摘要  异种金属焊接过程中两种不同液体之间不断变化的界面形式可以严重影响凝固微观结构的发展并决定接头的机械性能。为了研究电弧焊过程中的界面演变机制,采用了时间分辨 X 射线照相术。观察结果表明,在短暂的准稳态之前,不同液体界面处会形成短暂的指状突起。使用磁热流体动力学数值模拟对实验观察进行的分析证实,准稳态涉及短寿命固相的形成,这改变了过程中的规则混合。对原位实验观察的分析阐明了热场、动量场、电磁场和成分场之间的相互作用,这些相互作用决定了液体界面不稳定性和熔池形状的形成机制。基于分析,我们扩展了我们的研究,通过抵消热源为异种材料焊接提供实用的增强。引言 使用焊接可以被认为是金属材料先进制造和制造的基石。日益复杂的设计和服务需求需要将不同的金属合金连接在一起。然而,异种金属焊接面临着挑战,因为需要焊接在一起的两种金属合金的性能存在固有差异。物理性质直接影响熔化和随后的快速凝固特性。不同密度的熔融液体在混合时容易产生瑞利-泰勒型不稳定性,并且焊缝熔合区边缘的波状起伏加剧了这种不稳定性。表面张力梯度(马兰戈尼效应)是一种非常重要的传质现象,它允许熔融金属在熔焊过程中响应表面张力的变化而流动。在异种金属焊接中,热膨胀系数和熔点的差异会导致熔池界面表面张力的快速变化,从而影响焊池的稳定性。硫和其他表面活性元素也会对熔池内熔融金属的表面张力产生深远的影响。它们可以逆转表面张力梯度,从而影响熔融金属流动和最终焊池形状以及缺陷形成。此外,异种金属焊接过程中异种金属之间的快速反应(以及微观尺度的质量扩散)和金属间相(IM)的形成会显着影响焊接接头的性能和结构完整性。当两种金属连接在一起时,它们表现出更高的腐蚀敏感性,导致使用寿命缩短并增加结构维护要求。在通过熔焊进行的异种金属连接中,由于不均匀的溶质分布而导致宏观偏析的发生是很常见的。总体而言,焊接接头的性能(包括熔合区形状和缺陷)与不断发展的熔池内发生的传热和传质过程密切相关。了解与熔池内发生的界面形成、混合和凝固相关的潜在物理机制将有助于制定针对形成的缓解策略劣质异种焊缝。这在安全关键型应用中尤其重要,例如核电和航空航天,其中异种金属接头很常见。液态混合不均匀、孔隙形成和溶质偏析是熔焊接头缺陷和有害相形成的主要潜在原因。其中许多原因往往受到熔池行为的影响。除了不透明之外,相间界面的高度瞬态性质加上高温使得直接观察熔池或类似事件具有挑战性。传统的调查大多仅限于后处理分析。然而,有两种新技术可以用来改变这种范式。同步加速器光源产生的高能 X 射线已成为克服这些挑战的工具,并为金属中的传输现象提供新的见解。Yamada等人利用高能X射线成像技术(HEXITEC)描绘了激光微焊接过程中熔池的形态变化,强调了气泡和裂纹的出现。Aucott 等人使用 HEXITEC 研究凝固裂纹和电弧焊中流体流动的作用,可视化表面活性元素对流速和图案变化的影响。Zhao 等人利用 HEXITEC 探索基于金属熔融的增材制造 (AM) 中的实时物理现象,强调熔池中的小孔形成和尺寸变化 。Parab 等人设计了一种实验室规模的激光金属增材制造装置,与 HEXITEC 集成,以捕获激光粉末床融合 (LPBF) 过程中的蒸气抑制和粉末飞溅等现象。以非常高的速度(10 MHz)捕获的图像定量测量了蒸气压的振荡和粉末颗粒的旋转。Liu等人采用HEXITEC来检查Al-8%Si电弧焊熔池中的流体流动,呈现熔合区形状、流动模式和缺陷的动态演变。这些研究例证了利用尖端成像技术来增强对基于熔合的金属焊接和增材制造工艺的理解。而之前几乎所有 HEXITEC 工作都集中在一种(类似)金属合金焊接和增材制造。这也限制了当前异种金属焊接模型的开发和验证,例如阻碍了对制造过程中普遍存在的多尺度现象的识别。例如,通常用于模拟基于电弧的连接过程的建模框架总是忽略对系统的电磁贡献,因为直到最近才可用强大且可计算处理的多分量磁流体动力学框架。通过采用原位 X 射线照相和基于磁热流体动力学的数值模拟,揭示了对强熔焊条件下异种液体聚结过程中界面演变顺序和相关机制的新见解。还进行了后处理分析,以表征异种金属焊缝的微观结构和化学特征,从而能够全面了解与快速熔化和凝固过程中异种金属熔池评估相关的潜在机制。 实验设置 为了检查异种金属焊接过程中基本热性能的影响,选择铝合金(AA 6082)、两种钢(SS316L、S275)和铜(商业铜)进行原位X射线成像实验。实验材料的选择主要基于原位快速X射线成像(提供足够的衰减对比度)的可行性以及决定热流和质量流的不同物理特性的演示。选择用于实验的两种钢含有不同的硫含量。硫含量的差异允许进行比较研究,以评估表面张力(Marangoni)驱动的流动的影响,表面活性元素水平对表面张力驱动流动的影响显着。钢和铝合金表现出导热率和熔点差异,而铝合金和铜提供接近的导热率和良好的衰减对比度。焊接样品的尺寸为6毫米×10毫米×50毫米(厚度×高度×长度),所有邻接样品表面均经过精磨处理(图1)。实验期间,在两个样品的中间进行自熔化钨极电弧焊 (GTAW) 四到六秒。所有电弧电压保持在 11.5 V,同时改变电弧电流。根据样品的物理特性,采用 150 A 和 175 A 输入电流进行不同的焊接参数。焊接电极固定在样品 10 毫米(高度)和 50 毫米(长度)表面上方约 2 毫米处。研究中使用的材料的标称成分及其物理和热性能如表 1(和补充表 1)所示。

实验是在英国钻石光源的 I12 光束线上进行的。使用 53 keV 单色 X 射线束,成像系统由 1 mm 厚的 YAG:Ce 闪烁体组成,通过透镜耦合到 Vision Research Inc. MIRO 310 M 相机,通过光学放大系统 。两个样品并排放置在载物台上,入射 X 射线束穿过连接的样品,如图 1 所示。成像数据以高达 1 kHz 的帧速率采集,并具有全帧速率。超过 22.9 × 14.3 mm2 的场成像,成像系统的空间分辨率通过 17.9 μm × 17.9 μm 像素尺寸确定。所有图像处理、分析和量化均使用 ImageJ® 和 Matlab® 进行。 为了从 X 射线照片中提取原子比和重量比,应用朗伯-比尔定律 ,如下所示: 
其中 I 是透射强度,I0 是入射强度,μ/ρ 是总质量衰减系数,ρ 是密度,x 是透射路径长度,t 是样品总厚度,下标 A 和 S 表示铝和钢, 分别。求解 xs 方程(对于射线照片的每个像素)可以确定相对传输路径长度 [44],可以通过考虑每种材料的密度将其转换为原子比。单位面积(图 1b 区域 1-4)中提取的质量分数、体积分数和铁(以及铬和镍,其中 ρ 和 μ/ρ 近似相似)与铝原子比的定量随时间演变(图 1b 区域 1-4)的平均值在低硫钢和高硫钢与铝的焊接过程中,整个预计厚度的变化如图(补充图 2)所示。 使用放电加工 (EDM) 切割焊接样品以获得横截面信息。为了进行能量色散光谱 (EDS) 分析和微观结构表征,使用标准金相技术对样品进行研磨和抛光。使用 Helios G4 pFIB 和 Oxford Instruments Ultim Max 170 EDS 检测器(15 keV 和 6.4 nA)收集化学元素分布数据。对铝熔池侧溶质元素的含量进行了分析,为通过半定量 EDS 揭示逐步混合阶段和指状物形成提供支持信息(补充图 6)。由于样品横截面约为7.3 mm×5.6 mm,因此采用蒙太奇方法采集样品表面的多个帧,帧宽度为1 mm/215像素。使用 TESCAN MIRA3(11.5 keV)扫描电子显微镜(SEM)收集融合区的微观结构图像。 对于异种熔焊过程的数学建模,采用了基于最近发表的工作的新型磁热流体动力学框架,该框架能够捕获不同材料(保护气体和不同合金)之间的大流体动力学和电磁特性梯度)。在所介绍的异种电弧焊接的情况下,以数学上严格的方式捕获这些属性梯度至关重要。磁场的时间演变意味着可以正确捕获金属基材和保护气体中感应的洛伦兹力和焦耳热,这对加热和混合动力学有很大影响;其他方法(例如电势公式)忽略了这些重要方面,因此扰乱了关键物理。现在将简要介绍该框架。求解耦合偏微分方程组,该方程描述了动量守恒(方程(2))、能量守恒(方程(3))、质量守恒(方程(4)),以及最后的传播磁场强度(方程(5))。这些方程使用 OpenFoam 库之上的以细胞为中心的有限体积方法进行离散化。总之,动量守恒由方程 (2)描述。 其中 U 是速度,ρ 是质量密度,P 是流体压力,τ 是粘性应力张量。在方程式中。(2) 包括洛伦兹力 J × B。洛伦兹力是在存在磁场 B 的情况下施加在流体上的体力,其中 J 是电流密度。Φ 中还包括其他效应,例如浮力、表面张力和凝固引起的动量阻尼。其他细节在其他地方提供。能量传输方程用于求解域中的温度,并包含由聚变潜热和焦耳热产生的源项。能量传输方程由下式给出: 其中 Cp、k 和 σE 分别是多相混合物的比热、导热率和电导率。Sh 捕获由于基底熔化和凝固而产生的潜热效应。在等式(3)中J⋅J/σE 是因导电而产生热量的源项,称为焦耳热。该焦耳热项将电磁场的演化与能量传输方程耦合起来。利用平流扩散传输方程系统来描述混合物中存在的多种化学成分分数 αk 的演变: 混合有效扩散系数 Dk 是使用广义 Fickian 模型通过交叉扩散对的加权求和得出的。实现的更多细节可以在其他地方找到[45]。使用组分体积分数作为权重因子来计算异质混合物的热力学和传输性质,例如ρ = Σ k ρkαk 为混合物密度。请注意,总质量守恒是方程式 (4)的结果。在跨相边界 μM 和 σE 具有强烈反差的异质系统中,磁感应方程改为根据磁场强度 H 来表述。由此产生的场方程由下式给出: 该框架捕获了重要的物理现象,例如电阻加热、洛伦兹力项、表面张力、表面张力的温度依赖性(马兰戈尼效应)、由于熔融状态转变而产生的潜热贡献、由于金属基材热膨胀而产生的浮力效应,以及由于凝固而产生的动量汇效应。该建模框架允许考虑电磁和流体动力学变量中的梯度,这对于具有不同材料特性的磁感应场景来说是不可能的。所采用框架的完整描述以及数值实现可以在其他地方找到[39]。使用实验设置中的工艺参数(例如电流、电压、尖端距离)和近似边界条件,无需任何其他具体可调参数。这项工作中提出的模拟是使用 40 个 CPU 内核执行大约 250 小时。结果与讨论 通过 X 射线照相术获得铝合金 (AA6082) 与低硫钢 (SS316L,硫含量 ~ 300 ppm)、高硫钢 (S275、硫含量 ~ 500 ppm)和铜如图 2a-c(和补充影片 1)所示。低硫钢和高硫钢最初都发生膨胀并伴有轻微熔化(图2a、b)。由于铝的导热率比钢高,尽管其熔点相当高,但最初熔化的钢较多。在铝/高硫钢耦合中,钢与铝的混合比铝/低硫钢耦合早约 100 毫秒。电弧开始后 2 秒内,铝和钢熔池界面处建立准稳态,表现为铝和钢混合率降低。即使工艺参数不同,铝和钢之间的混合顺序也很明显。主要观察到熔池宽度增加随着(补充图 1)焊接电流的增加,可提供更高的热输入水平。  最初熔化和混合后,钢/铝熔体界面出现指状结构。这样,铝随着钢熔体膨胀而稀释,导致局部液相线温度升高,引发部分再凝固,并暂时稳定这种以手指形式出现的潜在固相形成。这种指状结构在低硫情况下大约需要 1.3 秒,而在高硫情况下大约需要 1.8 秒。一旦指状结构开始溶解,在铝/高硫钢对中观察到含铁熔体更明显的进入。由于硫的表面活性,在铝/高硫钢耦合中观察到熔池更宽,这强烈影响了马兰戈尼特性(图2b和补充图2、4)。虽然两种钢的碳含量存在相当大的差异,但不同的硫含量引起的相反的流动行为对熔池演变有较大的影响。熔池界面中心的对流在铝/高硫钢对中更为显着。随着焊接过程持续进行直至电弧熄灭,混合界面的不规则形貌清晰可见(图2)。与铝-钢接头相比,铝-铜接头在图2c中表现出明显不同的混合模式。在这种情况下,铝-铜接头的熔池尺寸和形状演变是不同的,这主要是由于两种基材的导热率较高。在前 0.5 秒内观察到基材的显着热膨胀,并在 1.1 秒左右开始熔化,这由可观察到的混合开始确定。马兰戈尼驱动的流动(图 3a)的强度在焊接的初始阶段达到峰值,这是由于在此期间金属界面上的温度梯度最高。这会导致熔池顶部熔融金属-气体界面的波动(图3b)。随着持续的热量输入,温度梯度减小,更多材料熔化,马兰戈尼对(总)动量的贡献减小,空气/液体界面变得更平坦、更均匀。模拟预测熔池界面上的温度梯度在 0.1 s 时为 4.2 ×107 K/m,在 0.5 s 时降至 3.4 ×107 K/m。因此,表面张力梯度的减弱是起弧后Fe-Al界面不相容并导致熔池界面由波状向波状转变的主要原因。 随着电弧的开始,铝钢界面的水平位置逐渐增加到初始位置(高度)之上。钢和铝的混合始于将钢输送到铝(图 4)。随着电弧进一步的热量输入(和电磁贡献),一些铝从界面的上部转移到钢侧。随着铝侧钢的膨胀大大停止,铝熔池开始水平膨胀,界面高度降低。此时,通过诱导流进行的质量传递比扩散更为显着,并且观察到铝熔体中钢液的运动主要是向下累积的(图4a)。模拟结果中显示的流动模式也与实验观察结果相似(图4b)。在熔池形成初期,铝钢熔池内的流动主要是向上、靠近界面处(顶部除外,此处较重的液体以动量侵入),在熔池外围则向下流动。在持续热输入约 1 s 的情况下,可以观察到铝侧钢的传输速率较高(从 18-49 mm/s 的代表值增加),并且熔化的铝较多,而总体流动趋势是向外的。当焊接时间经过约 2 秒时,界面上出现了明显的钢向铝的质量传输,这与实验和模拟一致显示。当大量的铝和钢混合时,密度较小的富铝熔体逐渐漂浮在富钢液体上方,并在熔池区域形成不规则的混合界面形貌(图2和图4)。X 射线成像和模拟表明,密度较大的金属更有可能迁移成较轻的金属。对于铝-钢和铝-铜焊接,铝侧是接收器。先前的研究还指出了焊接中重力驱动效应的重要性,而目前的工作可以为该现象提供可量化的证据。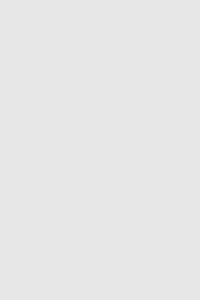 据观察,不同种合金中每种合金的熔化温度直接影响两种金属的最终混合状态。在铝-铜对中,中心区域金属的熔化发生时间明显晚于铝-钢(图2a-c),这似乎是由于较高的热导率所致。同时,气泡在两种金属之间的界面上形成时被夹带,然后被向下推(图2c)。在这两种情况下,电磁(电弧)力都会导致熔融金属向内流动,并导致气泡被包含在内。铝与钢的焊接不同的硫含量表明表面张力对不同液体的显着影响。随着硫含量较高,可以看到向铝侧的强劲向内流动,并且钢主要水平运输所需的时间较短。相反,在硫含量相对较低的情况下,由于内流趋势相对较小,钢侧的熔池直径相对较大。高硫钢中的正表面张力迫使更多的钢输送到铝熔池中,而低硫钢中的负流动在铝侧沉积更多的钢,导致更高程度的宏观偏析。与熔池宽度扩展中的低硫钢 (30 wt.%) 相比,这些反向流动模式将钢与铝的混合率提高到约 57 wt.%(补充图 2)。鉴于铝钢焊缝的不规则混合模式与指状突起的形成有关,因此有必要评估熔池中的元素分布。铝侧的 Fe 含量从熔池中心到边缘区域发生了巨大变化,重量百分比从 80% 左右下降到 60% 和 20%(图 5c),X 射线结果还表明 Fe 的重量百分比凝固后随着熔池膨胀从 64%(区域 1)下降到 28%(区域 3,图 1b)。在熔池边界处形成的指状突起中,Fe 含量有所上升(图补充图 2)。这是因为半固态结构的形成导致熔化过程中Fe(还有Cr和Ni)含量的积累和瑞利-泰勒型不稳定性。虽然标记的混合区域更接近铝基体,但在重力作用下,Fe的质量分数与Al的质量分数相似。这导致在熔池边界形成富铁枝晶(图 5 和补充图 4)。能量色散 X 射线分析揭示了焊池中 Fe 含量的波动。不同的Al与Fe含量比可以从熔池中经历非线性和不均匀熔化过程的瞬态多相形成和逐步混合模式来理解。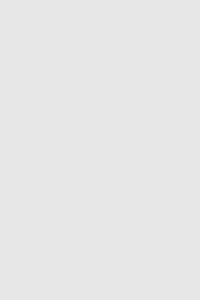 反映铝和低硫钢电弧焊的数值模拟结果(图 2d,e)通过预测不对称焊池形状和基体的熔化顺序(与补充图所示的熔池宽度相比)合理地匹配射线照相观察结果。. 1,增量变化的平均精度为 10%)。至关重要的是,该模拟再现了在可比较的时间尺度上观察到的指状结构,由于与熔池中的熔体动力学密切相关的成分的高度非线性传输[39],混合界面具有相同的不规则性(图 2e 和补充图 4)。模拟结果表明,进入铝基材的热传递量更大,并在 700 至 1400 毫秒内生成了深熔池(图 2)。随着铝钢焊接过程的继续,在 1 至 2 秒内,界面处建立准稳态,混合熔池的尺寸保持稳定。根据 Al-Fe 相图 (Suppl.图7)中,与周围的液态铝相比,混合区域中较高的铁溶质水平提高了熔点,从而形成稳定的界面[48]。这种独特的状态一直存在,直到电弧传递更多的热量以重新熔化混合物区域。在此阶段,在1至2秒之间,铝液中的钢含量迅速增加。这相当于中部地区的重量百分比从 3% 增加到 59% 左右(补充图 2),并导致钢材运输停滞(图 2a、b)。由于铝钢混合物的熔点随着钢含量的增加而升高,当来自电弧的额外能量被传输到熔池时,钢向铝的传输继续进行。这种运输的主要指标是形成铝钢熔池界面处出现手指状突起。在这里,液态铝和钢的阿特伍德数约为 0.49,在这种情况下,瑞利-泰勒不稳定性驱动了铝侧铝-钢界面处这些指状突起和不规则形状的形成。此外,液体之间粘度和密度的差异也可能是促进此类形成的另一个影响因素。这种手指形成的现象可以在实验和模拟结果中观察到(图2、6和补充图3、4)。模拟还表明,熔池中的平流和扩散通量产生相对平滑的成分分布,因此液相线温度也产生平滑的分布;进一步支持了实验观察到的指状结构是异种熔体界面处的瞬态半固态结构这一假设(根据图6的模拟,指尖处的温度约为950-1100 K,而熔化温度含 45-50 wt.% Fe 的 Al-Fe 相远高于 1300 K)。因此,在高温流体聚集和重力作用的共同作用下,铝熔池边界中下区域形成了指状突起。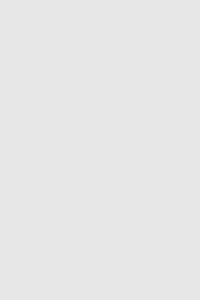 在铝-钢情况下,输送到铝侧的钢的温度变得比其熔化温度低得多。这种过冷允许快速凝固,并且根据热溶质条件,形成可以是蜂窝状的或树枝状的。实验和模拟结果需要更高的时空分辨率才能准确解析结构的形态。熔池内的中间固相形成和相关的传质过程显然是由富含钢的致密层(位于顶部)到其下方的低密度层的重力加速扩散驱动的。随后,随着密度较大的富钢熔体在富铝熔池上方积累,铝钢熔池边界处的瑞利-泰勒不稳定性发生变化,并导致湍流和随后的混合。这种中间固相的形成可能改变了流动模式。中间固相显然中断了一般流线型的流动(如果没有这样的固体)。铝-钢焊接时会出现逐渐熔合的现象,导致铝熔池中钢含量的周期性积累,并导致明显的宏观偏析。大约 40% 重量百分比的钢堆积在熔池中心附近,直到局部液相线温度(在熔池边界)增加,触发了钢-铝界面处的部分再凝固,正如模拟所证实的那样(图2. 补充图 2、4)。铝-钢焊缝界面处指状瞬态固相结构的形成很大程度上归因于两种金属性质的固有差异。与钢相比,铝较高的导热率和较低的熔点可能导致铝更容易熔化,并具有显着的表面张力梯度,从而导致铝-钢界面处的不相容性。密度差是导致表面不稳定和指状结构形成的另一个关键因素,同时它也直接取决于材料的熔化体积。两个金属基板。在铝-铜焊接的情况下,熔化的铜的体积可能不足以在宏观水平上形成指状突起。因此,控制这些突起的一种潜在方法可能是在焊接过程中仔细管理热量输入,以确保更均匀的温度分布和与温度相关的表面张力梯度,这有助于最大限度地减少这些突起的形成和界面不相容性。 根据实验观察,为了能够在计算机上优化不同类型的焊接工艺,对铝和低硫钢对进行了额外的模拟,其中焊接电极尖端在含铁部件上偏移了 2 毫米。由于电流密度主要流向具有相当高熔点的钢基材,因此电极的这种补偿位置导致形成明显不同的熔池形状。因此,在开始熔化之前需要更长的时间(约 2 秒),如图 1 和 2 所示。如图 7 和 8 所示。在这种情况下,初始熔化区域的尺寸再次明显小于原始情况(电极偏移为零)。然而,一旦建立了熔池,每种材料的熔化体积就更加相似,与零偏移情况相比,导致熔池更加均匀。然而,与凝固事件相关的冶金学可以在焊接接头的组成相中发挥不同但重要的作用,这完全取决于相关的独特成分。 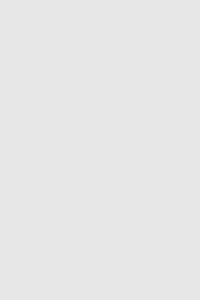
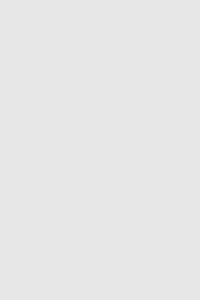
结论 实时快速 X 射线成像观察和磁热流体动力学模拟用于识别异种金属焊接过程中熔池的时间演变。我们进行了仔细计划和详尽的研究,以辨别热场、主导流动驱动力、表面活性元素和金属合金中固有的物理差异对异种金属焊接的影响。观察和分析有助于了解熔池界面形成和演化过程中的基本过程行为。这项工作的结论如下: (i)通过比较不同金属配对在熔焊下的原位 X 射线图像,我们清楚地证明了金属合金的固有物理和化学性质如何极大地影响焊接性能。熔池的形成和熔融金属的混合方式。热性能的巨大差异表明直接影响了铝-钢和铝-铜焊接中观察到的独特熔合模式。 (ii) 表面活性元素在异种金属焊接熔池的形成中发挥着重要作用。原位X射线结果表明,硫含量的差异会引起铝钢焊接中流动模式和熔融金属混合模式的变化,导致熔池中溶质偏析的发生。 (iii)结果揭示了强热场下变化的温度和溶质场如何促进铝钢焊接中混合液体的瞬时准稳态以及随后形成指状瞬态固相。两种材料的密度和熔点差异都对瞬时固相形成的开始产生显着影响。指状突起与熔池内部的溶质偏析直接相关,导致内部不均匀性和焊接质量差。 (iv) 基于原位 X 射线成像和模拟,对异种金属焊接中的偏置热源进行了计算机测试,以检验界面形态工程的潜力。它设想通过控制贱金属的熔化量来解决异种金属焊接中长期存在的宏观偏析问题的良好前景。 论文信息 https:///10.1016/j.actamat.2023.119232 https:///10.1016/j.actamat.2023.119232
|