 图1所示零件数学模型为汽车左右后纵梁前段,料厚1.5mm,材料为加磷高强度冷连轧钢板B250P1,结构件用材料,有利于部件减薄,适用于对抗凹陷性能要求较高的零件,外形尺寸为328mm×156mm×269mm。根据经验分析,此零件的造型不利于零件的最终成形,大拐角的Z型处成形时易开裂、起皱,又因为材料强度高、难成形,且修边线形状不利于后期修边模修边刀块结构的设计和布置,该零件的冲压工艺性差,必须经过形状调整才能成形。良好的冲压工艺性应保证成形零件质量稳定、工序数目少、材料消耗小、模具结构简单、操作安全和方便等。 在保证零件使用要求的前提下,经CAE软件AutoForm模拟分析,对零件的形状、尺寸、精度要求进行合理的修改。制件改进前CAE分析结果如图2所示,F处开裂严重、G处起皱严重且经过增加吸皱筋厚度后,G处起皱问题仍不能完全消除,H、I、J处的起皱、开裂经后工序模具整形优化可消除,根据冲压成形经验和软件分析结果,零件造型的局部修改如下。根据经验,图1中A、B、C、D、E处的工艺缺口增加了修边模设计制造的难度,其中E处的修边线最为复杂、制造困难,需提请工程变更申请书(engineering change request,ECR)更改零件边界线,更改后的零件形状如图3所示,将A、B、C、D、E处工艺缺口补齐,减小修边的难度,局部加宽修边法兰面(加宽3~13mm),便于布置修边刀块,使零件E处更改后达到修边目的。
 根据软件分析结果,图2中F、J处开裂严重是因为R圆角太小,不利于拉深时材料的流动成形,需提请ECR,加大局部零件R圆角。图3所示b处零件圆角由R8.5mm更改为R30mm,c、h处零件圆角由R11mm更改为R20mm,d处角部球化SR25mm,经分析零件改进后有利于拉深成形,最终解决开裂问题。根据软件分析结果,零件成形时,在拐角部位易产生起皱,如图2中G、H、I处所示,且后期难以通过钳工调试解决,影响零件成形质量,必须在前期将起皱问题减到最小状态。图2中G处过渡剧烈(90°),CAE软件分析零件拐角处起皱明显,需提请ECR,增加如图3所示的j处长90mm、宽30mm、深7mm的渐变吸皱筋,优化成形起皱问题,而由于零件k处ϕ10mm的孔距离吸皱筋太近,为便于模具结构的布置,需提请ECR,孔位向端头移动10mm。 根据经验,图3中f处ϕ14mm的圆孔距离成形R角过近,后工序整形时孔位有变形风险,因此需提请ECR,将此孔向零件中心位置移动7mm。 为保证零件成形质量将图3中e处的圆孔凸台R圆角半径R6.5mm更改为R10mm,以减小材料流动阻力,降低零件开裂的风险。
 由于零件造型的特点,存在2处近90°的结构成形(外90°易开裂、内90°易起皱叠料),拉深成形时一般要考虑:①零件能够顺利成形并充分拉深以保证零件的刚度;②工艺补充部分尽量少,以提高材料利用率;③拉深是实现零件的第一道工序,要考虑拉深工序完成后能顺利实现切边、翻边、冲孔等后序工作。结合以上3点并考虑零件是梁类制件,要控制零件的起皱、回弹和扭曲才能满足装车使用要求,所以拉深时的冲压角度要有利于起皱、回弹和扭曲的控制。零件为左右对称件,采用左右对称的双拉深成形,既有利于模具成形零件时的压力机平衡,又有利于提高生产效率。零件成形工艺方案:拉深→粗修边→精修边、冲孔→整形、侧整形,如图5所示。
(a)拉深 (b)粗修边

(c)精修边、冲孔 (d)整形、侧整形
图5 工艺方案排布 拉深工序压边力为800kN,拉深力为2500kN,四周由定位板定位,由于加磷高强度冷连轧钢板B250P1的特性和零件的成形性能,将拉深工艺零件的侧壁拔模角向外放大15°(后工序通过整形消除放大角度),以便于零件一次拉深成形。 粗修边工序以零件形状定位,对零件周圈进行修边,在该工序上完成修边(粗修),但局部由于修边角度太小,难以一次修边完成,待后续精修完成。 精修边、冲孔工序以零件形状定位,冲压方向沿拉深方向旋转50°,调整修边角度以实现粗修边工序未完成的修边以及精修零件四周,同时零件所有的孔在该工序冲压完成。 整形、侧整形工序以零件形状一端的边线定位,冲压方向沿拉深方向旋转20°,将拉深工序侧壁放大的15°拔模角整形到位,同时实现法兰面的整形。 由于该零件相对较小,为节约压力机资源,模具结构采用左右件共模的双槽模具结构,即以1模2件的方式进行生产,为便于回弹、扭曲的调整,在整形、侧整形工序使用侧整形斜楔。 单动拉深模结构,模具外形尺寸:2090mm×1620mm×850mm。凸模采用MoCr铸铁、局部表面淬火,热处理硬度50HRC以上,凸模结构如图6所示。压边圈受拉深力部位采用材质锻件Cr12MoV镶件,整体淬火后热处理硬度58~62HRC,特别注意的是镶件分缝处必须采用斜拼方式,拼缝方向与材料流动方向角度θ≥10°,压边圈如图7所示。
图7 压边圈

图8 凹模
凹模采用材质锻件Cr12MoV镶件,整体淬火热处理硬度58~62HRC,淬火硬度高、耐磨性能好,镶件拼缝必须采用斜拼方式,拼缝方向与材料流动方向角度θ≥10°,如图8所示。粗修边模具结构外形尺寸:1930mm×900mm×850mm。 精修边、冲孔模结构外形尺寸:1940mm×1110mm×900mm。上、下模修边刀块和废料刀块都采用锻件Cr12MoV镶件,整体淬火热处理硬度58~62HRC,数控仿形加工,淬火硬度高、耐磨损。

图9 整形、侧整形模结构
1.下模座 2.上模座 3.斜楔驱动块 4.侧整形斜楔 5.压料芯 6.侧整形斜楔 7.斜楔驱动块 8.侧向力导滑块 9.凸模 10.侧向力导滑块整形、侧整形模结构如图9所示,模具外形尺寸:2290mm×1450mm×850mm。上、下模侧镶件、侧驱动器采用HT300;整形镶件(整形凸模)采用锻件Cr12MoV,整体淬火热处理硬度58~62HRC,数控仿形加工,淬火硬度高、耐磨损。工作过程:下模座1固定在压力机工作台上,上模座2固定在压力机滑块上,斜楔驱动块3和7、凸模9、侧向力导滑块8和10固定在下模座1上,侧整形斜楔4和6、压料芯5固定在上模座2上。零件放置于凸模9上,压力机滑块带动上模座2、侧整形斜楔4和6、压料芯5一起下行,当上、下模闭合时压料芯5与凸模9压紧零件,侧整形斜楔4和6分别在斜楔驱动块3和7、侧向力导滑块10和8的共同作用下向中间水平移动,同时压紧凸模9的两侧实现侧整形。 模具结构采用侧整形斜楔的侧整形结构,模具结构复杂,但便于后期实际零件回弹补偿调整,钳工调试简便易操作,使最终零件的成形容易达到使用要求。模具制造完成后,在压力机上对其进行动态精度试冲验证,通过试冲的工序件鉴别冲模制造的质量,并发现问题消除制造缺陷。模具的调整很难一次成功,需要反复进行试冲,周期长、机床使用时间和材料消耗大,因此必须集中技术力量解决调整中出现的问题。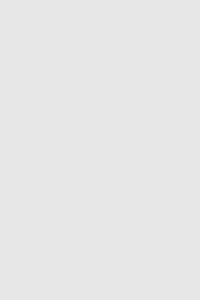
图10 拉深工序件
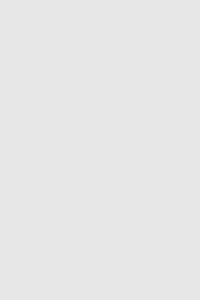
图11 增加吸皱造型
拉深模在冲压设备上试压,工序件如图10所示,起皱严重甚至叠料,零件还存在成形多料问题,为弥补横向吸皱筋的缺陷,在零件立面中增加4个吸皱的造型,如图11所示,可以有效缓解零件的起皱。模具经反复装机研合调试,最终调试的零件局部压伤、R角不顺畅、起皱问题基本消除。经过最终的零件局部结构更改和模具调试研合,实际生产的零件达到设计要求,零件合格率达到95%。▍原文作者:彭文会 ▍作者单位:山东御捷马新能源汽车制造有限公司
《模具工业》杂志不接受任何代理方式投稿,本杂志唯一官方网站——模聚网,敬请作者访问网站投稿http://www./mjzz/ 订阅杂志请加发行部QQ2762515535或致电0773-5861906垂询
|