壳管蒸发器内制冷剂通过换热管与管内流体进行换热,制冷剂在此过程中发生相变,制冷剂传质量的多少决定了蒸发器换热量的大小。在壳侧流体相变过程中,换热管束排布会影响两相流型从而影响壳侧传质量和换热系数,因而需要针对满液式蒸发器工作时气泡的生成、运动规律对换热管束排布进行优化设计。本文我们就一起来看这个问题。 满液式壳管蒸发器基本结构如图1所示。其在稳定工作时,制冷剂液体从壳程进口进入筒体,水从管程进口进入换热管束,制冷剂通过换热管与管程的水进行换热,在筒体内沸腾,制冷剂蒸汽从壳程出口离开。图2(a)为正常工作时满液式壳管蒸发器的侧面剖视图。满液式壳管蒸发器在工作过程中,制冷剂从底部进入换热管束底部区域,换热管传递热量部分用于管外流体的潜热换热,流体在换热管外表面不断蒸发并生成大量气泡,气泡汇聚在一起形成气膜并粘附在管壁上。在靠近液面的上部区域,气泡尺寸、数量都显著增加。图2(b)为单根换热管壁面上制冷剂的蒸发过程。制冷剂在换热管壁上吸热发生相变从液体蒸发为气态,首先很小的气泡从换热管壁面上形成,在向上运动过程中气泡不断吸热,蒸发量增大,气泡也跟着长大,最后在换热管上部脱落,在液体中形成单独的气泡;来自换热管下方的气泡也会和换热管壁面上新生成的小气泡结合,形成大气泡。通过求解一组带有各相流体体积分数的控制方程,能够计算整个区域中所有网络中各相的体积分数,从而得到气液相界面。对于同种工质的蒸发冷凝问题,VOF方法中气相和液相的连续性方程如下:

 在上述控制方程中,连续性方程中传质源项、 动量方程中表面张力项和能量方程中潜热传热项 未知,需要分别建立子模型进行求解。 为了得到方程(1)、(2)中的蒸发量mሶ lg和冷凝量 mሶ gl,需要针对满液式壳管蒸发器工作特点建立相应 传质子模型。考虑到满液式壳管蒸发器中,传质主 要发生在换热管壁面上液面覆盖区域,而流动中气
泡在液体中运动时通过相界面发生的传质量较小。当换热管外壁面网格存在液相,且液相温度等 于或高于蒸发温度时,液相通过换热得到的热量用 于流体潜热传热,液相蒸发为气相,即外壁面网格
满足a1 > 0,Tl > Tsat,壁面上的蒸发量由下式计算得出: 为了得到动量方程(4)中的表面张力Fσ,在 VOF 方法中使用连续表面张力模型(Continuum
Surface Force Model,CSF)获得表面张力项。连续表面张 力模型中,气液相界面处的表面张力由表面张力系
数s和相界面正交方向的曲率决定,其计算公式如下: 由传质模型可知,能量方程(7)中的工质潜热换 热源项 Sh 由下式计算得出: 在对满液式蒸发器进行模拟时,由于换热管长 度相比换热管直径长得多,因此可采用二维模型。网格划分采用结构性网格,同时采用区域网格划分方法,在进出口、换热管壁面等流动复杂区域采用
较小的网格尺寸,在靠近壳程筒体等区域采用较大 的网格尺寸,兼顾了网格质量和计算速度的需求。模拟中使用的工质为 R134a,在表压260 kPa 工况下蒸发温度为 6 o C;进口边界条件为速度入口, 出口边界为压力出口,具体参数见表 1;换热管壁 面上采用第三类边界条件,其管内换热系数、管内 流体温度和壁厚见表 2,管内换热系数是通过换热管相变传热性能测试的数据拟合曲线得到;初始化中设置初始时刻液面位置比最上方换热管略高,即初始时刻工质完全浸没换热管束,且工质温度设置为 5.9 o C,略低于蒸发温度。计算区域边界条件及参数见图 3。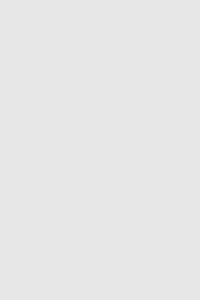 为了验证所建立的壳侧换热模型的正确性,对 原始排布样机进行仿真计算,并将结果与采用焓差 实验台的测试结果进行比较。实验工况、测量参数要求均满足热交换器及传热元件性能测试方法国家标准(GB/T 27698.1-2011和GB/T 27698.2-2011)。考虑到各传感器精度及测量误差,整个实验台系统误差小于标准规定的±5%。实验结果见表 3。使用所建立的模型对原始样机进行仿真所得的平均单管管外换热系数为 5,434
W/(m2 ·K)。仿真 结果误差不超过 5%,因此模型的计算结果与实验 结果符合较好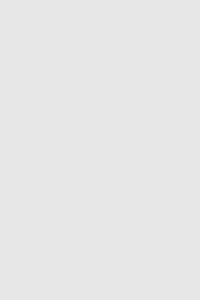 为了研究换热管横向间距对换热管束换热能力的影响,在单列管束研究中逐渐增大换热管横向 间距进行模拟,换热管横向间距从原始排布的 19.23 mm 增大至 23.23 mm。不同横向间距的管束结构的换热管壁表面平 均换热系数的变化规律如图 4 所示。增大管束间横
向间距能够有效地提升管束表面换热系数。当横向间距增大时,管外换热系数先迅速增大,后缓慢增大,当横向间距大于 22.23 mm后,换热系数增大 幅度不明显。这是由于管束横向间距增大后,气泡 更容易离开换热管壁面,减小气泡热阻,当管束间 距增大到一定程度时(以本文研究中的换热管为例,
横向间距为 22.23 mm),单管换热系数达到最大, 这时继续增大换热管横向间距对换热效果的提升 已经不再显著。从图 4 曲线中可以看出,当横向间 距为 22.23 mm 时,单列管束表面换热系数提升幅
度最大。对于不同型号和换热能力的换热器,不同横向 间距对单列管束表面换热系数的影响会随之变化, 横向间距的最优值也需要重新计算得出。为了研究换热管纵向间距对换热管束换热能 力的影响,在单列管束研究中逐渐增大换热管纵向 间距进行模拟,换热管纵向间距从原始排布的 22.2 mm 增大至 26.2 mm。不同纵向间距的管束结构的换热管壁表面平
均换热系数的变化规律如图 5 示。增大管束间纵向 间距能够有效地提升管束表面换热系数。当纵向间距增大时,管外换热系数先迅速增大,后缓慢增大, 当纵向间距大于 23.2 mm后,换热系数增大幅度不 明显。这是由于管束纵向间距增大后,气泡更容易 离开换热管壁面,减小气泡热阻,当管束间距增大 到一定程度时(以本文研究中的换热管为例,纵向
间距为 23.2 mm),单管换热系数达到最大,这时继 续增大换热管纵向间距对换热效果的提升已经不 再显著。从图 5 曲线中可以看出,当纵向间距为 23.2 mm 时,单列管束表面换热系数提升幅度最大。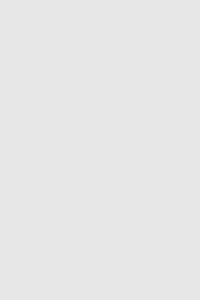 对于不同型号和换热能力的换热器,纵向间距 对单列管束表面换热系数的影响也会随之变化,纵 向间距的最优值需要重新计算得出。原有满液式壳管蒸发器换热管束间都采用相同的间距,导致中上部换热管附近的气泡无法及时 排出换热管区域,结合对单列管束的研究结果优化设计换热管束排布如图 6 示。优化后的换热管束分为四个区域,并在不同区域中采用不同的换热管间距,其中底部区域换热管排布较密,换热管间距较小,上部区域换热管排布较疏,换热管间距较大。此外,还在中上部区域内布置了气道,使气泡更快地通过换热管束区域,减小气泡与换热管接触造成 的热阻。对于不同换热能力的换热器,管束优化结构,可参照图 6 的方法进行调整和优化。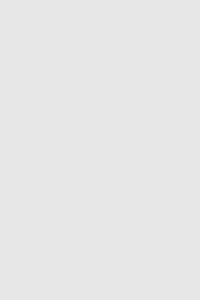 采用本文模型对优化结构进行仿真,并将其结 果与原始结构进行比较,如表 4 所示。在不同时刻
的优化排布比原始排布换热效果都好,优化后的换 热管束在 3 s 内的单管平均换热系数比原始排布高 14.4%。1)根据单列管束仿真结论对换热管间距进行适当优化后,单管平均换热系数 有所提高;2)在换热管不同区域采用不同的换热管间距可以使各区域的气泡都尽快离开换热管;3)在离两侧壳程筒体较远的中间区域,气泡可以通过纵向气道更快向上运动离开换热管束区域;4)优化后的换热管束拥有更多的区域,气泡容易通过不同区域间的空隙向两侧壳程筒体导走。根据表中数据可以看出,优化后的换热管排布可以有效提高单管平均换热系数,其幅度为 14.4%。根据本文提出的优化设计方法,对蒸发器管束 排布进行了优化设计,将换热管束分为多个区域, 在不同区域采用不同的换热管间距并布置纵向气
道,根据优化后的结构制造样机并进行实验。所用焓差实验台、实验工况、测量参数要求均满足热交换器及传热元件性能测试方法国家标准 (GB/T 27698.1- 2011 和 GB/T 27698.2-2011),考虑到各传感器精度及测量误差,整个实验台系统误差
小于标准规定的±5%。样机设计中将换热管数量从 原始排布的 169 根减少到优化设计后的 149 根,减少约 11%。对采用原始换热管排布的冷水机组,以 及根据优化原则设计的样机进行实验,其实验结果见表 5。从表中可以看出,蒸发器的单管换热量从原始 排布的 5.904 kW 增大到优化排布样机的 6.725 kW, 采用优化排布方案的蒸发器单管换热器,比原始排布的蒸发器大13.9%。其原因在于,优化后的换热管束排布能够使气泡尽快脱离换热管壁,减少气泡造成的热阻,从而提高了换热管的换热系数。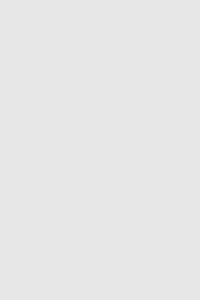
版权声明:本文作者陈松等,由HETA小编编辑整理,内容有删减修改,文章观点不代表本公众号立场,侵权联系删除,转载请注明来源。
|