在工程机械类产品中常会用到类似拉板的结构,例如泵车臂架铰点中的连杆、挖掘机斗杆与挖斗铰点处的连杆、全地面起重机或履带式起重机的拉板结构等等,这些都是非常典型的拉板结构。 图0.1、泵车臂架铰点直连杆 
图0.2、挖机直连杆 
在评估泵车臂架铰点机构的连杆应力时出现最大等效应力远大于许用应力,有的还大于BS900D的屈服强度900MPa,甚至某些点达到1100~1200MPa。很显然,按照许用应力设计法评估,这些连杆结构不满足结构强度要求,需重新设计。但公司内部有不成文的规定,对于受挤压等部位(如销轴与轴套、支腿搭接位置)的应力若不超过1100MPa,则认为满足强度要求。 但这个不成文规定没有理论依据的支撑,是根据之前的设计经验总结得出的,并且之前其他泵车臂架的直连杆最大等效应力有超过超过1100MPa,在实际使用时却并未出现损坏的情况,这导致了设计人员难以把握这种拉板结构的强度评估标准。 本文以一个直连杆的受拉工况为例,从静强度和疲劳强度两个方面来进行评估,希望大家在阅读完本文后对类似结构的设计和评估会有一个更清晰的理解。 以混凝土泵车的结构设计为例,参考GB3811《起重机设计规范》的许用应力设计法评估法。工程师们希望对一种等级的钢结构材料使用一个许用应力值与计算应力值做比来评估强度。例如中长米段泵车臂架常用900钢,其许用应力为578MPa,假设某个臂架计算完后,所有点的应力值(排除所谓的应力集中点的高应力值)低于578MPa,则认为满足强度要求。但是臂架的这些应力集中点,以及受拉连杆、支腿之间搭接部位的应力往往超过了许用应力值,那么就要增加非常多的材料才能把应力降下去,实际上可能原来的结构是满足强度要求的,在实际结构设计和产品使用中也是这样,计算值超过限值,但实际使用中极少或没有出现开裂或断裂,反而是一些其他应力水平不高,之前未注意到的地方出现结构破坏了。甚至有些部件静强度计算的应力值很小,远低于许用应力,却出现结构开裂或断裂,这些情况该做如何解释?
结构载荷计算时考虑了钢结构动载系数、混凝土(输送管中混凝土满管)动载系数、6级风载、末端软管横向拉拽力以及臂架水平打泵等一系列因素,且这些因素以最危险的情况同时施加在臂架上,但泵车实际使用时这种载荷组合是非常少出现的,甚至是不会出现的,也就是说使用了虚高的假载荷作为最危险的计算载荷; 钢结构许用应力计算时也考虑了安全系数,并且有些工程师将这个安全系数提高,例如将BS900D的许用应力规定到500MPa,在评估时将500MPa同时作为静强度和疲劳强度的应力标准,低于这个应力值就认为不会发生静强度破坏和疲劳破坏,这种做法把静强度和疲劳强度混为一谈了;一方面,500MPa这个静强度许用应力过于严格,很多过渡圆角等应力集中点附近的应力无法通过;另一方面,影响结构疲劳寿命的主要因素是结构的应力集中情况,应力幅、应力循环次数等,应力幅表示最大应力与最小应力差值的一半,和承受静载下的最大应力没有绝对关系。 在评估结构静强度时各种规范推荐许用应力设计法和极限状态设计法。在GB/T3811《起重机设计规范》中,分成了三个载荷组合,并分别规定了对应的强度安全系数。
图1.1、GB/T3811中许用应力计算 臂架载荷对应组合B,按1.34的安全系数计算,BS900D的许用应力应为578MPa。
图1.2、BS900D钢许用应力值 将BS900D的许用应力应为500MPa过于苛刻,建议做调整。从材料力学课本上可以看到,塑性材料(低碳钢、高强度合金钢等)试件在承受轴向载荷后,一般经历4个阶段后才会被拉坏,也就是说试件的应力要达到抗拉强度后才会被拉坏。
我们平时做的强度评估基本是静强度评估,计算的最大等效应力小于许用应力即认为静强度满足设计要求。但并不是说大于许用应力就会造成结构破坏,最大等效应力在局部超过屈服强度后也不会立即破坏,只会造成局部位置出现塑性变形。 00:12 图1.3、试件拉伸试验 
图1.4、试件应力应变曲线 但是对于承受动载荷的部件,如果动载荷循环次数超过一定次数,例如在GB50017-2017《钢结构设计标准》的16.1.1条款中规定当应力循环次数在50000次以上时需做疲劳计算。这里要强调本文探讨的是高周疲劳,也叫应力疲劳,基于材料弹性理论。而低周疲劳,即应变疲劳,静强度下的等效应力一般接近或超过屈服强度而发生塑性变形,在一定的交变应力下一般可能少于10000次就发生破坏,限于个人水平,这里不做讨论。图1.5、GB50017中疲劳计算一般规定 本文讨论的直连杆是非焊接件,相关的理论、标准和实验数据表明:对于非焊接件,抗拉强度越高,其试件的疲劳极限也越高。但焊接件和非焊接件的疲劳机理完全不同,IIW和BS7608标准将二者按照细节结构做了分类。董平沙博士提出基于主结构应力法的焊接结构疲劳寿命评估,将不同焊接接头形式、厚度、加载模式的疲劳S-N数据统一起来,形成了一个主S-N曲线,如下:
图1.6、主S-N曲线 这里需要说明的是:本文分析的直连杆是单板形式的非焊接结构,使用的是材料的S-N曲线,而非上面的主S-N曲线。本文以某直连杆为研究对象,直连杆成对出现,这里假设单个直连杆受到的最大拉力为700000N,其他尺寸等数据如下:
图2.1、直连杆示意图及相关尺寸 这里介绍两种理论计算方法,分别参考手册计算和曲梁正应力公式计算,具体如下:这里参考航空工业部科学技术委员会编写的应力集中系数手册,在手册5.15中对受拉耳片的最大应力计算采用名义应力乘以应力集中系数的方式计算得到最大应力,如下图所示,本文的直连杆结构为半圆形: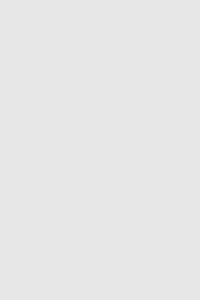
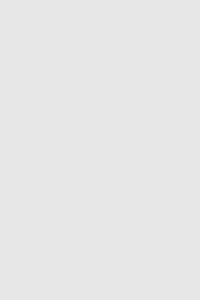
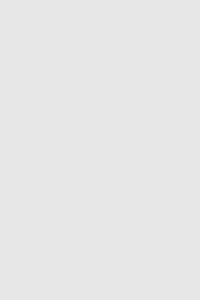
图3.1、半圆形耳片轴向拉伸时应力集中系数曲线图 通过曲线插值得到应力集中系数约为2.9,由计算公式得到A点处的最大正应力为: 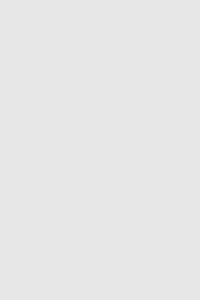 对于这种半圆形拉板结构,假设拉力在轴孔内壁按正弦分布,通过求出a-a和b-b两个截面上的力和力矩,再代入曲梁正应力计算公式得到两个截面上的正应力,由于b-b截面内侧的应力最大,这里仅考虑这个最大应力,很显然,这是个拉应力。这里不对这两个截面正应力计算公司做推导,这些在王金诺编写的《起重运输机金属结构》一文中有详细的推导过程,有兴趣的同学可自行查阅。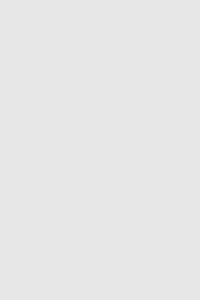
图3.2、销孔拉板计算示意图 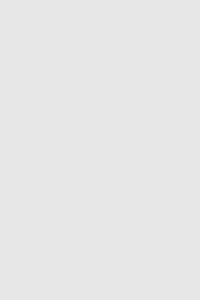
图3.3、销孔拉板关键点正应力计算公式 将参数代入后得到b-b截面内侧的最大应力为727Mpa。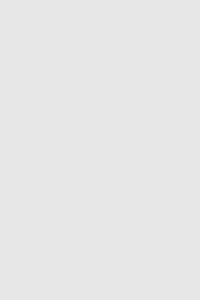
图3.4、B-B截面正应力计算 接着采用Ansys Workbench软件计算直连杆单板的应力,考虑到轴孔与销轴的力传递,这里采用接触非线性,摩擦系数设置为0.15,具体的接触非线性设置这里不做详细说明。为减少计算量,这里仅考虑单个直连杆,同时也不考虑销轴本身变形对直连杆轴孔造成的单边挤压情况,最终计算模型如下: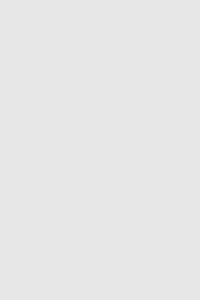 前面计算得到的是B-B截面内侧的正应力,作为对比,这里也提取这个对应截面上的正应力,其最大值为704MPa,如下: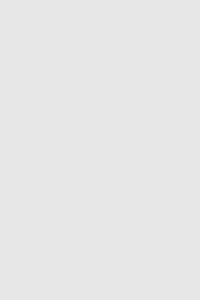
图4.2、B-B截面内侧的正应力 有限元计算值(704MPa)与理论计算值(709MPa及727MPa)非常接近,这些数据之间的偏差做如下说明:
五、直连杆结构强度评估 上面两种方式都计算得到了拉板的最大正应力值,在评估钢结构时工程师们会采用Von Mises等效应力与许用应力比较,首先提取直连杆的等效应力分布云图,如下:
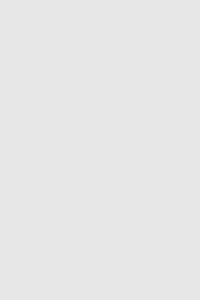
图5.1、单板直连杆等效应力云图 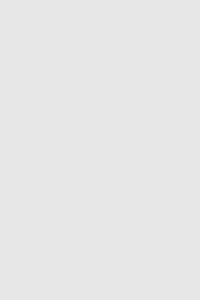
图5.2、BS900D钢许用应力值 在B-B截面位置附近最大等效应力达到了786MPa,远超BS900D的许用应力578MPa,很显然按照这个许用应力来评估是无法通过的,但这些连杆在实际使用中并未出现拉断等情况,主要有以下三点原因: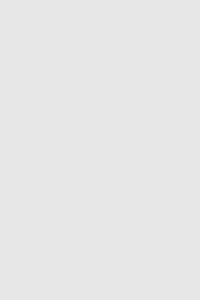 图5.3、BS900D材料力学性能参数(摘自宝钢官网用户手册)在评估结构强度时若要保证所有点的应力低于578MPa,这种方法并不合理,也限制了产品轻量化发展。这里推荐借鉴JB4732-2005《钢制压力容器-分析设计标准》,将应力线性化后再做评估,评估标准如下: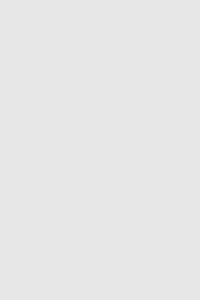 σm表示薄膜应力,σb表示弯曲应力。在有限元软件中设置评估路径,提取以上应力值按标准评估即可。先设置如下应力评估路径: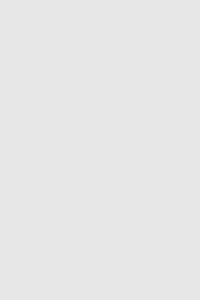
先看最大应力路径上的强度评估: 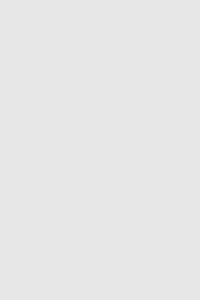
图5.5、最大应力路径上的应力值 从上图可以看到薄膜应力为265.98MPa,在整个路径上都相同;弯曲应力是先减小后增大,由于二者有正负号规定,所以叠加后的薄膜应力和弯曲应力是单调递减的,按上面的评估标准满足强度要求,如下: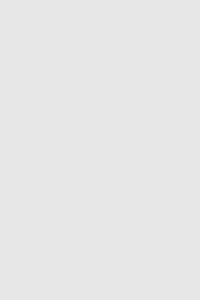
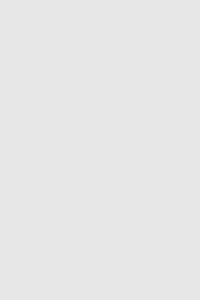
图5.6、B-B截面应力路径上的应力值 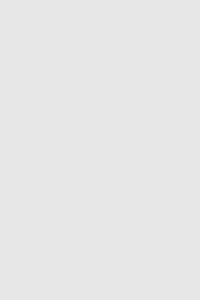 从上面的评估可以看到这个直连杆的静强度还有较大的设计余量。 直连杆的静强度满足要求,但由于其等效应力大,并且泵车在使用过程中直连杆承受的是交变载荷,有必要评估其疲劳寿命。但是我们要知道疲劳寿命评估的准确度受多种因素影响,比如:以上这些因素都会导致实际产品的疲劳寿命具有相当大的分散性。直连杆采用BS900D材料,手上没有这种材料的S-N曲线图,这里参考湘潭大学唐涛的研究生论文《高强钢箱型泵车臂架的疲劳寿命研究》中的试验数据得到的拟合后的S-N曲线,如下:
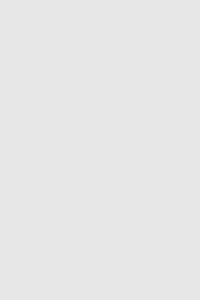
图6.1、BS900D参考使用的S-N曲线二参数方程 通过上式得到BS900D的材料S-N疲劳寿命曲线,如下: 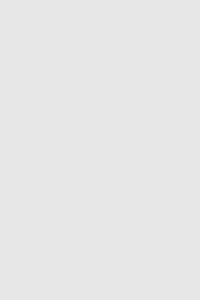
图6.2、BS900D的S-N曲线 假设这个直连杆的前端臂架始终处于水平打泵工况,考虑到前端臂架在打泵过程中有上下晃动,导致直连杆受到的拉力在700000N~560000N之间变化,如下所示:
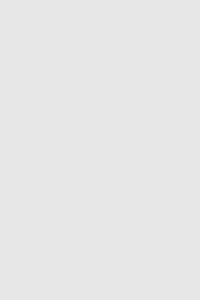 直连杆始终处于拉-拉受力状态中,假设直连杆受力变化按正弦曲线,如下: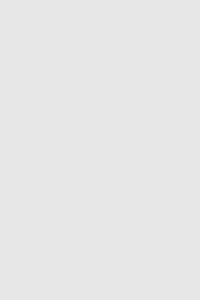
上图的T表示拉力变化周期,假设泵车每分钟泵送10次,每泵送一次为一个周期,平均每天工作4小时。本文采用Ansys Workbench自带的Fatigue Tool疲劳评估工具,按照以上假设,做如下设置: 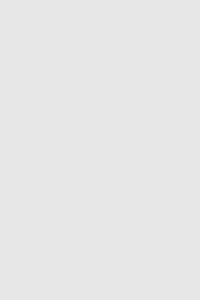 fatigue strength factor(Kf)设置为0.8,主要用于考虑将材料S-N曲线转换为零件S-N曲线,这是个综合参数,包含的参数有应力集中系数,尺寸系数和表面质量系数等。 Loading ratio为载荷比,设置为0.8,表示最小载荷与最大载荷之比。考虑到泵车结构基本都是高周疲劳,所以选择analysis type为stress life, 即应力疲劳。选择Goodman法作为Mean stress theory(平均应力理论)的修正方法,这种方法偏保守。最后选择equivalent (Von-Mises)即等效应力作为应力评估量。 运行后能看到在最大等效应力处其疲劳寿命最小,表示在经过5.5296×10^6次循环后这个位置将会出现疲劳失效。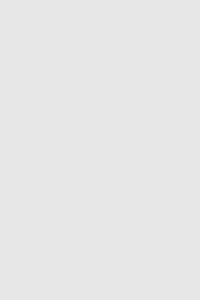 将疲劳失效循环折算成时间,为6.31年,即2304天:
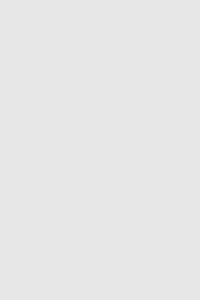
ANSYS软件提供的Fatigue tool是一个简化版的疲劳分析工具,能设置的参数少,适合在设计阶段做简单的评估,如果要对一些关重部件做疲劳分析,推荐还是采用Ncode或Fe-safe等专业软件。
专业疲劳分析软件是一方面,更重要的是输入数据的准确度。作为主机厂以从材料S-N曲线/焊接件S-N曲线试验数据以及载荷谱的实测方面入手。如果没有实测的S-N曲线,没有实际产品的工作载荷谱和由此编制的应力谱等基础数据,再好的软件也没卵用,当然,这些数据的获取需要花费大量时间、人力及Money。
|