1. 焊装生产线概述 车身是构成汽车的主要组成部分,车身制造技术也是现代汽车工业的重要组成部分,车身制造水平的优劣直接体现了一个国家汽车工业的水平。自1913年福特汽车公司采用“流水线”生产方式以来,汽车生产线在汽车工业中占据了极其重要的地位,它对提高生产效率,降低汽车成本起到了至关重要的作用,在大规模生产方式下居于核心地位。 汽车白车身焊装生产线是把各车身冲压零件装配焊接成白车身的全部成形工位的总称,它通常包含发动机舱、侧围、地板及车顶顶盖等焊接分总成线及最后合装主焊生产线。根据生产节拍、自动化程度及生产方式等不同,主焊线及分总成线又划分为若干工位,各工位通过各种类型输送装置连接为一体,每一工位负责完成一部分工作。单工位一般由连接设备、焊装夹具、传输装置等几部分组成(见图1)。  图1 焊装总拼工位
1.传输装置 2.焊接设备 3.车身焊装夹具 2 . 焊装生产线问题 (1)工位故障率问题 每条白车身焊装流水线由若干工位组成,而每个工位完成车身的一道或几道工艺,因此每个工位由若干设备组成,如图1所示。此工位为主焊接线的一个重要工艺工位,其工艺流程为:车身由升降传输辊床运输到工位内部,到位之后,由车身焊接定位夹具将车身侧围、顶盖横梁和车体主结构定位夹紧,然后机器人抓取点焊焊枪对于车身进行点焊焊接。焊接结束之后,夹具打开,车身再由升降辊床运输到下一个工位。整个工位的设备组成:机器人+点焊焊枪7台;左右侧围定位车身焊接夹具两台;升降辊床传输装置1台。 单台设备对应的平均故障间隔时间,平均修复间隔时间,以及可利用率参数如表1所示。 
以上这些设备构成了一个可修复系统。虽然这些设备都是独立不相关,发生故障的概率也没有联系,但是当其中任何一个设备发生故障时,整个系统将要停机用于修复,所以为了保障整条生产线效率,不仅在设计过程中就要为此工位留出修复的时间,同时在生产过程中,还要安排维修人员进行维护和及时修复。 (2)暂存区域问题 白车身焊装车间最主要的问题在于每条生产线中,设备随机的故障而导致的停产,比如焊接设备中的机器人故障、车身焊装夹具中气缸的故障,传输装置中升降传输辊床故障,这些设备造成整条生产线停产而导致线效率的下降。为了避免整个生产系统全部停产瘫痪,在关键工位之间、每条线体之间增加暂存区域,这样可以有效地降低部分系统产生问题对于整个系统的影响。因此,每个生产系统之间,例如地板总线和主焊接线之间就要设置暂存区域,但地板总线因故障而导致停产时,主焊接线还是利用暂存区域里的储备物料进行生产。 但是暂存区域的数目以及每个暂存区域的容量也不是越大越好,它会造成以下几点问题:①暂存区域会造成投资成本、生产运营成本、维修成本上升。②暂存区域会占用生产工位的操作空间。③暂存区域没有生产活动,会产生空闲时间,并且在生产预热过程中,需要填满所有的这些暂存区域才能使得生产系统工作,从而导致整体的生产效率下降。 所以,焊装车间的设计以及布置的目标之一就是最小化暂存区域。 (3)生产时间变动影响 在高度自动化的白车身焊装车间,每个工位,每条生产线的期望的生产节拍是恒定的,但是这是无法满足的。假定生产安排JPH=60,设计要求的生产线效率为85%,那么生产节拍为: 
因此每个工位、每条生产线的节拍要求都不能超过Tmax=51s,否则就会产生瓶颈工位。另外,在不超过指定节拍前提下,要求生产活动尽量用足指定节拍,从而减少生产设备、工位以及操作工人。另外一个与节拍相关的目标是尽量均衡每个工位之间的生产时间。当每个工位之间生产时间都均衡的条件下,也可以降低暂存区的数目。 (4)焊装生产线目标函数 综上所述,白车身焊装生产线是一个多目标优化问题,需要考虑的目标包含:①最小化暂存区容量。②最大化每个工位生产时间。③最小化每个工位生产时间之间的差异。④生产必须满足JPH要求,从而满足每天N辆车的目标。 但是上述设定目标和现实之间还有冲突,例如,由于每个设备存在着不同的可利用率,上述第3项就和生产时间最大满足节拍要求冲突。因为可利用率是一个随机的波动值,如果不留余量的话很容易造成瓶颈工位。 3. 车身总拼线建模分析 (1)仿真平台 Tecnomatix公司的数字化工厂软件Plant Simulation是一款完全采用面向对象方法的仿真软件,它构建了一个完整的工厂,从生产线、加工单元到工序操作的所有层次进行设计、物流仿真和优化的集成计算机环境。面向白车身的解决方案主要解决白车身焊装生产线的工艺规划、焊装生产线的布局等问题,同时应用物流仿真模块对整个生产线进行物流分析和优化。 (2)实例车身仿真模拟 某工厂建立的焊装车间,规划设计的产能是JPH=60,进行车间生产线的平面布置和设备的选取。每条生产线根据工艺需求分为若干工位,如图2所示,其焊装主线由13个工位串联组成,焊接车身地板总成和侧围内板以及顶盖横梁。  图2 车身主线
注:①为Afo4100 Lifter,②为Afo4110 Manual sealling,③为Afo4120 Manual Loading & Tab,④为Afo4130 Manual Loading & Tab,⑤为Afo4135,⑥为Afo4140 Framing inner Geo,⑦为Afo4150 Auto Re-spot,⑧为Afo4160 Auto Re-spot,⑨Afo4170 Auto Re-spot,⑩为Afo4175 Auto Re-spot,⑪为Afo4180 Man Repair,⑫为Afo4185 Inline Measuring,⑬为Afo4190 Lifter。 焊装主线上每个工位的可利用率、失效间隔平均时间、维修间隔平均时间,具体参数如表2所示。 
从数据上分析,4140工位的可利用率相对较低,并且MTBF间隔时间最短,因此4140为瓶颈工位,那么从Plant Simulation环境下对其进行建模仿真研究,并且验证解决方案对于提升生产线效率的有效性。 将4140工位和4130、4150工位串联起来组成一个分系统,建立仿真模型,根据表3输入参数(见图3)。  图3
经过系统的仿真,输出这个分系统的效率为96.08%。从理论上而言,如果是独立系统的效率达到96.08%的话,这个系统的生产率还是很高的,也不用产生额外的成本去优化处理。但这个分系统只是串联系统中的一部分,所以对于这个分系统的优化还是必要的。 优化方法一:改变部分工艺顺序,缩短4140工位实际的加工活动时间,将原本51s的加工时间缩短至49s,仿真结果如图4所示。  图4 4140瓶颈工位优化仿真一
通过优化仿真,分系统的生产效率提升至96.28%,相对原来系统生产率提升了0.2%。 优化方法二:在瓶颈工位4140前后增加暂存工位,各增加两个串联的暂存工位,仿真结果如图5所示。  图5 4140瓶颈工位优化仿真二
通过优化仿真,分系统的生产效率提升至96.34%,相对原来系统生产率提升了0.26%。 优化方法三:在生产线上增加一个并联的4140工位,由于生产线的节拍保持51s不变,理论上单个4140工位生产节拍可以做到102s,但为了防止可利用率的波动造成效率影响,将单个4140工位生产节拍提升到90s,仿真结果如图6所示。  图6 4140瓶颈工位优化仿真三
通过优化仿真,分系统的生产效率提升至96.72%,相对原来系统生产率提升了0.64%。 综合上述三种优化方法,生产线效率的提升随着方法是递增的,但是同时加工成本也是随着方法递增的。在实际的生产活动中,必须综合考虑各方面的因素而选择布置操作工位,解决瓶颈工位的问题。 (3)生产线仿真模拟 根据表3建立主线1的模型,如图7所示,通过仿真模拟,整条生产线的效率为91.96%,满足规划设计85%的设计要求。 从仿真结果来看,工位4100,4135(暂存工位)产生空闲时间,可以安排工作内容,以均衡整条生产线之间每个工位生产节拍;另外,工位4140、4150为瓶颈工位,规划设计以及实际生产活动中,都应该着重提高这两个工位的效率,避免瓶颈的出现。  图7 主线1仿真模型
4. 结语 白车身焊装生产线系统是一种典型的离散系统,受随机因素影响较大,离散系统仿真算法较多,其中面向对象的仿真方法更符合生产线的实际情况。Plant Simulation具有丰富的建模单元,能够模拟生产系统中的各种加工单元,再加上软件本身强大的实验分析、遗传算法等功能,可清楚地看出系统的瓶颈所在,并且结合生产经验仿真解决措施,从而提升生产线效率。 该研究对于汽车生产企业的生产线效率提升具有较强的参考价值。 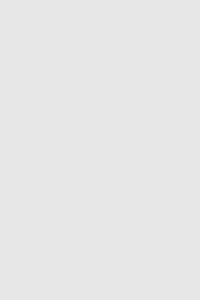
本文刊登于《金属加工(热加工)》2012年22期
|