1、概述 高炉矿渣是冶炼生铁时从高炉中排出的一种废渣。在冶炼生铁时,加入高炉的原料,除了铁矿石和燃料(焦炭)外,还有助溶剂。当炉温达到1400-1600℃时,助溶剂与铁矿石发生高温反应生成生铁和矿渣。高炉矿渣就是由脉石、灰分、助溶剂和其他不能进入生铁中的杂质所组成的易融混合物。从化学成分看,高炉矿渣属于硅酸盐质材料。每生产1t生铁时高炉渣的排放量,随着矿石品质和冶炼方法不同而变化。例如采用贫铁矿炼铁时,每吨生铁产出1.0-1.2t高炉矿渣;用富铁矿炼铁时,每吨生铁只产出0.25t高炉矿渣。 
1.1 高炉矿渣的分类 由于炼铁原料品种和成分的变化以及操作条件等工艺因素的影响,高炉矿渣的组成和性质也不同。高炉矿渣的分类主要有两种方法。 (1)按照冶炼生铁的品种分类 ①铸造生铁矿渣;②炼钢生铁矿渣;③特种生铁矿渣。 (2)按照矿渣的碱度区分 高炉矿渣的化学成分中的碱性氧化物之和与酸性氧化物之和的比值称为高炉矿渣的碱度或碱性率。 1.2高炉矿渣的组成 高炉矿渣中主要的化学成分是二氧化硅、三氧化二铝、氧化钙、氧化镁、氧化锰、氧化铁和硫等。此外,有些矿渣还含有微量的氧化钛、氧化钒、氧化钠、氧化钡、五氧化二磷、三氧化二铬等。在高炉矿渣中,几种化学成分见下表。 1.3 高炉矿渣的综合利用情况 由于高炉矿渣属于硅酸盐质材料,又是在1400-1600℃高温下形成的熔融体,因而便于加工成多种建筑材料:水淬成粒状矿渣(水渣)是生产水泥、瓦砖和砌块的好原料;经急冷加工成膨胀矿珠或膨胀矿渣,可做轻混凝土骨料;吹制成矿渣棉可制造各种隔热、保温材料;浇筑成型可做耐磨的热铸矿渣;轧制成型可做微晶玻璃;慢冷成块的重矿渣可以代替普通石材用于建筑工程中。因此,高炉矿渣的综合利用非常重要。我国高炉矿渣的利用率为85%以上。 2、高炉矿渣的加工和处理 在利用高炉矿渣之前,需要进行加工处理。其用途不同,加工处理的方法也不同,我国通常是把高炉矿渣加工成水渣、膨胀矿渣和膨胀矿渣珠等形式加以利用。 2.1 高炉矿渣水淬处理工艺 国内外生产上应用的高炉渣基本上是水淬法和干渣法。由于干渣处理环境污染较为严重,且资源利用率第,现在已经很少使用,一般只在事故处理时。高炉矿渣水淬处理工艺就是将热熔状态的高炉矿渣置于水中急速冷却的处理方法。用水淬处理后的高炉矿渣可变为疏松的粒状矿渣。 2.1.1 水淬的主要方法 在高炉生产中,水淬法是最简洁、高效的渣处理方法,目前的水淬法包括拉萨法(RASA)、图拉法(TYNA)、明特法(MTC)、底滤法(OCP)、因巴法(INBA)。 我国大多数高炉采用的是深水底滤法(OCP),西方国家大部分采用因巴法(INBA)。 
2.1.2 各种水渣处理方法的工艺流程及特点 (1)拉萨法 拉萨法的处理工艺是由英国的RASA公司和日本的钢管公司一起研发的,在1967年首次应用于日本福山钢铁的1号高炉(2000m3)。 在国内第一家应用该技术的企业是上海宝钢。其工艺流程为高炉渣由渣沟倒入冲制箱进行水淬,之后进入粗分槽; 渣浆泵将渣送进脱水槽进行脱水处理,将渣粒送至沉淀池,经沉淀后的渣粒再次送入脱水槽;沉降池中的水经过冷却处理后再返回去进行冲渣处理,以此形成循环利用。 
(2)图拉法 图拉法首次应用在俄罗斯图拉厂的2000m3的高炉上。国内首次应用的厂家是首钢。其工艺流程为采用圆筒形的转鼓对渣进行脱水处理。 首先转鼓带动四周的筛板旋转把渣水混合物带上来,在外壁的滤网处进行脱水。然后将落在转鼓内接料罐中的渣通过胶带机传送到渣料场。 2)采用粒化轮机械粒化,轮转速125—1250rpm。4)吨渣耗水0.7t/t、压缩空气消耗10m3/t。
(3)明特法 明特法最早应用于首钢3#高炉(2536m3)上,该工艺是由北京明特克冶金炉技术有限公司和首钢联合研制的。 明特法采用螺杆旋转的方式将储渣池底部的渣向上传送,渣的脱水过程通过重力和螺杆片对渣的旋转力和挤压力的共同作用下完成。 脱水后的渣被搅拌器的凹槽输送到皮带传送系统上,再到残渣场。渣池中的冲渣水经过过滤器过滤后在排渣泵的作用下回送至渣水系统,实现整个排渣系统中水的闭路循环。 4)冷凝塔采用耐热钢制造,塔内有不锈钢丝网和喷头,塔顶设防爆阀。
(4)底滤法 底滤法的工艺流程为:当炉渣进入炉渣沟并落到底部时,高压水流立即将其击碎,矿渣经水淬后被冲到矿渣池,抓斗将矿渣吊起进行脱水,矿渣池中的水经过滤池过滤后经水泵送到冷却塔,形成循环利用。该冲渣工艺中的水压:0.3~0.4MPa;渣水比为 1:10~1:15,水渣含水率为10%~15%。 
(5)因巴法 因巴法是20世纪80年代由比利时西德玛公司与卢森堡公司联合研发的一项熔渣处理工艺。我国于1991年6月首次应用于宝钢2号高炉上。 因巴法的工艺流程为:熔渣从渣沟流向重制箱,被里面的高压水水淬后进入渣沟,经分配器、缓冲槽进入滚筒过滤器进行过滤,脱水后的渣经皮带机运出,然后由外部皮带机运送到储渣槽内。 因巴法有冷INBA、热INBA和环保型INBA之分。3种因巴法的炉渣粒化、脱水的方法均相同,都是使用水淬粒化,采用转鼓脱水器脱水,不同之处主要在水系统。 冷INBA水系统中设有冷却塔,粒化水冷却之后再进行循环;热INBA中没有冷却塔,粒化水直接进行循环; 环保型INBA水系统中分粒化水和冷凝水两个系统,冷凝水系统主要用来吸收二氧化硫、蒸汽、硫化氢。与冷、热INBA比较,环保型INBA最大的优点是硫的排放量很低,它把大部分硫转移到循环水系统中。 2)分为冷因巴(需要循环水冷却)、热因巴(不需要循环水冷却)、环保型因巴(配循环水冷却、冷凝)。
热因巴简单,不需要冷却水塔

环保型因巴法

2.2 干渣法高炉渣处理工艺 2.2.1 滚筒法 滚筒法分为双滚筒法和单滚筒法。双滚筒法由日本NKK公司研究开发[7],它的主要技术原理是将1400℃的熔渣倒进两个反向转鼓,经过转鼓的旋转作用将熔渣粒化并同时进行热交换,经冷却后的渣温度约900℃,生成的蒸汽经回收后用于蒸汽发电。NKK在福山4号高炉上进行了工业试验,渣玻璃化率达95%,热回收率达40%。 单滚筒法是由日本住友金属公司与石川岛播磨重工于20世纪80年代联合开发的。其工艺原理为:熔渣从一定的高度落下撞击到旋转的滚筒表面而被粒化,之后进入固体介质的流化床进行热交换。此工艺热量回收效率较低,处理能力小,因此至今未能实现工业化应用。 1)高炉熔渣用粒化器冲制成水渣,渣浆经渣头流入滚筒。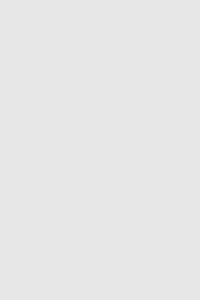
2.2.2风淬法 风淬法的技术原理是熔融态的高炉渣在高速的气流冲击下被喷射粒化,粒化渣在余热回收设备里进行换热冷却,收集的显热用于蒸汽发电。 此方法在日本、德国、瑞典、韩国等国家均有研究,其中日本新日铁、川崎制铁、住友金属等公司联合进行了高炉渣风淬粒化试验[8-10]。 国内也有一些风淬法相关研究。王子兵[11]等人以高炉熔渣为热源,以空气为风淬介质,以空气和水作为换热介质,利用回转式冷渣机,进行高温渣粒余热回收试验。该工艺将粒化与余热回收分开,大大减少动力消耗。 研究调质剂比例、风淬压力和喷嘴结构对系统热回收效率的影响。刘振超[12]通过建立数学模型研究了高炉渣的气淬成珠原理,利用热力学模型和实验探究了颗粒在空气中的换热过程和成珠效果。 研究表明,喷嘴直径、气体的流量和压力、高炉渣表面张力和粘度等都会影响成珠过程,据此确定了最佳工艺条件。李书磊[13]等人根据高炉熔渣具有巨大显热的特性,设计了一种通过风淬粒化、余热锅炉回收余热的新工艺。该工艺不仅余热回收率高,而且具有结构简单、不消耗新水、有害气体零排放等多种优势。 3)熔渣温度从1500到1000,再在热交换器内冷却到300℃。4)风淬得到的粒化渣的颗粒直径分布宽,不利于后续处理。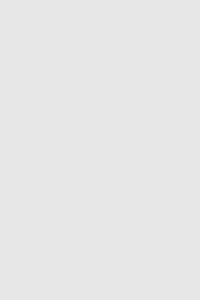
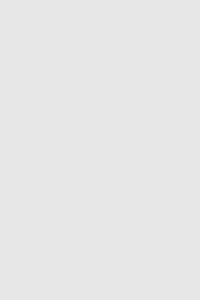
2.2.3. 离心法 (1)转杯粒化法 转杯粒化工艺是由英国的Pickering[14-15]等人在上个世纪80年代提出的。主要工艺流程为:高温熔渣进入高速旋转的转杯,在离心力和表面张力的共同作用下熔渣沿半径被甩出并形成颗粒,同时转杯周围的环形空气射流使渣膜产生不稳定的波动,进一步促进熔渣的破碎粒化。 粒化渣撞击粒化室内壁,与水管中的冷却水进行热交换,然后反弹进流化床再次进行热交换。该方法粒化渣玻璃相大于95%,性能优于水淬渣,但设备复杂,控制起来较为困难。 Mizuoehi[16]等人研究了转杯形状、转速、熔渣粘度、气流速度等对高炉渣粒化的影响。结果表明,具有浅薄边缘和平缓内壁的转杯更有利于粒化;转杯的转速越大,渣粒的平均尺寸越小,当转速为3000r/min时,渣粒尺寸<1mm,形状多为球形;粘度增大,粒化效果变坏,同时增加气流速度将有利于高炉渣的粒化。
(2)转盘粒化法 转盘粒化原理与转杯粒化相似,依靠转盘旋转的离心力将熔渣甩出粒化。澳大利亚联邦科学与工业研究组织(CSIRO)研究了转盘干法粒化的原理[17],优化了工艺流程。 2015年,北京中冶设备研究设计总院有限公司与CSIRO合作进行转盘粒化的工业化试验,目前已经建成了处理量30t/h的粒化设备,运行效果良好。 该技术采用两步法工艺,第一步是采用特殊设计的气流旋转式粒化装置,对熔渣进行离心粒化与余热一次回收,即借助转盘的离心力对高炉渣进行干法粒化处理并利用一次冷却风进行快速冷却和一次余热回收; 第二步是已凝结的高炉渣粒冷却和二次余热回收,进一步提高余热回收率,既采用特殊设计的具有缓冲功能的回转式逆流余热回收装置进行二次余热回收。 (3)转筒粒化法 2010年日本京东大学的Kashiwaya[18]等人开发了转筒粒化工艺,其工艺流程为:将高温熔渣从旋转的转筒中心注入筒身,筒身侧面设有喷嘴装置,在离心力作用下熔渣被挤入喷嘴,并以一定的速度喷出。 转筒分为双喷嘴和多喷嘴两种形式。此工艺生产的产品多为玻璃相球体,具有较高的球形度。 3)滚筒内通入有机高沸点(257℃)流体(二甲醚)迅速冷却。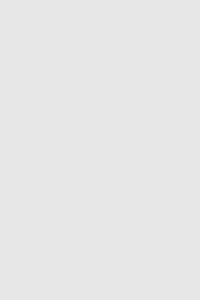
3、高炉渣余热回收利用的难点 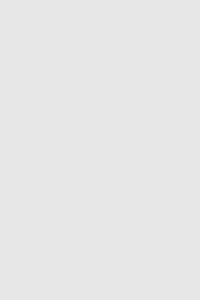 1)回收的高炉渣必须能做水泥原料,满足每年3亿吨高炉渣的市场需求,这也就是为什么90%的高炉都用水冲渣。2)高温熔渣的出渣是间隙性的,余热回收希望是连续的。3)通过循环水回收余热,因为蒸汽收集难,而60%的余热在蒸汽中,还有循环水的蒸发浓缩,导致循环水含盐量极高,结垢性腐蚀性都强,水水换热器造价高、维修量大。4、 高炉渣余热回收利用现有技术 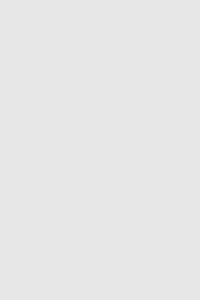
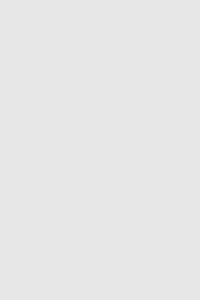 1)本产品主要针对冶金行业高炉冲渣水、化工厂半水煤气洗涤水、蒸氨废水、造纸厂黑液等各类具有强烈腐蚀性以及结晶、结垢现象的各类工业废水及工艺循环水的热能采集;2)采用真空相变技术,热能的提取与释放在两器内分别进行,避免了废水侧换热壁面的存在,溶解于水中的大量无机盐类等易结晶物质无处附着,从而彻底杜绝了间壁式换热器在换热过程中换热壁面结晶挂垢问题,同时也便于与废水接触的蒸发器部分进行防腐处理,且不影响传热;3)蒸发器等与废水接触的部分均采用以改性环氧树脂为基材的MH-700重防腐内壁专用涂料做为底衬,高屏蔽性的纳米陶瓷做表面涂层,在钢厂高炉冲渣水工况下使用寿命不低于10年,同时具备较强的抗侵蚀、抗结垢性能;4)对于各类工业废水,可连续稳定运行180天以上,传热温差可控制在5℃以内,且在承诺的使用期内传热系数无衰减。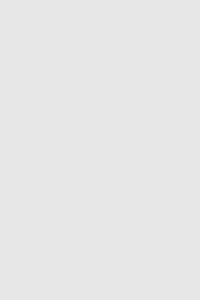
4.3甲烷循环反应热回收法 2)用高速喷出的甲烷和水蒸汽混合气体对高炉渣进行冷却和粒化,高炉渣被粒化成小颗粒。3)甲烷和水蒸汽混合物在熔渣高温热的作用下,生成氢气和一氧化碳,吸收高炉渣余热。4)生成气体进入反应器,在一定条件下,氢和一氧化碳气体反应,生成甲烷和水蒸汽,放出热量。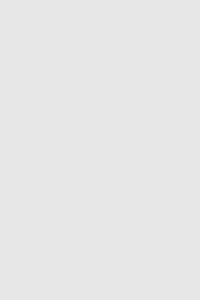 1)对水—水换热器存在问题,研究采用真空相变换热取热技术,改进完善。2)针对真空相变取热技术,研究改进提高,使余热回收温度降低到20℃。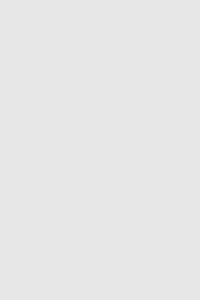
2)高炉渣雾淬粒化技术:
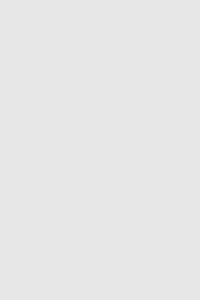
3) 高炉炼铁碳循环工艺 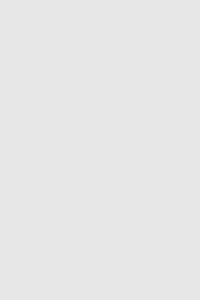 (2)二氧化碳加压用于高炉渣雾淬粒化,并加碳实现还原
|