摘要: 探索了航天电子产品CQFP封装器件焊接和粘接加固"一次成型”工艺。遴选了适用于再流焊温度的高温快速固化环氧粘接剂,通过工艺试验调整了印刷、点胶、贴片和再流焊工艺参数,并检测了焊点外观和粘接剂粘接界面,最终通过环境试验后的金相剖切验证了的焊点可靠性。结果表明,“一次成型”工艺能够实现在再流焊工序同步完成焊点钎焊和粘接剂固化,焊点和粘接质量满足标准要求,焊点可靠性能够满足航天电子产品型号环境试验条件要求。 CQFP(Ceramic Quad Flat Package,陶瓷四边引线扁平封装)器件以其高可靠性和优良的电气性能与散热性能,在航天等领域得到了广泛应用[1-2]。近年来,型号任务对航天电子产品的需求量日益增长,迫切需要在保证产品可靠性的同时,提高产品生产效率。现有大质量、大尺寸CQFP器件通常需要在器件本体底部点封环氧粘接剂以提升加固裕度,采用的装联工艺主要有2种[3]:1)先通过再流焊完成焊点钎焊,再通过PCB的预留孔于器件底部注入环氧粘接剂,室温固化;2)先在器件底部点封环氧粘接剂,然后贴片,室温固化后,手工完成焊点钎焊。这些工艺方法均存在不足之处:2种工艺下,环氧粘接剂固化时间均为小时级,且不能与其他工序同步开展,影响工艺全流程的装联效率;若采用手工焊接,不仅生产效率较低,焊点的一致性保障难度高;若采用预留孔注胶,对操作的手法要求极为严格,要保证粘接面积的同时,避免粘接剂污染焊点,也会对生产效率造成影响。 面对传统CQFP装联工艺生产效率较低和质量一致性难以保障的问题,木文通过工艺试验,对CQFP粘接固化、焊点钎焊在再流焊工序同步完成的工艺(后文简称“一次成型”工艺)进行了探索,并对新工艺下的焊点可靠性进行了验证。 由于需要通过再流焊工序同时实现焊点钎焊和底部粘接剂的良好粘接固化,所以试验首先需要选用满足航天材料要求且能够兼容有铅再流焊温度曲线的高温快速固化环氧粘接剂。遴选出材材适用的粘接剂后,通过焊接试验,确定焊膏印刷、点胶、贴片和再流焊工序的相关工艺参数,直到工艺参能使性焊点及底填粘接剂粘接质量满足标准要求。最后,使用新工艺参数焊接试验板组件,在经历环境试验考核后,通过金相剖切验证焊点可靠性。 本文是以CQFP256器件作为研究对象,如图1所示,其边长为37mm,引脚中心距0.5mm,引脚宽度为0.2mm,器件高0.5mm(器件本体底部到PCB上面的距离)。PCB材料为FR-4,焊盘设计尺寸为3.05lmm×0.30mm;焊料使用Sn63Pb37。 按Q/W-Q-70-01-2015《航天器材选用控制要求》[4]遴选在再流焊炉温下快速固化的环氧粘接剂,通过调研初步选取了6种工业领域中已成熟应用的粘接剂,并针对这6种粘接剂按照如图2所示的流程开展遴选。 在PCB上分别点涂6种环氧粘接剂,点涂范围为直径约1cm的圆形,点涂后将PCB放入再流焊炉中,使用典型再流焊曲线对其进行加热,检验出炉后环氧粘接剂外观,如图3所示。外观判定原则为环氧粘接剂固化表面必须平整,无表面开裂、气孔、凹凸等现象。因此,选取3号和5号环氧粘接剂进行下一步物理性能的测试筛选,考察其是否满足要求。 观根据要求,针对舱内使用的环氧粘接剂技术要求,对3号、5号粘接剂的真空质损、可凝挥发物、固化度、热稳定性、剪切强度和温循后剪切强度进行了测定,测试项目和方法、标准以及实测值详见表1,可知,3号环氧粘接剂的各项性能指标良好,满足要求。反之,5号环氧粘接剂由于不满足真空质损小于1%的要求,不具备低污染性而被剔除。因此,选取3号环氧粘接剂用于“一次成型”工艺试验。 CQFP“一次成型”工艺流程需要在传统再流焊工艺基础上加入点胶工序,并在再流焊工序同步完成粘接剂的固化,因而其完整工艺流程应由4个工序组成,依次为印刷焊膏、底部点胶、贴片和再流焊(粘接剂固化),如图4所示。因此,本研究将从这4个工序出发,开展工艺试验确定工艺参数。 按开口尺寸与焊盘尺寸1:1的比例设计并加工了0.13mm、0.15mm和0.18mm三种厚度的网板。 在无底部点胶的情况下,分别使用三种厚度的网板进行了焊膏印刷,在典型再流焊温度曲线下完成焊接。使用VS8在30倍倍数以上放大,对到焊点进行观察,如图5所示。考虑到底部点胶后受热过程中存在的热膨胀会抬高器件本体使钎缝扩大,因而选择了提供焊膏量更充足,能使焊点更为饱满的0.18mm厚度网板,进行底部点胶情况下的工艺参数摸索。 (a)0.13mm网板 (b)0.15mm网板 (c)0.18mm网板 结合网板厚度和器件本体底部与PCB的间隙、引脚厚度、贴片后引脚嵌入焊膏深度的尺寸,最终计算出底部粘接剂点胶高度应不低于0.61mm,才能保证器件底部粘接剂与器件本体底部良好粘接。因此,制作了0.7°-00.5mm厚的不锈钢点胶工装,如图6(a)所示。使用工装完成点胶后,通过刮刀取平的方式控制点胶高度,点胶完成状态如图6(b)所示。 在网板厚度和底部点胶高度已确定的基础上,为使贴片时设备能提供一定的预压力,保证贴片后引脚与焊膏、器件底部与粘接剂的良好接触,设定0.1mm、0.2mm和0.3mm的器件高度补偿参数进行贴片试验,最终得到贴片高度补偿参数为0.2mm时,既能满足引脚至少1/2厚度嵌入焊膏的要求,又可避免由于预压力过大导致引脚变形。贴片设备如图7所示,贴片完成后引脚与焊膏的接触状态如图8所示。
 典型再流焊曲线参数见表2。当再流焊温度升高至Sn63Pb37焊料熔点183℃时,焊料开始熔化,器件由于重力作用下沉,使针缝厚度控制在合理的范围。由此可知,若器件底部粘接剂在焊锡熔化前过早脱胶,失去流动性,将会阻止器件下沉,导致引脚和焊盘间焊缝过大,焊锡不能充分填充和爬升,从而不能形成合格焊点[5]。根据以上原则,首先通过介电固化[6]测试对3号环氧粘接剂在150℃、183℃的凝胶曲线进行了确定,如图9所示。

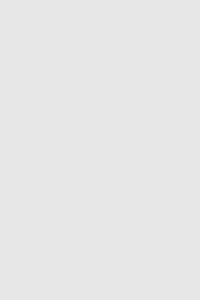 由图9(a)可知,恒温150℃时,3号环氧粘接剂凝胶时间为5.0min。而在预热区温度由室温升至150℃的时间仅为1.5min,且该区间的反应速率慢于恒温150℃时反应速率,由此推知,此阶段的固化反应程度较低,但已经形成一些交联结构,对凝胶有利。 由图9(b)可知,恒温183℃时,3号环氧粘接剂凝胶时间为2.0min。而曲型再流焊曲线要求保温和升温区(150℃~183℃)的时间上限恰为120s,虽然反应速率慢于恒温183℃时反应速率,但考虑到预热区(室温~150℃)对凝胶的贡献,仍需要缩短保温度和升温区(150℃~l83℃)的总时间,才可保证凝胶时刻滞后于焊料熔化时刻。根据此原则,通过调整再流焊炉工艺参数,得到如图10所示曲线。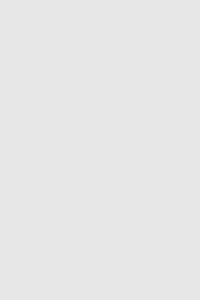 使用调整后的再流焊曲线完成焊接,如图11所示。为验证工艺参数的可行性,对焊点的外观和底填粘接剂的粘接情况进行了检验。首先,以光学焊点检测仪观察焊点外观,如图12所示,由图可知,焊点光亮饱满,脚跟、脚尖均形成了良好润湿角,焊锡爬升高度高于引脚上表面,满足ECSS-Q-ST-70-38C[7]标准中的焊点外观合格判据。然后,使用超声波扫描仪(C-SAM)对器件底部粘接情况进行C-SCAN(横截面扫描)[8],扫描结果如图13所示,由图可知,粘接剂与PCB表面及器件底部均形成了良好的粘接界面,没有分层、脱胶的情况出现,且没有对焊点和引脚等部位造成污染。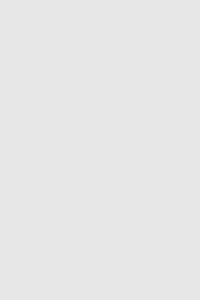 使用前文已确定的“一次成型”工艺参数制备1块CQFP组件(4个器件子样),进行力学和温度循环试验,试验条件详见表3。试验结束后对器件子样焊点进行剖切,选取3个器件,每个器件剖切4个焊点,剖切位詈如图14所示。4个焊点均给出剖切后的焊点金相显微照片,并选取其中1个焊点进行扫描电镜(SEM)检测。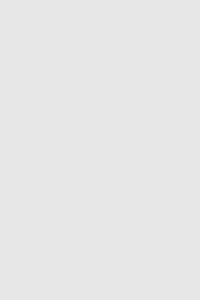
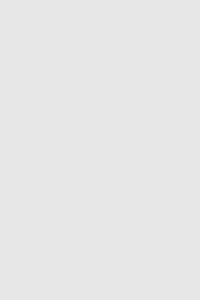
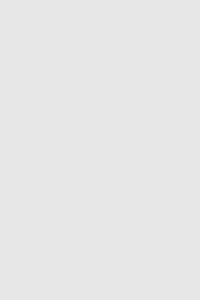
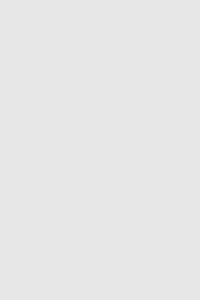 焊点金相显微镜及扫描电子显微镜照片如图15和图16所示,能谱分析结果见表4。由以上焊点的金相显微镜照片可以看出,焊点无裂纹缺陷,满足ECSS-Q-ST-70-38C标准中“环境试验后表贴焊点裂纹长度<25%”的要求。结合焊点扫描电镜照片以及图中各点的能谱分析结果可知,镀镍Fe-Co-Ni/Sn-Pb/Cu焊盘钎焊接头钎缝组织依次由靠近镀镍Fe-Co-Ni侧的Ni-Co扩散层(厚度为2µm)、(Cu,Ni)6Sn5金属间化合物层(厚度约为2µm)、Sn基固溶、Pb基固溶体和靠近Cu侧的Cu6Sn5金属间化合物层(厚度约为3µm)构成。钎缝组织中Sn基固溶体Pb基固溶体均匀分布,无明显偏析,两侧连续的(Cu,Ni)6Sn5金属间化合物与Cu6Sn5金属间化合物界面反应层表面平坦,厚度适中,说明“一次成型”再流焊接工艺参数下,焊料可以有效去除界面污染和氧化膜与两侧母材形成完整有效的冶金反应界面,实现良好可靠的机械连接与电气迕接。因此,“一次成型”工艺参数下焊点满足任务书规定的可靠性指标要求。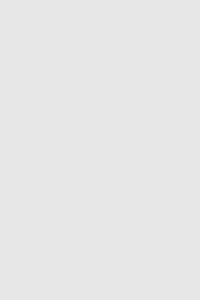
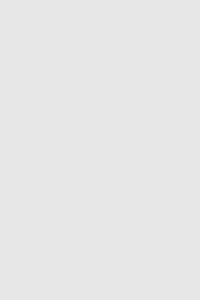 1)选用3号高温快速加固化环氧粘接剂,通过印刷、点胶、贴片参数调整保证贴装质量,结合再流焊工艺参数的调整来控制凝胶时间,可以实现CQFP器件焊接、粘固在再流焊工序同步完成,生产效率得到大幅提升,焊点外观、底部粘接质量满足航天电子产品标准要求;2)使用“一次成型”工艺装联的CQFP板组件,经航天型号环境试验考核后,焊点经金相剖切未发现裂纹缺陷,表明“一次成型”工艺下的加固效果和焊点可靠性能够满足航天电子产品型号环境试验条件要求。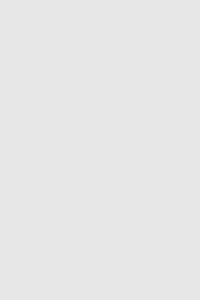
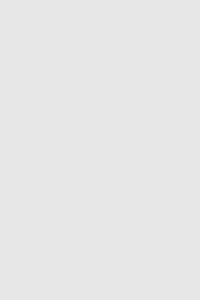
|