
摘要:针对GZQC33离合器壳体在压铸生产过程中出现的烧伤、粘模缺陷和生产效率低等情况,进行原因分析,找出原压铸工艺存在的问题,并提出采用三维打印模具镶件的方案,对离合器壳体工艺进行改进。应用模流分析软件对改进的工艺进行模拟仿真,并进行批量生产验证,离合器壳体的废品率由原压铸工艺的9.76%降低至改进工艺的0.89%,生产能力提高28%。 汽车离合器壳体铝合金压铸件如图1所示。产品尺寸为550mm×395mm×230mm,质量为10.2kg,使用2500t压铸机生产,年需求量为12万件。图示位置为油道区,共有七条油道,作用为驱动拨叉改变挡位。油道工作压力为2.5MPa,试漏条件为300kPa气压下泄漏量小于8mL/min。 在离合器壳体生产初期,压铸不良率约为7.8%,主要缺陷为铸件表面烧伤、粘膜等。客户端机加工废品率为9.76%,主要问题为油道漏气及加工面气孔。压铸生产节拍为126s,理论班产能为185件,剔除废品和处理故障后,日平均产能为400件。客户需求为每天420件,供货压力非常大。 笔者使用三维打印工艺制作模具镶件,实现随型冷却水道,提高冷却效果,可以从根本上解决铸件表面烧伤、粘模等压铸缺陷,降低废品率,提高生产效率。 离合器壳体油道多,因为角度等结构问题,不适宜铸造预铸孔。为了确保油道内部质量,内浇道设计时尽量安排在油道附近,缩短铝液填充路径,提高填充质量。在油道区增加挤压销,进行二次增压,进一步改善产品内部质量。产品浇铸系统如图2所示。 内浇道离油道区域很近,高速高温的铝液对模具冲刷严重,容易造成烧伤粘模等压铸缺陷。为了控制模具温度,降低产品烧伤,根据产品结构增加点冷布置。动模点冷如图3所示。 压铸工艺参数对铸件质量非常重要,其中,模具温度对油道区内部质量影响最大,因此控制模具温度是保证产品内部质量的前提。为了控制好产品质量,需要将影响模具温度和内部质量的压铸参数列入重点压铸工艺参数,见表1。
试制过程中发现,油道区域减料槽处容易出现烧伤缺陷,如图4所示。
产品加工油道后,烧伤位置产生泄漏,如图5所示。
 模具温度对铸件内部质量影响非常大,当模具温度过低时,模具与铝液温差过大,影响铝液流动性,产品内部容易缩松。当模具温度过高时,高温铝液注入模具,温度迅速上升,而点冷冷却速度却缓慢,导致铸件表面烧伤。经调查发现,产品油道区深腔处模具存在孤岛,经高速铝液冲刷后,模具温度很高,冷却散热量不足,由此造成烧伤粘模,影响产品质量。 传统点冷冷却通道如图6所示。传统点冷冷却通道只能采用深孔,进水孔直径受模具结构限制,运水能力有限。冷却水进口和出口只能在同一侧,并且离模具面一般为5mm,由此降低导热效果,难以控制产品烧伤。 三维打印模具镶件的冷却通道如图7所示。可以依据产品形状和壁厚,设计模具型芯内部三维随型冷却水道,确保水道中心至模具表面距离相等,精准控制模具温度。  应用模流分析软件,对采用三维打印模具镶件按调整后压铸工艺参数进行填充模拟,对铝液填充温度和速度进行跟踪分析,分别如图8、图9所示。调整后压铸工艺参数见表2。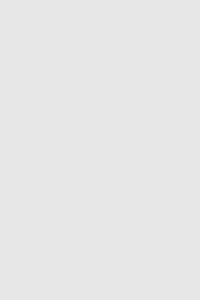
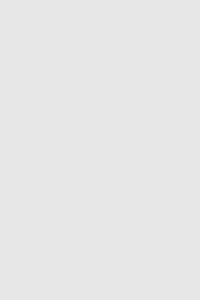 模流分析结果表明,铝液填充按顺序没有包卷,温度分布比较均匀,温度梯度不明显,油道深坑区域温度得到控制。 采用三维打印模具镶件后,模具投入压铸生产,产品深腔处烧伤问题得到解决,产品表面平整光洁。使用三维打印模具镶件冷却与传统点冷产品表面质量对比如图10所示。模具烧伤故障处理时间由每班次60min缩短至每班次20min,压铸节拍由每件126s变为每件110s。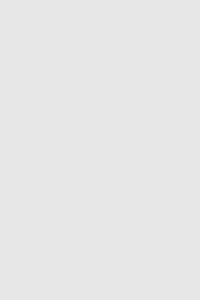 采取改进后的三维打印模具镶件工艺进行小批量试生产,铸件表面烧伤、粘模缺陷明显减少,光滑平整,外观质量明显提升。将调试后的GZQC33离合器壳体50件发送至客户端进行加工验证,50件离合器壳体加工全部合格。批量生产后,进行工艺改进前后铸件废品和班产量数据统计对比,分别见表3、表4。可以看出,铸件的废品率明显降低,班产能明显提高。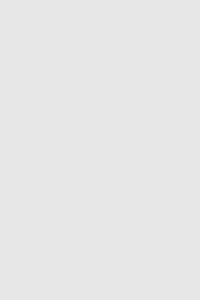
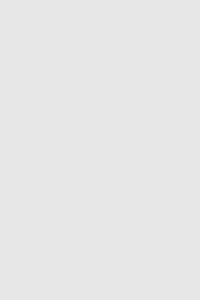 通过对GZQC33离合器壳体原工艺进行分析,找到了产生缺陷和影响生产效率的原因。通过工艺模拟仿真,确定改进工艺方案,并通过批量生产验证了工艺方案的可行性。 采用改进后的三维打印模具镶件工艺生产离合器壳体,废品率由原来的9.76%降低至0.89%,生产能力提高28%。本文作者:广东鸿图科技股份有限公司李振生、汪炜周、张伟炎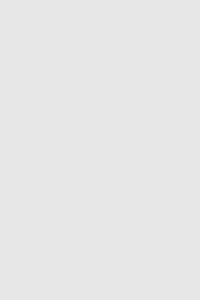
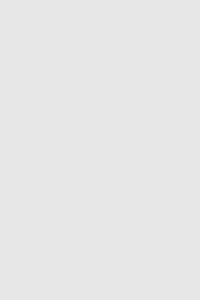
|