“ 在深度饱和的电机市场,同质化竞争、价格战让所有人都疲于应战并感叹前景黯淡。当下,我们越发能够感受到:“技术创新才是是价值创造的原动力,一个底层技术的突破会带来一系列应用创新、供应链发展的机会”。要参与这些增量蛋糕就需要及早识别机遇并参与创新。而这首先要从开阔眼界开始,这也是蜗牛团队一直跟踪国际先进电机技术的原动力。本期我们带来美国最新的电机技术进展。 ”
Elt091项目 Elt091项目是美国能源部DOE资助的一个最新的联合开发项目,立项于2017年,目前正处于关键发展阶段。该项目由特拉华大学、爱荷华州立大学、Ames实验室、联合技术研究中心等四个机构联合开发的,我们暂时称为四方联盟吧。改项目的核心技术为两个材料创新技术+1个应用创新技术。1.开发替换稀土磁材的低成本高性能磁材 MnBi材料; 2.开发低损耗高导磁能力的6.5%Si 的超级硅钢材料;这两种材料技术的突破带来一个电机应用技术的新发展:高功率密度低成本无稀土技术。
三个技术简单的逻辑关系如上图所示,我们先从材料技术发展讲起。 MnBi磁材 MnBi磁材是Mn和Bi合成的一种纳米晶材料,它具备很好的磁性能力,一款典型的MnBi合计 剩磁在0.6T左右,磁能积在8-10MGOe之间,整体性能在永磁体的30-40%之间。这种材料备受“四方联盟”青睐,号称是唯一可以达到DOE2025成本和性能要求的软磁材料。钕铁硼因含稀土太贵,而铁氧体和铝镍钴性能又不易达标。 MnBi磁材受青睐有内外两个原因,内在的原因是确实有独特的性价比优势。Mn和Bi这两种材料分布很广,成本相比稀土材料要低的多,大批量生产后磁材的价格可在10-26$/kg,而42UH的价格在60$/kg左右。另外这种磁材还有一个明显的优点,就是矫顽力正温度系数,在220℃范围以内矫顽力随温度提高和提高,且磁密和磁能积几乎不受温度的影响。
这种优秀的特性特别适合驱动电机,因为MnBi的矫顽力高(40%钕铁硼)且随温度变化而增长,这会降低很多潜在的退磁风险。另外磁性能对温度不敏感的的特性也极大了提高了电机的可靠性, 并降低控制的难度。 MnBi被美国看好的另外一个原因涉及到政治问题,随着中美脱轨的发展,美国急于摆脱对中国的稀土依赖,因此发展无稀土、少稀土的磁材技术就有了政治基础。  但MnBi材料也有明显的缺陷其一是材料的磁能积不高,当前实验室最好的水平能做到12MGOe,相当于钕铁硼N48UH的25%,虽然理论上限可以达到20MGOe,但成长空间仍然有限,这会导致电机磁密受限、进而导致功率密度无法满足DOE2025的要求。因此这种材料的创新不能单独成立,还必须和其它技术创新相匹配,形成组合策略。因此“四方联盟”选择了“超级硅钢”和它做搭档。超级硅钢:6.5%Si 这几年,Ames实验室一直在进行超级硅钢的研究,目前已具备小规模生产的能力。他们的目标是获得一种具备革命性意义的“低高频铁耗,高导磁率”的硅钢材料。 高性能电工钢的技术有很多种技术路线,包括:钴铁合金、镍铁合金、非晶材料。Ames选择的是高硅钢路线。那么为什么选择6.5%Si含量是因为这个比例下,硅钢具备最低的铁耗和最高的导磁能力。 除了6.5%的硅含量恰到好处,这种合金还需要独特的制成工艺。有别于传统的工艺,这种材料是先从颗粒开始做起的。具体的成型工艺分成四步:利用晶体成型技术先制造成几克到几百克不等的碎片; 利用热压工艺将碎片制造成原柱状体; 对柱状体进行1100℃*2h的去应力退火;
切割成需要的厚度;
 利用上述工艺制成的硅钢材料,隐含一大关键信息,就是这种材料的绝缘工艺是“亚颗粒级别”。如上图所示 每个碎片颗粒内含了多层“铁-绝缘”复合结构。类似非晶材料, “亚颗粒绝缘”的架构使得涡流铁耗大幅度降低。由此我们也能得知这种材料铁损的性能和绝缘层工艺密切相关。Ames掌握了两种无机绝缘层技术,一种是CaF2材料一种是MgO材料,目前较成熟的是前者,可以做到500nm-1um的绝缘厚度,使得合金材料的电阻率到322.5uΩ-cm,电阻率越大材料的铁损就越小,当采用MgO材料绝缘工艺时,电阻率可以达到1111.5uΩ-cm,但相应的叠压系数只有84.8%,叠压系数过低会降低导磁能力。所以这种工艺也存在跷跷板效应:“铁耗低-导磁能力弱,导磁强-铁耗就高”。  尽管有跷跷板效应的存在,这种新材料-新工艺制成的硅钢材料。其铁耗-磁导率都优异于普通硅钢水平。如下图所示,Ames推出的一款GO2P23牌号的 6.5%Si材料,同样制成0.2mm的片子,其在400HZ和1000HZ下的铁耗比宝钢的B20AT1200小30%,最高磁导率提高了270%,也就说这款产品的高低速性能都大幅度领先普通产品。而另外一个名叫“Hiperco-50”的同技术产品,表现出了杰出的饱和磁性能,饱和磁密达到2.5Telsa远超过了其它电工钢的水平。 6.5%Si具备低铁耗高导磁的双重特性,是名副其实的超级硅钢,备受联盟推荐,虽然仍未成熟,但已展开电机应用层级的开发。它将和MnBi磁材形成技术组合,服务在一款高速无稀土电机上。04 —
技术组合:高速无稀土电机 联盟采用MnBi磁材和6.5%Si钢形成技术组合,开发了一款低成本的高速无稀土电机,这种策略组合具备很强的互补性。首先要实现无稀土和低成本,需要利用MnBi的低成本优势,但是这种材料的缺点也很明显,磁能积最多只有40%的钕铁硼,单靠这种材料实现高功率密度几乎不可能。6.5%Si的高导磁特性却能很好的弥补这个缺点。其基本逻辑是:高导磁性提高了磁密饱和点,使得定子齿、轭的面积大幅度减少。腾挪出来的空间可以设计更多的铜,电密和电阻得以大幅度降低,线负荷可以取高,从而提高扭矩和功率。本质上这是用电负荷补磁负荷的策略。
 其次,采用高速化策略,高速化使得6.5%Si的低铁耗优势得以发挥、而速度提高使得同样功率下扭矩下降,磁负荷需求也随之下降,这又进一步规避了MnBi磁能积低的缺点。 这种扬长补短的策略组合令人拍案叫绝,联盟的采取小步快跑的策略,第一步先做一款10kw@8000rpm的原理验证机以磨合新技术。第二步开发满足DOE指标要求的大功率样机(这几乎是固有模式了)。下面是这款电机的具体指标。 初步设计是一款10极12槽电机,采用集中绕组结构,从下图中我们能看到,这款电机的轭部和齿部厚度非常小,这是6.5%Si的特性。而让出来的空间给了铜线,该10kw的电机的铜线用了3.4kg,几乎是我们普通100kw驱动电机的水平。因此这是一种多铜少磁的方案。 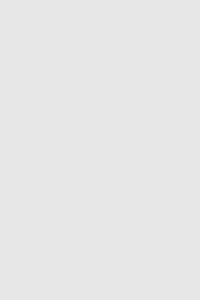
下面是这台电机的样机图,可以发现该电机的转子采用表贴式+保护套的结构。为了避免高速产生的大量涡流损耗,将磁钢分成轴向6,横向4的阵列。这种设计在一些高速电机上常见,但是否最佳值得再研究。 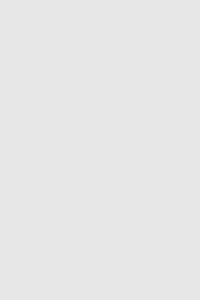 最后值得一提的是该电机采用了多目标优化设计方法,这几乎成了先进电机开发的一种常态。因为新技术的引入使得传统的经验设计方法已无法适用,必须依靠算法来寻找新的边界、新的平衡解。该电机的设计优化目标是由“结构强度-转矩密度-热极限”三类物理场目标构成的,这也预示着多物理场的联合优化设计将成为新的发展方向。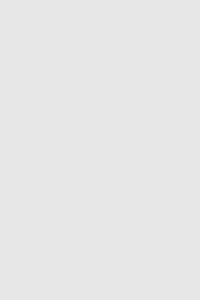
05 — 我们能学到什么 这个案子,有很多东西值得我们学习。首先技术创新才是源头活水,越是源头侧的创新,其带动的能量越大。磁材和硅钢的技术迭代,将革命性的提高电机的性能并降低成本。以往,我们擅长利用超大规模性在供应链侧降本,这种红利已经挖掘干净,持续的降本压力也使得供应链不堪重负。 通过技术革新带来成本降低、性能提升才是唯一出路。 而且新的技术的突破 将带来大量增量蛋糕的机会,给中小企业提供了发展空间。其实,我们观察到欧美国家技术创新的模式呈现组合化、联盟化发展趋势。如“四方联盟”一样,有人负责材料侧的创新,有人负责电机应用侧的优化计算把新材料的匹配性做到最佳,还有人负责产品的开发和推广。在美国“长板合作”趋势已经非常明显,这给中小企业发展提供了一种新的参考模式。
|