摘要 大尺寸低缺陷碳化硅(SiC)单晶体是功率器件和射频(RF)器件的重要基础材料,物理气相传输( physical vapor transport, PVT)法是目前生长大尺寸 SiC 单晶体的主要方法。获得大尺寸高品质晶体的核心是通过调节组分、温度、压力实现气相组分在晶体生长界面均匀定向结晶,同时尽可能减小晶体的热应力。本文对电阻加热式 8 英寸(1 英寸 = 2. 54 cm)碳化硅大尺寸晶体生长系统展开热场设计研究。首先建立描述碳化硅原料受热分解热质输运及其多孔结构演变、系统热输运的物理和数学模型,进而使用数值模拟方法研究加热器位置、加热器功率和辐射孔径对温度分布的影响及其规律,并优化热场结构。数值模拟结果显示,通过优化散热孔形状、保温棉的结构等设计参数,电阻加热式大尺寸晶体生长系统在晶锭厚度变化、多孔介质原料消耗的情况下均能达到较低的晶体横向温度梯度和较高的纵向温度梯度。0 引 言 碳化硅(SiC)单晶材料具有宽带隙、高临界电场、高热导率、高载流子饱和漂移速度等特点,是重要的第三代半导体材料,适合用作功率/ 射频器件的衬底。根据电学性质不同,碳化硅主要分为导电型和半绝缘型两类。P 型导电的碳化硅是制造 SiC 功率器件的理想衬底材料,但 P 型掺杂技术还不够成熟,由此生长的晶体缺陷多、电阻率高,因此现阶段主要使用 N 型导电碳化硅衬底(电阻率 < 30 mΩ·cm)进行同质外延制造 SiC 功率器件。SiC 基的 MOSFET、肖特基二极管和晶闸管等已被成功用于新能源汽车动力控制、超级充电桩、电力系统和列车牵引等领域。同时,由于 SiC 与 GaN 材料晶格失配度低(3. 4% ;Si 与 GaN 为16. 9% ),半绝缘型碳化硅(电阻率 > 105 Ω·cm)是异质外延氮化镓薄膜的优良衬底材料,相关的高频大功率微波器件(如 HEMT 等)也已在雷达、5G 通信等领域取得了成功。SiC 基器件相比 Si 基器件具有开关效率高、散热强、能耗低、体积小的特点,被认为可大面积取代 Si 基器件,但碳化硅衬底高成本制造成为目前制约 SiC 器件发展的主要原因之一。加入三代半交流群,加VX:tuoke08。现阶段工业化生长碳化硅晶体主要使用物理气相输运( physical vapor transport, PVT)法,它涉及多相、多组分、多种传热传质输运和磁电热流交互作用的复杂多物理场耦合问题。因此,PVT 生长系统设计难度高,且晶体生长过程中的工艺参数测控较为困难,导致所生长的碳化硅晶体质量如缺陷难以控制,晶体尺寸偏小,从而以 SiC 为衬底的器件成本居高不下。为了降低成本,有必要发展高品质大尺寸 SiC 晶体生长的装备和工艺。目前工业上一般使用中频感应加热的 PVT 生长系统,主要由感应线圈、保温层、坩埚和坩埚装载的 SiC原料与籽晶等要素构成,坩埚侧壁中感应电流产生的焦耳热是主要热源。PVT 法生长 SiC 单晶主要包含:SiC 原料分解生成气相组分、SiC 气相组分在惰性氛围中输运至坩埚顶部的籽晶附近、SiC 气相组分在籽晶上结晶后定向生长三个过程。所生长的晶体形貌和结晶质量受籽晶温度均匀性、气相组分硅碳比、输运气体的流动速度和原料杂质含量等因素影响,其中气相组分的流速、流量和硅碳比值由原料区域的温度梯度、温度大小和原料孔隙率等参数控制。随着晶体直径扩大,坩埚变大,热量从外向内传递所受热阻增大,晶体和原料的中心温度降低所造成的晶体横向温差变大从而导致晶体多型、基平面位错(BPD)甚至开裂等缺陷增多。原料中间区域温度低而侧面温度高造成原料的分解速度中心慢侧面快,使得壁面附近气体流量大,从而导致晶体外缘生长速度加快,甚至产生横向分解与结晶过程。大尺寸晶体生长过程中,原料内温度及分解条件变化巨大,如:原料从周缘开始消耗并生成多孔碳,导致原料内部温度下降(外到内的传热阻力加大),SiC 气相组分流动的驱动力减小,同时原料上部的低温区可能因为粉末烧结或 SiC 气相组分再结晶变得更致密,气流向外流出的流阻又增大,晶体生长可能因此减慢甚至中断。由此可见,原料到晶体的传热及流动设计至关重要。基于均匀绕线距离的感应加热,很难满足原料加热的动态需求,因此有必要重新研究基于电阻加热的加热器设计及系统热设计。近年,Ⅱ-Ⅵ等公司已使用电阻加热式 PVT 系统生长 8 英寸(1 英寸 = 2. 54 cm)及以上碳化硅单晶体。晶体生长在极高温且封闭的设备中进行,由于缺乏直接观测和参数监控手段,计算机数值仿真是研究系统内热力学和动力学的重要手段。美国 CREE、Ⅱ-Ⅵ等公司通过近 15 年的努力,将衬底产品从 2005 年的 4 英寸发展到了现在的 8 英寸 N 型和 6 英寸半绝缘型低缺陷衬底,并正在进一步扩大产能,而国内的相应技术仍处于攻关阶段。本文针对电阻加热 PVT 法生长 8 英寸 SiC 晶体开展热场设计和工艺设计的数值仿真模拟研究。首先建立描述碳化硅的原料受热分解热质输运及其多孔结构演变、能量输运的物理和数学模型,再研究散热孔直径、加热器长度位置、加热温度等生长系统中的重要设参数对热场的影响规律。加入三代半交流群,加VX:tuoke08。最后,根据籽晶面横向温度梯度小、料与生长界面之间纵向温度梯度大的要求,提出 8 英寸晶体生长热场的优化设计方案。1 PVT 法晶体生长过程的热-质输运原理 1. 1 基本物理过程 图 1(a)展示了电阻加热式 PVT 生长系统的主要结构,包括保温层、加热器、坩埚和坩埚内的原料与籽晶,系统呈圆柱轴对称形。与感应加热方式不同,电阻加热以电阻体作热源,并以热辐射为主要传热方式加热坩埚外壁,再通过坩埚导热来加热原料。加热器可布置在坩埚的周围、顶部和底部以实现对局部区域的温控。原料被加热后发生分解,所产生的 SiC 气相组分在温度梯度的驱动下被输运至处于顶部的低温籽晶面再结晶从而形成晶体。对于 PVT 法生长 SiC 晶体,系统中热-质输运及其特点可按三个区域来描述,各区域涉及不同物理问题,如图 1(b)所示。 第一是原料区。原料是晶体生长的气源可以直接影响晶体质量,例如 SiC 原料粉末中常含有杂质 N 元素,会导致半绝缘型晶体的电阻率偏低。原料温度分布是控制晶体生长速率、形貌的主要因素。电阻加热式 PVT 生长系统中,围绕坩埚的侧加热器是主要热源,顶部孔洞是主要散热通道,原料表面与籽晶/晶体表面之间存在较强的辐射换热。因此原料区有明显的横向和纵向温度梯度,即原料周缘区域温度 > 中心区域温度 > 原料表面温度。在这样的温度分布下,且因贴壁区域气流通道更大,外缘的原料消耗速率大,内部原料消耗速率低,如图 2 所示。文献报道[9],原料区域温度梯度与晶体的极限生长速率密切相关,增大原料区域温度梯度可提高晶体生长速率,但温度梯度超过某个阈值则会导致生长速率下降甚至生长中断。温度对原料分解过程的影响会改变晶体生长速率变化,如原料内部温差与原料表面———长晶界面温差的匹配不适造成 SiC 气相组分在原料表面结晶。此外,温度大小影响气相组分中的硅碳比例,当温度在2 800 K左右时,气相的硅碳比达到最优值,且反应产物均为气相,无残留的固相碳;当温度低于 2 800 K时,气相的硅碳比达富硅,大量的原料被石墨化。 第二是坩埚上部空腔区。SiC 气相组分在压力差和浓度差的共同作用下逸出源区,进入充满氩气的坩埚上部空腔形成宏观流动和扩散。 空腔是由晶体生长界面、坩埚壁面和原料表面所构成的封闭空间,能量在此空间中以辐射和对流的形式进行输运。 若采用石墨坩埚,气体会与坩埚壁面发生反应,从而改变气相中硅碳元素之比。第三是籽晶区。SiC 气相组分输运至较冷的籽晶面,改变了此处的热力学平衡状态,过饱和的气相沉积,即实现了晶体生长。 籽晶区的温度均匀性十分重要,它不仅控制晶体界面生长速率,也影响微管、位错等缺陷密度大小。气氛中的硅碳比是影响 SiC 晶体生长的重要因素。 晶体生长气氛需要一定程度的富硅,而富碳会导致晶体的碳夹杂增多。 使用 PVT 法生长 SiC 晶体的初期,由于原料在被消耗的初始阶段,生成的碳较少,气氛呈现富硅。SiC 气相成分一方面被多孔介质阻碍流动,另一方面会在低温料的表面沉积,此时晶体生长速率较低。随时间推移,壁面附近的原料被消耗后呈石墨化状态(见图 2),固相碳含量增多,气相中的硅碳比下降。该阶段中因为料顶部被消耗,气流通道慢慢打开,更多的气相组分达到籽晶附近,晶体生长速率逐渐变大。到了中后期,由于原料一直处于高温环境,部分碳化硅料烧结生成多孔的碳化硅陶瓷,同时由于更多的原料被消耗,形成多孔碳。这个过程会影响分解反应的平衡,抑制富硅气相生成导致气氛转为富碳。因此,PVT 法晶体生长过程的核心物理问题是热力学过程及热-质输运过程,需要建立合理的物理和数学模型。1. 2 热力学过程 坩埚内的气相组分主要有 Si、SiC、Si2C 和SiC2等,以及微量C3离子、C2 、C 和Si2等。这些含碳、硅元素的气相组分一方面源自碳化硅的原料分解所生成的气体产物,另一方面来自原料分解的气体产物与石墨坩埚中的碳反应产物,总体构成了碳-硅二元素系统,该系统的组分构成主要受环境温度的影响。Lilov用热力学分析手段分别得到了 Si、SiC、Si2C 和SiC2等气相组分在不同温度下热力学平衡状态下的分压。原料分解涉及的主要可逆化学反应包含:

 从表中数据可知,当温度低于 2 546 K 时,反应(b)和反应(c)中的 Si 蒸汽平衡分压低于 Si 饱和蒸气压,因此硅元素主要以气相存在,系统内为富硅蒸汽环境,且主要由反应( b)控制。当温度大于 2 546 K 小于2 900 K时,反应(b)和反应(c)中的 Si 蒸汽平衡分压低于 Si 饱和蒸气压,但反应(b)的 ,因此在该温度区间里,Si 蒸汽分压由反应(c)控制。当温度高于 2 900 K 时,反应(c)中的 Si 蒸汽平衡分压高于 Si 的饱和蒸气压,因此一部分生成物以凝聚态液相存在。生长碳化硅晶体需要 C 元素,籽晶附近的 C 含量处于较低水平,而 SiC 蒸汽在工艺温度下分压很小,因此主要考虑SiC2 、Si2C 和 Si 组分的作用,即晶体生长速率由反应(c)和反应(d)控制。若假设晶体以理想计量比生长,则控制组分的摩尔通量需满足 JSiC2= JSi2C JSi,且温度低于 2 900 K 时,SiC2的平衡分压大于Si2C的分压,环境组分主要由反应(c)控制。因此,忽略掺杂源,系统气相可简化为晶体生长控制组分SiC2 、Si 和载气(如氩气等)构成的单相体系。1. 3 传热传质过程的物理和数学描述和分析 PVT 法生长碳化硅晶体需要大于 2 000 ℃的温度环境,本文所研究电阻加热生长系统中,加热器的能量通过热辐射、热传导等方式传递给碳化硅原料,原料分解生成的气相组分在温差、压差和浓度差的驱动下形成流动和扩散,被输运至籽晶面(或晶体生长界面)以及生长腔内的各个位置,因此传热模式包含传导、对流和辐射三种。另外原料和晶体生长会吸热和放热,这些机制相互耦合,最终使系统温度维持在稳定的范围内。为了解各种热传递模式的强度,首先分析传热量的量级,之后对生长系统开展数值仿真模拟预测温度场等分布的研究。1. 3. 1 传热方式量级分析 晶体生长系统内的温度一般在 2 000 ℃以上,近电阻加热器的区域温度最高,因此辐射是热传递的主要方式。电阻加热式生长系统的辐射传热主要存在于三个区域:(1)坩埚内生长室内的壁面、籽晶面和原料堆表面之间;(2)石墨加热器外壁、坩埚外壁和保温棉内壁之间;(3)保温棉外壁到不锈钢外壳之间。坩埚上部空腔中原料表面到籽晶面的辐射热量可用下式近似估算:同理估算电阻加热器外壁对坩埚外壁之间的辐射热量:  保温棉外壁温度一般低于 700 ℃ ,热辐射相对较弱,但也可按下式估算其热量的量级: 坩埚内气相组分流动的热输运强度可用无量纲量瑞利数表征。瑞利数 Ra(Rayleigh number)是普朗特数 Pr(Prandtl number)与格拉晓夫数 Gr(Grashof number)之积,用于衡量热传导和热对流相对强弱,也可用于判断自然对流强度。一般认为 Ra > 105时,热对流占主导,Ra > 1 707 时,封闭空间中开始产生自然对流(贝纳德对流)。瑞利数 Ra 表达式如下: PVT 法生长 SiC 晶体主要经历两个过程,也即碳化硅原料受热分解成多种气体组分和气体组分在籽晶面结晶并定向生长。实际上这两个过程存在较为复杂的表面化学反应,可近似认为是相变。因此可用下式估算原料表面和长晶界面上由于化学反应所引起的热量变化:
计算使用的参数如表 2 所示。 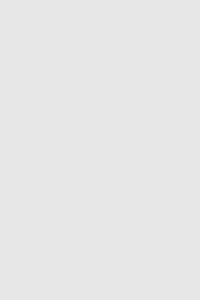 在典型工况条件下, 电阻加热器温度 2 280 ℃ ,坩埚外壁温度 2 275 ℃ ,保温棉外壁 60 ℃ ,环境温度30 ℃ ,籽晶面温度 2 200 ℃ ,原料表面 2 235 ℃ ,籽晶与原料表面相距 0. 054 m,环境压强 2 kPa,晶体生长速率 Gcrystal≈0. 4 mm / h。联立求解方程(2) ~ (6),获得 Ra = 78( < 1 707),说明对流引起的热传递小,自然对流强度小,均可忽略。坩埚内空腔的辐射热量 Qradi_cham = 1 094 W,加热器对坩埚外壁的辐射热量 Qradi_heat =2 281 W,保温棉外壁对外界辐射热量 Qinsu = 692 W,相变热 Qchem = 0. 1 W。由此可知, 能量输运主要受加热器对坩埚外壁、原料表面对籽晶面的辐射传热控制。1. 3. 2 输运方程 根据 1. 1 节的物理过程分别建立输运方程。由 1. 3. 1 节传热方式量级分析可知,能量方程主要考虑热辐射和热传导,且本文主要研究热场设计,因此忽略流动计算。原料部分的构成是多孔体结构,其物理过程复杂,涉及辐射传热、固相导热、相变以及原料消耗后使孔隙率变化从而改变气相流动。从系统热场的计算准确性来讲,将原料部分简化为宏观多孔介质是合理的,因此基于多孔介质模型来建立该部分的输运数学模型。假设: (1)原料为大小一致、直径 1 mm 的球形颗粒; (2)原料固相密度不变; (3)原料颗粒处于局部热力学平衡状态; (4)颗粒间的辐射传热用等效传热系数计算; (5)SiC 气相组分中硅碳原子数为理想 1∶1 化学配比。 则该区域的能量守恒方程可表示成: 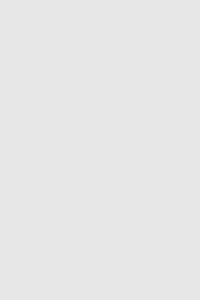
式中: (ρcp )eff 是原料颗粒的等效热容。 考虑多孔介质内存在固相和气相,等效热容可按下式得到: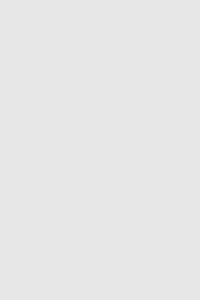
式中: εp 为原料颗粒的孔隙率, ρcp是热容,下标 SiC 和 gas 分别代表原料颗粒和气相。 类似,等效热导率 keff需考虑孔隙内的热辐射和固相热传导,用下式计算: 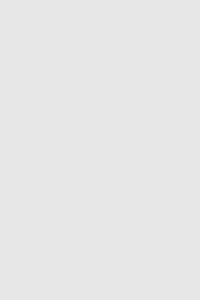 式中:k 为热导率,下标 SiC 和 gas 分别代表原料颗粒和气相; 另外,由于固体消耗导致原料中的孔隙率增大,孔隙率的变化一方面能反映料的消耗情况,另一方面孔隙率会影响料的导热性能和气相组分的流动,因此也需要考虑孔隙的演变情况,通过质量守恒可得孔隙率演变方程(10): 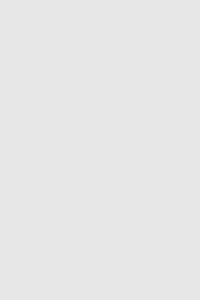
由于假设 SiC 气相组分中硅碳原子数一致,各组分的摩尔通量需满足 JSiC2= JSi2C JSi,即总的气流摩尔通量 JA = 2JSiC2,因此为简化计算,可令 R= 2RSiC2,并由式(11)进行计算: 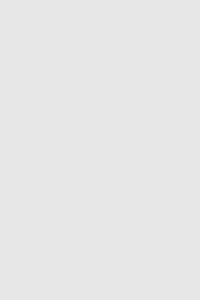
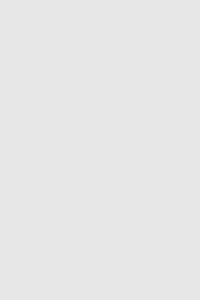 对坩埚的空腔区域,主要考虑导热和壁面之间的辐射,能量方程如下: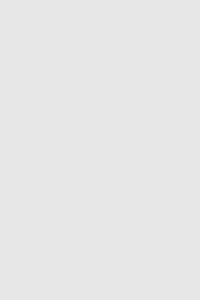 对于辐射计算,可将所有固相物质视作不透明物体。假设所有参与辐射的壁面均为漫灰表面,采用面对面辐射模型,辐射热流 q″radi以第二类边界条件的形式参与计算,每若干个迭代步更新一次辐射在内边界上的热流,因此需要计算每个参与辐射壁面上的净辐射热流密度。对于参与辐射的表面,净辐射热流密度 q 可用相应参与辐射表面温度计算获得:式中: δij 是 Kronecker delta; Fij 为视角系数,表示从 j 面发射的能量被 i 面拦截的份额,用式(15)计算: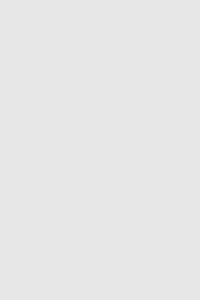
本文算例的计算域均为轴对称,半径约 500 mm,高约 1 400 mm,采用商业软件ICEM 对计算域划分非结构网格,网格尺度为 1 mm。采用 Fluent 对方程进行离散和求解,对称轴边界条件为温度零梯度,其余外边界为 320 K 定温。 2 大尺寸 SiC 晶体生长系统热场设计 本节讨论基于数值模拟方法开展电阻加热式 8 英寸晶体生长系统的热场设计研究,提出热场设计准则,探究结构参数如散热孔径、加热器温度和加热器尺寸等对热场的影响规律,并基于影响规律,围绕保持良好的籽晶横向温度均匀性和大纵向温度梯度的要求,给出结构和工艺优化设计。 2. 1 热场设计准则 热场设计主要从以下 5 个方面考虑。(1)如何满足晶体或籽晶面横向温度均匀性要求,即径向温度梯度合理且恒定。(2)原料与籽晶面之间的纵向温度梯度要合理,不能过小或过大。(3)原料区域容易出现再结晶或烧结形成硬质陶瓷,为了保证提供晶体生长所需的气流量,需要优化原料内的温度梯度。(4)由于更高的料外侧温度使其最先被消耗,造成坩埚壁面附近气流量增大,有利于晶体边缘快速形成多晶,避免这种情况发生需设计导流结构。(5)随着晶体的增厚和料的消耗,温度会出现波动,对 8 英寸晶体生长系统而言,波动会更大,热场设计需要考虑在不同阶段实现动态可控或自适应调整保证系统的温度场稳定。实验表明,较低的籽晶面横向温度梯度可有效改善晶体生长形状,纵向温度梯度则直接控制晶体生长速率,满足这两个要求是热场设计的首要需求,因此下文将围绕籽晶面横向温度均匀性和纵向温度梯度阐述热场设计。2. 2 热场结构设计参数研究 系统尺寸扩大,结构参数对晶体生长热场影响发生变化,有必要先探究结构设计对温度的影响规律。本节研究的几何模型基于小尺寸系统放大,坩埚内径为 200 mm,如图 3 所示。对坩埚而言,加热器参数控制热源,散热孔参数控制冷源,因此选择顶部散热孔直径、底部加热器温度和侧面加热器长度作为研究变量。顶部散热孔直径基础值 D0 = 60 mm,底部加热器基础温度 T0 = 2 238 ℃ ,侧加热器基础长度 L0 = 420 mm,采用单一控制变量法进行研究,设置 4 组算例,其中算例 1 为对照基础,算例 2 ~ 4 分别研究不同设计参数的改变对坩埚内温度分布的影响,具体参数设置见表 3,几何参数变化范围见图 3 中虚线框域。计算结果重点考察籽晶面横向温度梯度、原料表面与籽晶面之间的纵向温度梯度,如图 3 所示,同时观察原料区域内最大温差变化情况。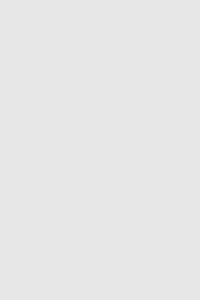 图 3 生长系统结构和设计变量说明,顶部散热孔径 D 变化范围是 0. 25D0至 D0 ,侧加热器长度 L 变化范围是 0. 6 L0 至 L0 ;坩埚内特征位置:籽晶面中心点 A、籽晶边缘点 B,原料表面中心点 C 和原料侧下方区域 E。籽晶面横向温度梯度等于(TB - TA ) / LAB , 原料与籽晶表面纵向温度梯度等于(TC - TA ) / LAC 。原料最高温度位置可能在 E 区内移动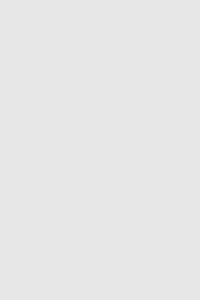 图 4(a)所示是基础算例 1 坩埚内温度分布。籽晶中心和边缘温度分别是 2 495 K 和 2 510 K,温差约15. 2 K,温度梯度 1. 52 K/ cm。原料表面中心的温度是 2 506 K,纵向温度梯度 1. 2 K/ cm。原料最高温度是2 548 K 在侧下方。图 4(b)是籽晶面横向温度分布与原料-籽晶表面纵向温度分布(实线),可看出,从籽晶面中心到边缘(对应图 3 中 A 至 B 点),温度逐渐升高,但斜率有波动;从原料表面中心到籽晶面中心(对应图 3 中 C 至 A 点),温度逐渐下降,且斜率不断减小。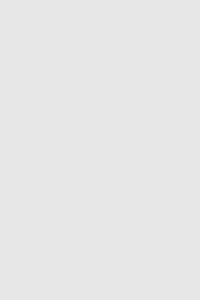
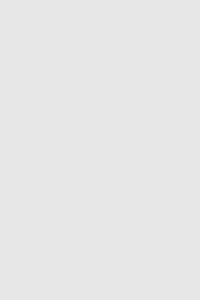 图 5 显示算例 2 ~ 4 籽晶面横向温度梯度和籽晶-原料表面纵向温度梯度随设计参数顶部散热孔直径、侧加热器长度、底部加热器温度等变化趋势。其中虚线、实线和点划线分别代表籽晶面横向温度梯度、籽晶-原料表面纵向温度梯度和原料内最大温差。表 4 汇总算例 1 ~ 4 横、纵向温度梯度等参量变化。从图 5(a)可见,顶部散热孔直径缩小,横向和纵向温度梯度同时降低。散热孔径缩小 50% 和 75% 时,籽晶面横向温度梯度分别降低 62% 和 87% ,纵向温度梯度分别降低 40% 和 66% 。较小的散热孔径有利于坩埚顶部均匀散热,横向温度梯度降低,但坩埚向外界的辐射散热也因此减弱,无法建立大纵向温度梯度。从图 5(b)可见,侧加热器长度变短籽晶面横向温度梯度降低,而纵向温度梯度略微提高,当侧加热器长度缩短 25% 和 40%时,籽晶面横向温度梯度分别降低 26% 和 47% ,纵向温度梯度分别升高 8% 和 11% 。侧面加热器是主要热源,它越长对坩埚上部的空腔和籽晶外缘加热越强,导致籽晶面横向温度梯度升高。适当调整侧加热器长度,使其减少对籽晶区域直接加热同时可充分加热原料,从而获得低横向温度梯度和高纵向温度梯度。从图 5(c)可见,底部加热器温度越高,原料内温差越大。当底部加热器提高 30 K,原料温差增加 35 K。但底部加热器温度变化对坩埚上部区域的温度场影响小,籽晶面横向温度梯度、籽晶-原料表面纵向温度梯度几乎不变。顶部散热孔直径对横向和纵向温度梯度的影响趋势相同,侧面加热器长度的影响却相反,因此要合理设计散热孔和侧加热器结构参数,扬长避短。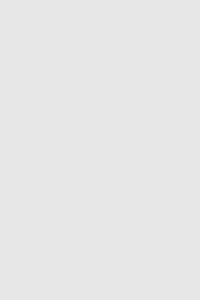
2. 3 热场优化和工艺设计 为提高籽晶面横向温度均匀性、增大籽晶-原料纵向温度梯度,根据上节的研究结果,对顶部散热孔和侧面加热结构进行优化设计。2. 3. 1 结构优化 考虑生长 8 英寸晶体的坩埚其顶部散热孔的直径需要扩大,但中部单孔扩径容易造成晶体中部过冷、横向温度梯过大、纵向温度梯度不均匀等一系列问题,因此当前的中部开口方式,很难产生合适的顶部温度分布。为提高晶体横向温度均匀性,可设计环形位置上多个偏心散热孔,并通过坩埚盖、均热板、黑腔等设计来调平晶体横向温度梯度及调平生长界面。只保留侧加热器并适当下移,在坩埚中部增加保温凸肩、底部设计保温隔板,削弱对籽晶外缘加热并减少热量在底部的耗散,使能量从原料区充分进入坩埚,形成自下而上的热流,同时适当缩短原料上表面与籽晶面的距离,从而提高坩埚内纵向温度梯度。纵向距离的缩短可能导致气流不均匀,需视情况设计导流结构,本文暂不考虑该影响。优化后生长系统见图 6,坩埚内径 ϕ210 mm,加热功率 8 ~ 10 kW,籽晶台高 10 mm。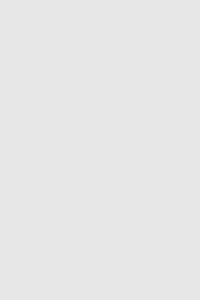
2. 3. 2 工艺优化设计 本节对工艺过程中的典型状态进行仿真,设置三组算例,先通过算例 5 检验优化方案下,未长晶体时的坩埚内温场分布,再通过算例 6 对不同晶体厚度的典型工况进行分析,最后通过算例 7 研究原料消耗对优化方案系统热场的影响,算例说明见表 5。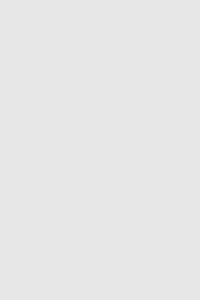 数值模拟得到算例 5、算例 6 的坩埚内温度分布如图 7 所示。籽晶面横向温度分布均匀,籽晶-原料表面纵向温度梯度较大。晶体厚度为 20 mm 和 30 mm 时,生长界面的横向温度分布均匀,温度值略有升高,原料温度分布状态保持稳定。晶体厚度增大,料与籽晶面温差变化较小,因此纵向温度梯度随两者距离缩短而增加。图 8 展示了优化方案下晶体厚度为 0、10 mm、20 mm、30 mm 时,及优化前(算例 1)系统的籽晶面横向温度分布和原料-籽晶表面纵向温度分布。从图中曲线变化趋势可知:优化后晶体生长界面横向温度均匀性好,温度梯度小;纵向温度分布均匀,温度梯度大。相比优化前(算例 1,双点划线),优化后籽晶面横向温度更均匀,纵向温度梯度更大。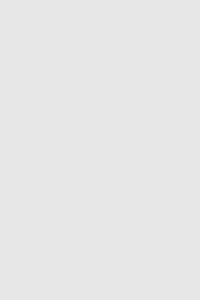
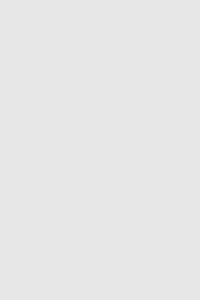 图 9 中原料孔隙率的变化反映了料的消耗情况。近壁面区域的料消耗速率高,底部消耗速率低,与文献报道的实验结果符合。坩埚内温度较高,辐射传热占主导,原料孔隙率变大使原料等效热导率提高,图 10(a)显示原料区平均温度和籽晶面平均温度随时间不断升高。图 10(b)、(c)显示在 0 h、27 h 和 54 h三个典型时刻,长晶界面横向温度变化小,分布均匀;原料表面与晶体表面温差保持在 40 K 左右,纵向温度梯度随晶体增厚而增加。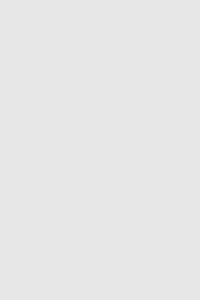
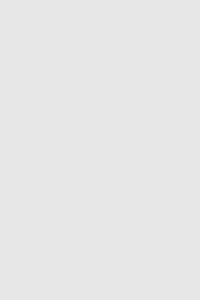 算例 5 ~ 7 的热场参量变化如表 6 所示。优化方案下的籽晶面横向温度梯度相比算例 1 中降低 81. 3% ,原料与籽晶面间的纵向温度梯度增加 509% 。晶体厚度变化时,晶体表面横向温度梯度稳定在 0. 25 ~0. 28 K/ cm范围内,原料与晶体表面温差稳定在 36 ~ 38 K 范围内,纵向温度梯度随晶体厚度的增加从 6. 7 K/ cm 增大至14. 2 K/ cm。原料消耗使孔隙率变大,原料的等效热导系数随之增大,致使原料内最大温差从 90 K 降至40 K,原料表面和籽晶面温度提高 40 K;晶体表面横向温度梯度稳定在 0. 27 K/ cm 左右,纵向温度梯度随晶体厚度的增加从6. 7 K/ cm 增大至10. 5 K/ cm,增幅53. 7% 。总体来讲,优化后的生长系统内温度分布合理,实现了晶体横向温度梯度小、料与晶体表面温度梯度大等主要设计目标,但料内温度梯度较高,气流可能不均匀,后续研究可考虑设计原料形状或导流结构来控制气流。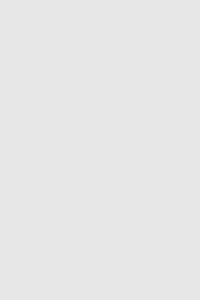
3 结 论 电阻加热式 PVT 生长系统中,侧加热器是主要热源,其长度过长会降低原料表面与籽晶表面温差,过短则可能无法充分加热原料,系统顶部散热/ 测温孔是主要散热通道,其孔径越小,晶体横向温度梯度越低,但无法建立大的原料与籽晶间温差。8 英寸碳化硅晶体生长要求较小的晶体横向温度梯度、较大的纵向温度梯度。优化方案的数值模拟结果表明,环形散热孔、顶部黑腔和保温隔断等结构可使籽晶面在不同晶体厚度情况下均能保持较低的横向温度梯度,同时用较低的加热功率实现了较大的纵向温度梯度。在忽略原料石墨化的情况下,随着原料的消耗,坩埚内温度明显升高,因此在设计热场时需要对全过程进行考虑,例如实时检测系统温度来调整加热器功率。大尺寸晶体生长的热场对细节要求较高,电阻加热方式有利于系统热场的灵活设计,系统局部设计也应作为研究重点方向。
|