有删减,如需全文,请购杂志或前往知网下载 作为汽车轻量化的重要途径,铝合金板料在汽车覆盖件上的应用是促进汽车轻量化的重要手段之一。研究表明,汽车每使用1kg铝,可减轻自身质量2.25kg,减重效应高达125%,汽车质量每下降10%,燃料效率可提高6%~8%。采用铝合金板料代替钢板材料,可使车身质量减轻30%~40%,承受同样冲击载荷,铝板比钢板多吸收冲击能50%。铝合金板料因具有高强度、耐腐蚀性、适合多种成形方法、较易再利用等优点替代钢板材料。 由于微观结构差异,汽车用铝合金板的成形性能与汽车钢板相比有较大的差异,传统钢板的成形理论和技术无法直接套用在铝板上。铝板的弹性模量是钢板的1/3,因此铝板成形的回弹量约是钢板的3倍,无论从成形性还是从回弹角度分析,铝板成形都有别于传统的钢板成形。 1零件冲压工艺分析 
图1 侧门外板及断面结构
侧门外板作为车身重要的外覆盖件,其成形质量直接影响整车的外观质量和品质。图1所示为某车型的侧门外板,外形尺寸为1152mm×685mm×1.5mm,材质为铝板5251_O。 
图2 工艺补充参数设置
零件冲压工艺为:拉深、修边、翻边。依据零件形状特点,通过AutoForm软件在拉深深度最浅和对称均衡触料以及最大接触面的原则上确定冲压方向,并通过软件的快速建模获得压料面和工艺补充。由于铝板延伸率较低,一般为25%,且塑性流动性差,压边圈应尽量光顺,避免曲率变化大,工艺补充各个参数都要大于钢板材质,图2所示为工艺补充参数设置。 根据上述分析确定最佳的工艺补充类型以及冲压方向,如图3所示,并生成凸模、压边圈以及凹模,选择材料参数,确定冲压压边力为1200kN,摩擦系数为0.14,进行CAE分析,经过反复调整拉深筋参数,最终确定板料大小。
(a)成形极限

(b)减薄率

(c)主应变

(d)次应变
图4 拉深分析结果评测 拉深筋作为控制板料流动速度的主要因素,为有利于分析并快速调整,前期分析拉深筋采用虚拟拉深筋,最终确定虚拟拉深筋阻料系数为0.75,对应板料长宽为1350mm×850mm。经分析并进行结果评测,FLD(成形极限)通过,如图4(a)所示;减薄率超过0.03且均匀,说明成形充分,如图4(b)所示;主应变中间区域未超过0.03,局部刚性存在问题,如图4(c)所示;次应变均为正值,如图4(d)所示,棱线滑移均超出圆角,可以根据此分析进行工艺和模具设计。
(a)修边后回弹

(b)中间塌陷结果
图5 修边后回弹及中间塌陷结果 由于零件型面比较平缓,且翻边均为直线翻边,不存在因弧度翻边造成的多料或少料的情况,因此翻边对零件回弹影响较小。回弹的主要原因是主应变不均匀和塑性变形不充分,为了后期指导调试进行回弹验证,通过分析修边后的回弹,找出影响零件回弹的因素,以便更好地减小零件成形时的回弹。根据以上拉深分析,修边后进行回弹分析,修边后回弹结果显示零件中间数值为负,如图5(a)所示。经过对比,显示中间结果为塌陷,如图5(b)所示。由于现场检测零件为样规弧板检测,即通过零件断面线加工一个断面样板,通过断面样板与冲压件的形状进行贴合对比,回弹数据会出现叠加效应,即上下回弹之和为总回弹。根据对比结果,零件中间位置回弹最大约5mm。经过分析,引起此回弹和塌陷的因素为主应变应变不充分及分布不均匀导致的。由于材质为铝板,延展性较钢板差,继续拉深无法加大主应变解决此回弹,鉴于铝板塑性变形越小回弹越小的特点,只能通过减小零件的成形充分性,使应变尽量均匀,减小回弹。
(a)增大板料流入量的回弹
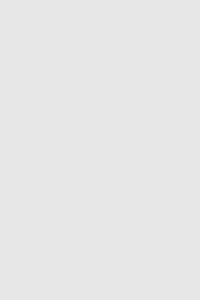
(b)中间塌陷结果
图6 增大板料流入量的回弹及中间塌陷结果 通过对虚拟拉深筋阻料系数由0.75更改为0.65,加大板料的流入量,减小铝板零件的塑性变形充分性,并降低应变值,经过回弹分析,发现总回弹值有所下降,零件中间位置最大回弹量约2.06mm,如图6所示。证明通过减小成形的充分性,尽量减小铝板的塑性变形,对回弹的减小有明显的效果。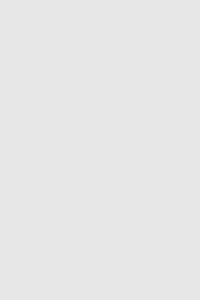
(a)虚拟拉深筋阻料系数0.5时的回弹
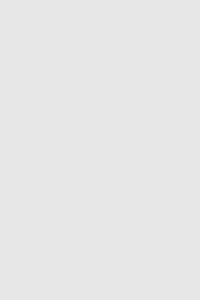
(b)中间塌陷结果
图7 虚拟拉深筋阻料系数0.5时的回弹及中间塌陷结果 为了得到更小的回弹边界条件,对虚拟拉深筋和流入量继续调整,经过反复分析,最终得出虚拟拉深筋阻料系数为0.5,与虚拟拉深筋阻料系数为0.75时相比,板料流入量长度方向多流入了约10mm,此时中间最大回弹量已经减低到1.3mm,如图7所示,若继续增大板料流入量,不但不会减小回弹,反而会加大回弹量。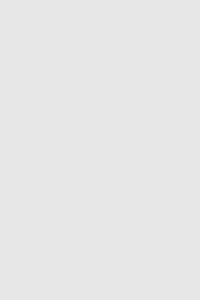
根据上述结果,对工艺型面进行处理,如图8所示,通过灰色框为边界,对中间点做1mm的隆起处理,并通过白色线对2个断面进行弧度处理。后期现场调试尽量提高研合率,通过型面处理和板料的厚向形变硬化以减小回弹。 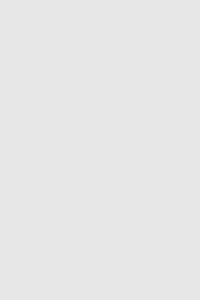
(a)研合率不足时成形零件状态
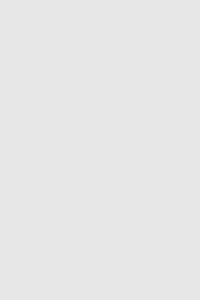
(b)流入量与分析结果一致的成形零件状态
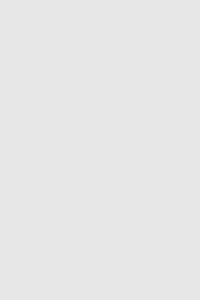
(c)重新加工型面回弹处理零件状态
图9 现场各阶段回弹测量数值 模具进入调试阶段后,最初由于表面粗糙度值偏高和研合贴合率不足60%,导致板料流入量较小,零件塌陷回弹较大,最大处约6.5mm,如图9(a)所示,通过调试减小拉深筋尺寸和压边力,使板料流入与分析结果一致后,零件回弹减小到2.5mm左右,如图9(b)所示。经工艺型面回弹补偿处理,通过降低模具闭合高度的方式重新加工模具零件型面,调试检测,零件回弹减小到0.5mm左右,如图9(c)所示。通过最终的模具研合率,成形的零件顺利通过验收。▍
|