
(1)混凝土浇筑时仅利用个别窗口,混凝土流动距离过长,距灌注窗口远处易因混凝土供应数量不足、压力不足而造成脱空。
(2)混凝土浇筑过程中未振捣密实,浇筑完成后混凝土受自重下沉,造成拱部脱空。
(3)混凝土浇筑至拱部时,难以精确掌握混凝土量,拱部混凝土灌注量不足而致使拱部局部形成脱空。
(4)拱顶混凝土采用一次泵满的方式施工,捣固后混凝土下沉致使拱顶形成空腔。
(5)下坡施工时,浇注段与上循环之间会形成空气囊(拱部)而造成衬砌背后空洞。
(6)混凝土扩散度不足,封顶时局部泵送不到位,造成二衬脱空。
混凝土自身收缩、徐变由于混凝土本身的特性,其在浇注后要发生收缩和徐变,致使衬砌与围岩或防水板间出现空隙,此种原因造成的空隙一般小于2cm。
通过上述分析可知,影响二衬脱空的因素涉及施工的各个环节,需从开挖、初支、防水板铺设、模板、砼浇筑、砼振捣、养护等环节加以控制。工艺控制要点如下:

(1)采用爆破施工时,现场严格按照钻爆设计并根据实际围岩情况,做好钻爆方案及现场工艺优化,保证开挖断面施工质量符合设计和验标要求。
(2)初支施工时设置厚度控制标识,施工人员做好技能培训和交底,严格控制喷射混凝土厚度和表面平整度,保证初支施工质量符合设计和验标要求。
(3)防水板铺设松紧适度,固定点间距严格按设计要求布置,搭接长度、焊缝及固定点焊接,严格按防水板施工作业要求施工到位。
(4)模板台车按衬砌施工作业要求施作,模板加固支撑体系严格检查,并采取防止上浮措施,各预留孔洞封堵到位,拱部浇筑预留通气孔。
(5)混凝土浇筑严格按照衬砌施工作业要求施作,严控施工浇筑顺序、捣固等工序的施工质量。
(6)拆模时间不宜过早,在初期支护变形稳定后施作的二次衬砌砼强度应达到8MPa以上;初期支护变形稳定前施作的二次衬砌砼强度应达到设计强度的100%,在模板台车端面上贴反光轮廓标,警示运输车辆,避免撞击造成台车移位。
注浆防脱空采用纵向预留管道法,在衬砌防水板施工时,在衬砌拱顶中央位置,安装注浆管与排气管。管体采用φ30PVC,长度等于衬砌长度加200mm外露,注浆管布设溢浆孔,孔径φ6~8mm,间距15~20cm,呈梅花型布置,外露段与注浆机连接,排气管不布孔,按照排气要求安设于注浆管侧面。施工可参照下图:



注浆管与排气管同防水板采用强力胶带粘贴牢固,按照0.5m一个节点固定,安装时应避免管体将防水板捅破。
本循环衬砌施工完成后,下循环衬砌施工前,并在孔口封堵材料达到一定强度后,进行衬砌拱顶注浆,注浆压力控制在0.2Mpa以内,注浆材料采用M20水泥砂浆或水泥浆,机械拌制,施工时严格按配比称量拌制,稠度控制在14~18s之间。注浆时,设备注浆管与衬砌注浆管固定牢靠,注浆压力达到0.2Mpa或排气管出浆时即可终止注浆。注浆结束后,应及时将注浆孔封堵密实。
在衬砌施工200m后即安排雷达检测,及早发现问题,以便采取措施,改进施工工艺、总结提高,减少后续施工衬砌脱空现象的发生,促进衬砌质量的提高。

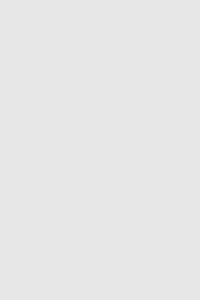