: 1)正确选用切削速度,使切削速度避开产生积屑瘤的区域; 2)使用润滑性能好的切削液,目的在于减小切屑底层材料与刀具前刀面间的摩擦; 3)增大刀具前角 ,减小刀具前刀面与切屑之间的压力; 4)适当提高工件材料硬度,减小加工硬化倾向。 五、影响切屑变形的因素 在研究分析切削过程变形规律之后,我们来归纳一下影响切屑变形的一些主要因素,以便利用这些规律控制和优化切削过程。 1.工件材料 实验结果表明,工件材料强度越高,切屑和前刀面的接触长度越短,导致切屑和前刀面的接触面积减小,前刀面上的平均正应力 增大,前刀面与切屑间的摩擦系数减小(见式2-14),摩擦角 减小,剪切角 增大(见式2-13),变形系数 将随之减小。 2.刀具前角 由式(2-13)知,增大刀具前角 ,剪切角 将随之增大,变形系数 将随之减小;但 增大后,前刀面倾斜程度加大,切屑作用在前刀面上的平均正应力 减小,使摩擦角 和摩擦系数 增大(见式2-14)而导致 减小。由于后一方面影响较小, 还是随 的增加而减小。 1. 切削速度 在无积屑瘤产生的切削速度范围内,切削速度 越大,变形系数 越小。主要是因为塑性变形的传播速度较弹性变形慢,切削速度越高,切削变形越不充分,导致变形系数 下降;此外,提高切削速度还会使切削温度增高,切屑底层材料的剪切屈服强度 因温度的增高而略有下降,导致前刀面摩擦系数 减小,使变形系数 下降。 2. 切削层公称厚度 在无积屑瘤的切削速度范围内,切削层公称厚度 越大,变形系数 越小。这是由于 增大时,前刀面上的法向压力 及前刀面上的平均正应力 随之增大,前刀面摩擦系数 随之减小,剪切角 随之增大,所以 随 增大而减小。
|