针对纤维/基体间的界面脱黏决定能量吸收这一核心问题,采用一系列标准黏结力参数调整复合板界面黏合力,并通过层间黏性行为和损伤参数模拟界面分层过程.利用ABAQUS有限元软件中的Explicit分析模块建立陶瓷/纤维复合防弹板的高速冲击损伤分析模型,通过分析弹丸初始速度与剩余速度,研究复合防弹板的各组分结构参数、纤维指标、铺层设计对靶板及层合板抗侵彻行为的作用规律,并结合冯·米塞斯(Von-Mises)应力云图和基体损伤云图,探讨复合防弹板的受力与损伤形式.最后,利用弹道冲击实验成功验证了模型的准确性.实验结果表明:由13mm厚SiC陶瓷、5mm厚碳纤维复合材料板和17mm厚超高分子量聚乙烯纤维(UHMWPE)复合材料背板组成的复合防弹板可有效防御弹丸侵彻,对弹丸动能吸收和弹速衰减作用明显. 陶瓷复合防弹装甲由硬质陶瓷与金属背板或纤维复合材料背板叠层,用于防御穿甲弹等高速弹丸侵彻的轻质防护装甲,目前陶瓷复合防弹装甲一直是军用防护领域的研究热点.陶瓷防弹装甲体系常用氧化铝(Al2O3)、碳化硼(B4C)、碳化硅(SiC)和氮化硅(Si3N4)为硬质陶瓷材料以抵抗弹丸冲击,以高性能纤维尤其是碳纤维、超高分子量聚乙烯纤维(UHMWPE)纤维等组合设计用以配合提高陶瓷层的抗变形能力,尤其碳纤维作为一种高比强度、高比模量的优质纤维,对于保证陶瓷防弹板防护稳定性具有重要作用.陶瓷复合防弹装甲在抵抗弹丸侵彻瞬时的能量吸收过程和吸收机制较为复杂,对于不同实验条件的弹丸侵彻过程仿真,一直是防弹装甲的研究重点.Schwab等研究了冲击速度对复合材料层合板残余速度、层合板内部的能量吸收、损伤模式和损伤尺寸的影响.Liu等通过ABAQUS有限元分析软件中的Explicit分析模块系统研究了钛合金/UHMWPE背层复合陶瓷装甲对弹丸的作用机理.Tepeduzu与Karakuzu则使用仿真分析软件ANSYS探讨了不同陶瓷厚度及不同背板材料的陶瓷复合装甲的冲击特性.有关陶瓷复合防弹装甲板的研究主要集中在失效破坏机制和结构组合设计方面,有关复合材料层间黏合性能、纤维类型参数以及装甲组合结构对靶板抗侵彻性能的影响研究较少,同时增强纤维与树脂基体间界面特性以及界面失效行为也是影响弹丸能量吸收效果的重要因素,纤维与树脂基体界面脱黏行为也将显著影响复合材料对弹丸的能量吸收.针对这一问题,本文采用系列化标准黏结力参数调整界面黏合力,使用54式12.7mm穿甲弹作为冲击体,在弹丸高速冲击瞬态破坏状态下,通过防弹复合材料板的层间黏结行为变化和损伤参数,模拟防弹板的界面分层能量吸收过程,并通过弹道冲击实验验证了模型的准确可靠性.此项工作可为陶瓷−纤维复合防弹装甲板设计和优化提供参考.
模拟仿真实验及方法 本文建立的防弹复合材料板材模型,包括陶瓷(SiC)硬质防弹层、碳纤维增强环氧复合材料(CFRP)刚性层和UHMWPE复合材料韧性背板层三部分构成,靶板的长宽均为600mm,厚度为35mm,其中陶瓷层厚度为10mm,CFRP层厚度为5mm,UHMWPE复合层厚度为25mm,其装配后截面如图1(a)所示.本文采用渐进式网格划分,网格密度由弹丸的弹着点为中心逐渐向外减少,同时采用1.5mm×1.5mm×1mm的细化网格处理侵彻直接接触区域的弹丸与靶板的直接接触部分,从而有效保证模型计算效率和计算精度. 本文的复合材料防弹板的仿真模型如图1(b)所示,弹丸与靶板的直接接触放大位置如图1(c)所示.靶板陶瓷防弹层使用三维实体单元建模方式,纤维增强树脂复合材料层采用连续壳单元建模方式,每层厚1mm,使用ABAQUS有限元分析软件内置的Hashin失效准则,靶板的复合材料层间通过接触属性定义层间黏性行为和损伤参数以模拟层间分层.实际弹体为12.7mm口径穿甲弹,采用四结点线性四面体单元(C3D4)进行仿真模拟,弹丸初始速度为820m·s−1,以柔性/剪切联合损伤模式定义模型中的材料属性,从而实现防弹靶板与弹丸接触瞬时的磨蚀作用仿真.弹丸与防弹板之间采用通用接触,对板外侧各面采取完全固定,弹头垂直于板中心冲击. 1.2 陶瓷Johnson-Holmquist材料模型 对于防弹陶瓷材料在较大应变变形、较高应变比率以及高压强瞬时高速冲击状态下的响应变化仿真研究,诸多学者进行了一系列本构关系模型的建立,由于陶瓷属于抗压强度高、抗拉强度低的脆性材料,并且当陶瓷出现微裂纹损伤破坏时,在压缩载荷的作用下呈现出渐进损伤状态,而这种大压强、高应变率条件下的脆性材料失效建模普遍采用损伤演化的Johnson−Holmquist(JH−2)材料模型,其中JH−2模型的强度模型为: 其中,归一化等效应力采用.公式表示,σ代表单位面积上材料所受的内力,Pa,其方向与应变方向平行;表示在Hugoniot弹性极限(HEL)时的等效应力,Pa;表示未损伤材料的归一化有效应力,Pa;表示完全损伤材料的归一化有效应力,Pa;D(0<D<1)表示基于每个计算循环里的塑性应变增量的累积破坏断裂准则.
 其中,材料常数采用A、B、C、M和N;P*表示通过Hugoniot弹性极限归一化压力,量纲为一, ,P表示材料当前所受压力,Pa;PHEL表示材料在Hugoniot弹性极限时所受的压力,Pa;T*表示归一化的最大拉伸断裂强度,量纲为一, ,T表示材料的抗拉强度,N·mm−2;THEL表示在Hugoniot弹性极限时材料的抗拉强度,N·mm−2;当D接近于1时,接近于0.归一化等效应变率采用 表示,其中 表示实际应变率,参考应变率 取值为1.0s−1.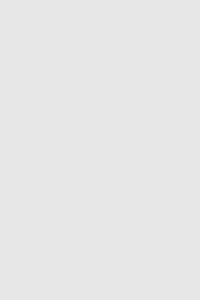 其中,p代表塑性,f代表断裂.等效塑性应变增量在一个循环的集成用表示,量纲为一;恒压断裂塑性应变采用表示,量纲为一.当D=1时,该元素将在模拟体系中被忽略.的表达式为: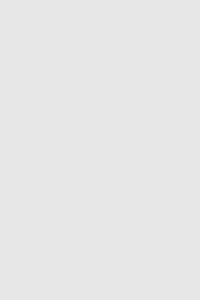 其中,损伤演化的材料常数用D1和D2表示.本次模拟使用的碳化硅硬质陶瓷材料的基本参数如表1所示.表中,表示最大断裂应力;HEL表示Hugonoit弹性极限;K1是体积模量,K2和K3是为了保证精度而引入的高次系数.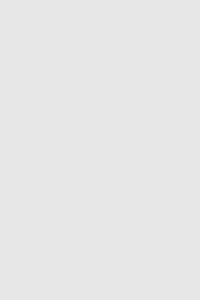 本论文采用浸渍树脂基体的纤维叠层结构的复合材料,纤维的轴向拉伸破坏在抵抗弹丸侵彻破坏方面起到主要关键作用,而树脂基体主要通过界面分层脱黏失效来实现对弹丸能量的吸收.本文基于Hashin3D失效准则建立仿真模型,遵循以下四个失效准则分析叠层复合材料的失效破坏: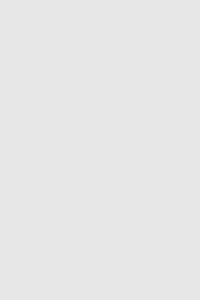
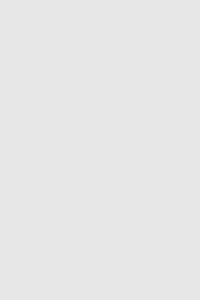
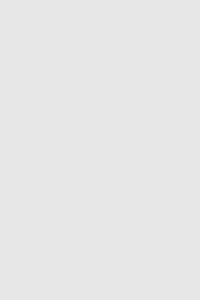
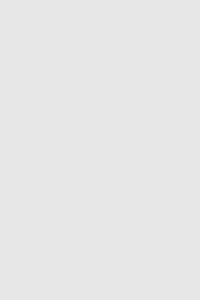 其中,T代表拉伸,C代表压缩,f代表破坏.FfT为纤维拉伸破坏系数,量纲为一;FfC为纤维压缩破坏系数,量纲为一;FmT为基体拉伸破坏系数,量纲为一;FmC为基体压缩破坏系数,量纲为一;XT为轴向拉伸强度、XC为轴向压缩强度、YT为横向拉伸强度、YC为横向压缩强度、ST为横向剪切强度、SC为轴向剪切强度,MPa;σ11、σ22、σ33、σ12、σ13分别为复合材料横向、轴向、法向、横向轴向交叉向、横向法向交叉向的应力分量;以(0≤≤1)表示剪切力的贡献因子.不同纤维增强环氧树脂基体复合材料基本性能参数,见表2和表3.表2中的E、υ和G分别代表复合材料的杨氏模量、泊松比和剪切模量;下角标11代表横向,22代表轴向,33代表法向,12代表横向轴向交叉向,13代表横向法向交叉向,23代表轴向法向交叉向.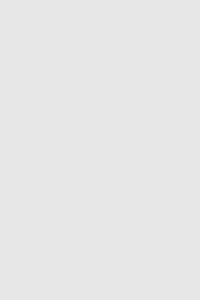
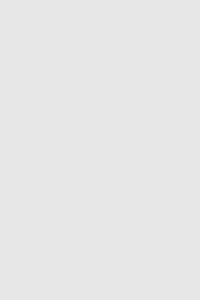
靶板结构对复合防弹板抗侵彻性能影响规律的仿真 陶瓷复合防弹板的陶瓷层主要通过破碎、磨蚀弹头和陶瓷破坏与变形吸能.图2为在纤维层厚度、铺设方式等条件相同的情况下,8、9、10、11、12和13mm六种不同厚度陶瓷复合防弹板受冲击时弹速随时间的变化.可以看出,弹丸剩余弹速随陶瓷层厚度增加而降低,其中8mm厚陶瓷板约在18时被穿透,而9mm和11mm厚陶瓷板被穿透时间分别为45和57.弹丸冲击陶瓷层为8mm的复合防弹板剩余速度为624.3m·s−1,相比820m·s−1的初速度,速度降低了23.87%,而冲击陶瓷层厚为9、10、11和12mm的复合防弹板速度分别降低了39.5%、42.02%、67.24%和69.59%.陶瓷层在对抗弹丸的侵彻方面起到关键作用,这种作用通过高硬度陶瓷材料对弹丸的磨蚀作用实现,当弹丸与陶瓷层的接触时间延长,所带来的弹丸端部的钝化磨蚀和弹丸材料的破坏作用越多,在弹丸侵彻过程所消耗的能量也越多,因此陶瓷复合靶板整体的防护特性也越明显,当陶瓷层厚为13mm时已可抵挡弹丸侵彻.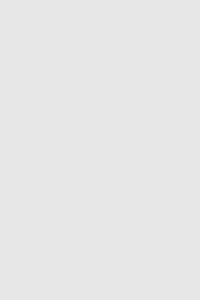 增强纤维与树脂基体之间的界面脱黏是复合材料防弹板消耗弹丸侵彻能量的另一种关键形式.本文的界面分层作用通过接触属性定义复合防弹板层间黏性行为和损伤参数进行模拟,所用标准黏结力参数如表4所示,其中,ModeI代表子弹冲击方向,ModeII和ModeIII代表垂直于子弹冲击方向的平面内以弹着点为中心的垂直两向.本节讨论黏结力强弱对靶板抗侵彻性能的影响,将表4中的黏合力分别上调和下调了20%以模拟强弱不同的层间作用力.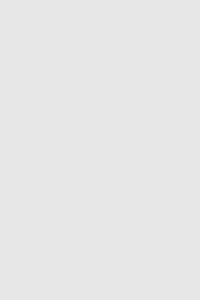 图3为不同层间黏合力下第10层纤维板基体拉伸损伤云图,可知随着黏合力增加,基体损伤面积减小,分层面积也随之减小.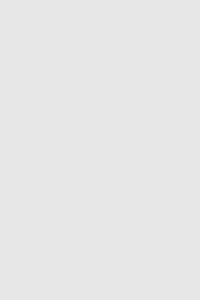 图4为不同层间作用力下弹速随时间变化曲线,由图4可知,黏合力上调20%的靶板与标准靶板、黏合力下调20%的靶板相比,弹丸残余速度分别降低了3.46%和7.19%.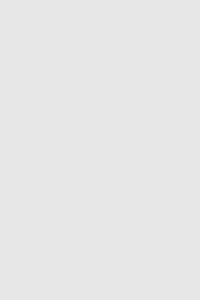 这是因为黏合力低,基体与纤维结合能力下降,纤维在弹击作用下易产生滑移影响抗侵彻性能,而黏合力增加能使纤维分层破坏过程中吸收能量更多,在逐层破坏的同时将弹丸的层间破坏通过界面脱黏吸能,使其弹速下降更明显.但也有研究表明,过强黏合力会阻碍纤维受外力作用时的拉伸变形导致吸能减少,因此,适当降低界面黏结度有利于提高冲击韧性.当黏合力弱时,裂纹端部出现脱黏,当黏合力强时,纤维冲断和纤维端部应力松弛吸收能量,适中的黏合力能使靶板吸收更多能量.本节对T700SC、M40JB和M60JB三种碳纤维抗冲击性能进行比较,不同种类碳纤维性能如表5所示.T700SC纤维拉伸强度和断裂伸长率最高,M60JB纤维拉伸模量最高,M40JB纤维各项数据适中.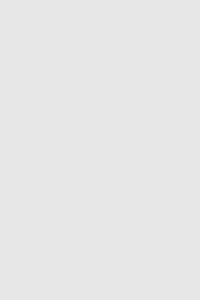 图5为不同碳纤维种类下弹丸动能随时间变化曲线,M40JB吸能最多,M60JB吸能最少,T700SC吸能介于二者之间,使用M40JB的装甲板的吸能约比使用M60JB和T700SC分别高7.09%和4.56%.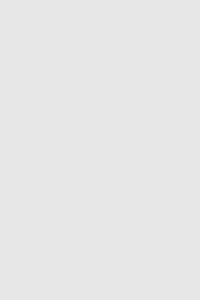 由模拟结果可知,拉伸模量和拉伸强度都会影响碳纤维的抗侵彻性能,高强高模、断裂伸长率高的碳纤维防弹性能更好.这是因为弹着点附近的纤维拉长进而断裂的过程可吸收弹丸部分能量,M40JB不仅拉伸强度较高,模量也较高,而模量较高的纤维背板不仅对陶瓷面板提供较强支撑,还可以快速传递冲击波,提高防弹效果;背板材料力学性能越好,陶瓷与弹丸相互作用时间越长,力学性能好的纤维还可以通过自身大变形来消耗弹丸部分动能以降低弹丸的残余速度.图6比较了纤维铺层角度按照0°和90°交替铺层([0°/90°/0°/90°])和纤维铺层角度按照45°和−45°交替铺层([45°/−45°/45°/−45°])两种纤维铺层方式对防弹板抗侵彻性能的影响.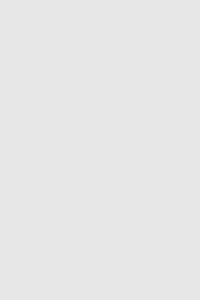
图7为[0°/90°/0°/90°]和[45°/−45°/45°/−45°]两种不同纤维铺层角度下弹丸动能随时间的变化曲线,在两种情况下弹丸动能衰减量分别为12870.84J和12044.58J,相比90°铺层,45°铺层对弹丸的耗能约高出6.86%,即45°铺层时靶板的抗侵彻性能更好. 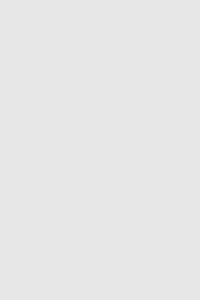
复合材料的拉伸失效是指复合材料弹着点附近的纤维被拉长直至断裂的失效过程,此过程可吸收弹丸大量能量,是复合材料防弹板的主要吸能过程之一.在这一过程中背板受力面积越大则参与拉伸失效的纤维越多,对弹丸的耗能也更多. 图8为两种铺层防弹板第22、23层纤维层的冯·米塞斯(Von-Mises)应力云图,从图中可以看出,45°铺层中防弹板受力面积更大,更多的纤维处于拉伸模式从而参与拉伸失效的纤维更多,靶板的抗侵彻性能也更佳. 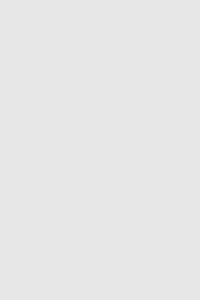 基于复合材料靶板的冲击波传播机制,对于叠层复合材料结构的弹丸侵彻过程,在其厚度方向存在不同类型的破坏形式,Johnson和Holmquist研究发现,复合材料靶板的侵彻破坏在弹丸入射方向上分两个阶段:第一为剪切冲塞阶段,该阶段纤维以横向的剪切破坏为主;第二为背凸变形阶段,该阶段纤维主要发生拉伸变形破坏.根据不同阶段的破坏形式特点,在迎弹面设置抗压强度和抗剪切强度高的无机陶瓷材料,而在背弹面设置抗拉强度高的有机纤维复合材料,可有效提高整个复合材料靶板的抗弹丸侵彻特性,基于此机制,本文在陶瓷层与UHMWPE层之间加入CFRP以增强背板抗侵彻能力,本节探讨了CFRP厚度对防弹板吸能效果的影响.CFRP层内能随时间的变化曲线.可以发现,随着CFRP厚度增加,能量吸收量逐步上升.5mm厚CFRP层和7mm厚CFRP层内能分别较3mm厚CFRP层增加了68.8%和109.2%,7mm厚CFRP层与5mm厚CFRP层相比吸能增加速率减小.CFRP层厚度与弹丸残余速度的变化关系如图9(b)所示,也可知CFRP层由5mm增至7mm时残余速度下降趋势变缓,因此当CFRP板的层数达到一定值后通过增加CFRP层的厚度对防弹板抗侵彻性能提升有限.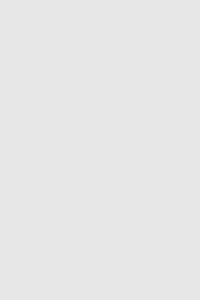 2.6 UHMWPE层合板厚度对复合防弹板抗侵彻性能的影响 UHMWPE复合材料板在受到弹丸冲击时的失效机理可以简单解释为:在冲击初始阶段应变率非常高,材料破坏是由于纤维断裂.第二阶段,弹丸动能降低,穿靶速度减慢,纤维复合板开始分层,导致背凸出现.最后,弹丸穿透面板或停止.为减轻防弹板质量,以13mm厚SiC陶瓷层为防弹面板、CFRP层厚度为5mm,研究UHMWPE复合材料背板厚度对弹丸残余速度的影响(图10),得出抗侵彻防弹板最低UHMWPE复合背板厚度.当UHMWPE复合材料厚度为17mm时弹丸残余速度降为0,可抵御弹丸侵彻.20mm厚的UHMWPE层合板弹丸冲击时残余速度减为0的时间约为210μs,而17mm厚的UHMWPE层合板弹丸冲击时残余速度减为0的时间约为250μs,用时时长增加约40,证明背板厚度增加可缩短防弹板受侵彻时间.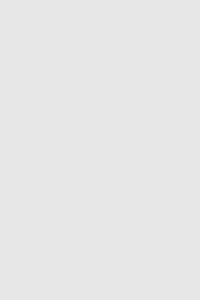
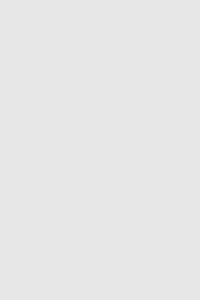
模拟仿真优化参数实验验证 根据本文模拟仿真研究的优化参数规律,以直径为12.7mm的穿甲燃烧弹作为侵彻条件,分别对两种组合结构的复合防弹板(13mm厚陶瓷层/5mm厚CFRP板/16mm厚UHMWPE层合背板和13mm厚陶瓷层/5mm厚CFRP板/17mm厚UHMWPE层合背板)进行实际打靶测试,以验证仿真结果的准确性.其中复合防弹板的UHMWPE纤维背板采用特力夫80UHMWPE纤维增强热塑性树脂20MPa模压成型制备,CFRP板采用T700碳纤维增强热固性树脂12MPa模压成型制备,陶瓷片与CFRP板以及UHMWPE纤维背板采用胶黏剂压力成型制备,成型压力为5MPa.上述两种结构的防弹板受冲击后的背板破坏形态如图11(a)和11(b)所示.从图中可以看出,装配16mm厚UHMWPE层合板的靶板被击穿,而装配17mm厚UHMWPE层合板的复合防弹板出现冲塞现象未被击穿,图11(c)为装配有17mm厚UHMWPE层合板的复合防弹板受冲击后背面仿真形貌图,从图中可以看出,模拟冲塞的形态与实验结果比较吻合.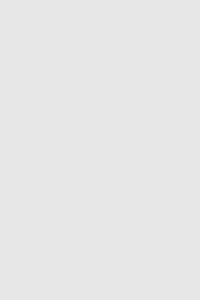
表6为两组17mm厚UHMWPE层合背板与仿真模拟云图背板形变量的对比数据,从表中可以看出,实际层合板背板的变形高度与仿真云图变形高度基本一致,因此模拟对实验结果的预测准确性良好,可为工程实际提供参考. 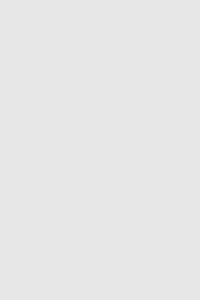
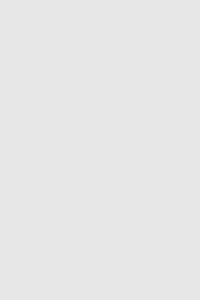
结论 本文探讨了复合防弹板不同陶瓷层厚度、不同背板材料的抗侵彻能力,使用显式有限元软件ABAQUS/Explicit对弹丸侵彻陶瓷/碳纤维/UHMWPE纤维复合防弹板的过程进行仿真模拟,得到如下结论:(1)陶瓷层碎裂及其对弹丸的磨蚀作用为复合防弹板的主要能量吸收方式,其中陶瓷层厚度为复合防弹板抗侵彻特性的主要影响参数,由仿真结果可知:13mm厚SiC陶瓷面板可有效抵挡12.7mm穿甲弹的弹丸侵彻.(2)适度的层间黏合力是复合防弹板瞬态吸能效果的有效保障因素,在一定水平下,层间黏合力的增加可降低基体损伤面积,有效提高纤维分层吸能效果,而过强的层间黏合力又不利于复合防弹板在弹丸侵彻瞬间的纤维拉伸变形.角度铺层纤维背板比正交铺层纤维背板具有更高的纤维拉伸失效参与程度,可使复合防弹板获得较佳的抗侵彻能量吸收效果.(3)复合防弹板抗侵彻过程的吸能增速随着CFRP板厚度的增加逐渐降低,当CFRP板厚度达到一定程度后,碳纤维复合材料层的厚度对复合防弹板整体抗侵彻性能的提升效果有限.仿真模拟分析可知,采用13mm厚SiC陶瓷、5mm厚CFRP复合材料、17mm厚UHMWPE复合材料组成的复合防弹板可有效防御弹丸侵彻,对弹丸动能吸收和弹速衰减作用明显.作者:秦溶蔓,朱波苣,乔琨,王东哲,孙娜,袁晓敏(山东大学材料科学与工程学院)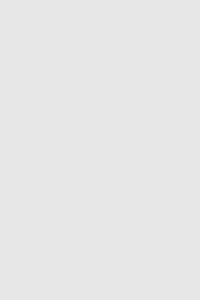 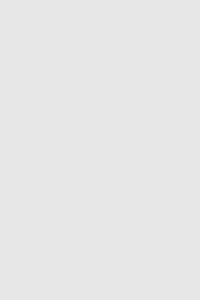
|