转载-蒸汽机模型制作 从6月26日起,开工做一台小型的蒸汽机模型,每天做一点,在这里开个连载做下记录。内容随着进度的前进,会适时刷新。基本上工作日会有更新,双休日工作室不开,俺也休息了。
原始设计来自米国《Popular Science》,在1947年连载了几期。俺结合手头的条件,对其作了一些修改,并修正了原图中不合理的部分
总装以后的效果如图,立式,单缸,双作用式,可换向。缸径1.25吋,冲程1吋,设计转速1500rpm。

原始设计用了若干铸件,因为没有铸造条件,全部改成焊件或者整料直接切削加工出来。
=============================================================== 6月26日 底座 毛坯用槽钢+板材焊接而成。基准面(底面)已经立铣出,导轨安装面(顶面)还未加工。安装螺纹底孔配打。

轴承座安装部分,先在底座体上立铣止口,再铜焊上去。用磷铜焊条+焊药,火焰钎焊。

============================================================ 6月27日 底座继续 铜焊进行的比想象中难,相比起锡焊,铜条不光熔点高,流动性也远不如焊锡。可能还是银焊比较妥当?焊完后喷砂去除熔融的玻璃质焊药。加工完,看到交界面上有裂纹,强度是要大打折扣。希望焊接面大能作为优势,使得两件能保持在一起 焊完再次铣底面作为定位基准,铣顶面,铣轴承座处壁厚到要求。以底面为基准,压板夹紧在工作台上,找正后铣主轴承槽,铣床上打主轴承轴向定位孔,固定螺纹底孔。利用铣床的刻度来打孔,可以得到相当精确的位置

============================================================== 6月28日,主轴承,连杆大头轴承毛坯 两种共三只轴承都是黄铜质的剖分式滑动轴承。其实现在小尺寸的滚动轴承可以轻易买到,不过为了复古起见,还是维持了原来的设计。原来设计的轴承是没有止口的,我在这里加上去了。
两种轴承除了尺寸外,工艺是差不多的。铜料锯下后,先上立铣铣出公母止口,并铣平接触面。各处留切削余量待用。涂焊剂,锡焊成一体以备钻,铰孔。焊得时候发现,这种情形下,配合不宜太紧(我做成轻压入),因为两侧上锡压合的时候,间隙太小很不容易对准。
焊成一体后,再上立铣床,找正装夹。铣与轴承座的配合部分。此处最后一两刀要试切一小段,拿轴承座上的槽来比划一下,再来调整之。

=============================================================== 9月29日,轴承完成,曲轴毛坯制作
铣主轴承各处到尺寸,打轴承下半部分的定位销孔(设计在这里是不完善的,存在过度定位,好在我孔打得很正,没有遇到装配问题),并打安装孔。这里虽然用了铣床上的数字显示,结果有一侧孔还是出现了些偏差,影响螺钉安装。应该是两次打孔中间的一次出了点问题。好在差的不多,改腰形孔。
本来应该一鼓作气攻丝并加工轴承孔的,结果准备好的M2.5丝锥全部忘了带去,工作室里也没有这么小规格的现成货。于是就转而先制作曲轴的毛坯,找了一条钢六方,车直径至0.5吋。此处因为要在经常掉头中保持同轴度,用两顶尖法,结果在工作室里找鸡心夹找了好久,据称已经长久没有人用这个方法了,囧。
到周末了,停止更新两天

============================================================== 7月2日,主轴承配制,飞轮开工
主轴承座孔攻丝。
以底面作基准,在铣床上用90度角板装夹,根据主轴承槽槽壁,用百分表找正到高度方向偏斜1/1000吋以内。分几级钻-扩-铰10毫米主轴承孔。
主轴毛坯上车床,粗,紧车至于主轴承孔成略紧的动配合,余量留作研磨用。
加热熔化焊锡,使得主轴承两半分离。刮清焊锡并测试接触面积。用研磨膏研磨主轴和轴承,到转动灵活。
飞轮毛坯下料(1吋低碳钢板锯出),锯去四角以减小车削加工量。画线,车床上用四爪卡盘找正,粗车轮槽,轮毂至尺寸(现在还夹在车床上,故无图)。

============================================================== 7月3日 飞轮完成
从一块方形的厚板到最后飞轮成形,颇费了点功夫。
先在四爪上车轮槽,再换三爪,用内卡爪卡住轮槽,粗精车轮缘处到直径。其间遇到一点问题,这块板子上曾经有人电焊过,焊点的周围就变成了一个硬点,大大影响车刀的切削。结果在砂轮上将那一处大部磨去以后才得以继续顺利切下去。
车成形以后,钻中心孔,钻-扩-铰轴孔到尺寸。曲轴毛坯继续上车床,车轴向和径向尺寸到要求。实际的配合比我预想中松,可能需要在轴上滚花来解决,待处理。
铣床上用角板装夹,与台面成50度,铣斜面,打顶丝螺孔。M4的顶丝暂时没用,先找了一颗螺钉代替。
本来另一侧的轮槽,外圆和内孔都是在一次装夹里车出的,应当不存在不同轴的问题,结果不然。装上去以后,端面和周向还是有少许跳动,看来轴线是有点歪了。想了想原因,多半是打孔时钻头磨制不当,一刃切削较强,一刃较弱,并且造成的偏斜在后续的扩孔-铰孔中也没有修正过来。看了看原来的文章,作者的工艺是先打轴孔,再用心轴,两顶尖,车外圆和端面,这样可以解决现有的问题,俺不用心轴,直接将装配起来的曲轴毛坯装夹车制,应该也能获得类似的效果,甚至会更好?@玉米加农炮 求建议


============================================================= 7月4日 假期, 停工一天
============================================================= 7月5日 曲拐侧板
从简化加工并容易获得较高精度起见,这个模型的曲轴是四件拼成,分别是轴身一件,曲拐侧板两件,曲拐轴一件。今天做了两个侧板,本来有望全部成功的,结果不幸在配作轴身配合部分的时候错了一个尺寸,直接导致整个轴身要返工从来……大悲剧
两块侧板的工艺是这样的:
-侧板先下料,铣平到厚度尺寸,并铣齐两边。 -在将要切去的部分,一块打螺纹通孔,另外一块打螺纹底孔并攻M3丝,用螺钉将两件连成一体以便得到准确尺寸。 -铣床上钻-扩-铰3/8和7/16吋两孔,并找出配重块部分的轮廓,浅浅铣一刀做记号。 -取下后在7/16吋孔中压入心轴,上回转工作台浅浅切出飞轮外圆尺寸,做记号。 -带锯机上根据切成的外圆锯去多余部分,砂轮上修整成接近圆形。 -心轴用两顶尖装夹在车床上,车外圆到尺寸。 -带锯锯去侧板减重部分,铣床上铣到尺寸。
本来轴身上的与侧板配合的轴颈部分,是要车到成过盈配合的,结果一时智障,读错了刻度,等切下去发现太小的时候,已经悔之晚矣。长度虽然不大,但是破坏了重要的轴向定位尺寸,为了完美起见,决定另作一根。现在正在进行中

============================================================= 7月6日 曲轴装配
曲轴总算有个模样了,先车与侧板配合的轴颈到尺寸,用细锉+砂纸略微修出锥度,同时打光表面。涂油后用手压机压入。压第二块侧板的时候,要留意对齐另一孔。俺是用相应尺寸的心轴来对齐的。压好侧板后压拐轴,也是修成小锥度,先用软锤打入,再用压力机压紧。压成后在轴毂连接处打销孔,砸进销子,在车床和砂带机上修整端面并倒角。下一步是切去轴身的中间间隔部分,并修整之。整根轴成功与否,事实上寄于切断后两段能够保持同轴。
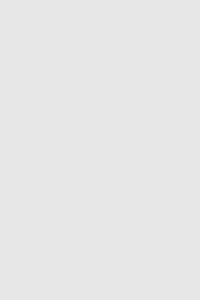
============================================================== 7月11日 连杆毛坯制作
原始设计,连杆用5矩形钢条,车制后烧红扭转90度。因为缺少相应的条件,改为整块切出。在铣床上铣出零件的最大轮廓尺寸5/8×3/4吋,并铣平一个端面。连杆大头轴承在6月28日已经制妥。此时用上。
工艺流程如下。 -在长方体毛坯中,立铣安装面以及小头轴承处尺寸。中部留着原尺寸不动,便于在平口钳上定位。 -在轴承毛坯和保持片(1/8吋铝片)上打一个螺纹通孔(3.2mm),备用。 -毛坯竖直装夹在铣床上,寻边,定位打螺纹底孔,攻丝M3 -在大头安装面上打中心孔,便于车制回转部分 -大头轴承及保持片用螺钉装上,定位打另外一侧螺纹底孔,卸下轴承等 -在螺纹底孔上攻丝M3,扩轴承和保持片上孔到3.2 -整体装配起来,铣到大头尺寸。 -装回轴承等,平口钳上放平装夹。铣床上准确定位并钻-扩-铰1/4吋和3/8吋大小头孔。在一次装夹中完成,可以保证两孔的周线间距和平行度要求。 -铣回转部分到毛坯尺寸,砂轮机上打去锐角,以减少车制的时候对车刀的冲击。
阶段成果见图
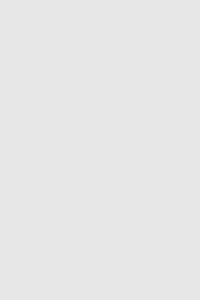
================================================================ 7月12日,连杆完成
四爪卡盘上车处链接部分以后,连杆开始有点样子了。但是随后各种不顺,小头部分本拟压入心轴后在回转工作台上铣出,结果貌似铰刀超差,铰出的孔和心轴配合不紧,铣刀一切上去整个连杆就转动鸟,不仅没把圆弧切出来,反而啃掉一块需要保留的部分。无奈之下,圆弧只能手工在砂轮上磨出,好在不影响重要尺寸,难看就先难看一点罢。
完成连杆后顺手车了个销子,和连杆上小头孔配合。
下一步是做导轨部分,找了一个大圆棒,在车床上扒出外圆,接着车内孔,端面。明天要做的是切断,装心轴后车另一端面,分度头上铣槽和平面。
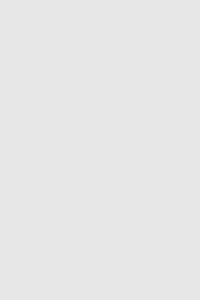
================================================================ 7月13日 十字头导管毛坯
顺着机座的尺寸一路上去,是十字头导管。原来的设计也是铸件,此处改成三件焊合。导管体一件,支腿两件。
这个零件的最大直径略大,有2吋,俺在材料堆里找了找,有2.75吋的低碳圆钢,尺寸大的有点多,也就先这样了。
车好全部外圆到尺寸,用卧式带锯机切断,再掉头装夹,车法兰侧的端面,留一点余量待切。手压床上压入心轴后,在万能分度头+顶尖的帮助下,铣两个对侧的两个平面。
接下来在铁板上画线,锯坯料下来。先铣一侧作为基准面,然后夹在铣床工作台上,找准尺寸立铣折弯槽。折弯部分成型后焊接加强。
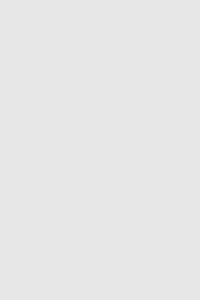
================================================================ 7月16,17日 十字头导管,曲轴切断
十字头导管的焊合是在7月12日进行的,期间遇到一点定位上的问题。仔细找正焊合后位置基本还是比较正的。
焊好后压心轴,装在车床上车平底部安装面。
焊接时在曲轴侧板上也点了两点,再次加强一下。今天做了切断,讲原来轴身中间的间隔部分切去,以形成真正意义上的曲轴。结果尚好。切断之前在车床上做了同轴度的检查,有少量焊接热变形,于是在轴颈上又光了一刀。其余的同轴度问题,可能要到V形块和平板上校正了。
曲轴切好后,连杆也有地方去了,将曲拐的轴颈部分砂磨抛光后,连杆装上可以顺畅转动。
下一步是镗导管内圆,并加工十字头。本拟先打安装孔,将导管安装在基座上再镗孔的,结果难以找准水平和前后方向的位置,因而还是先保证十字头处的配合后,再行加工为妥。
两张图,一张是装起来摆摆样子,一张显示连杆装上曲轴后的情况
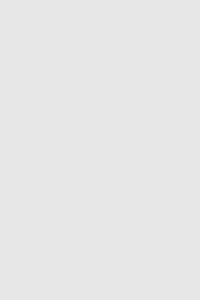
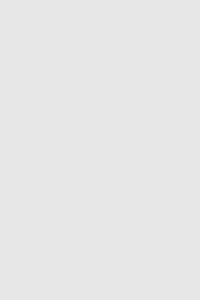
================================================================ 7月18日 导管,十字头完成
早上一去,先两顶尖车平顶面,并且保证十字头导管总高在尺寸内。
随后是镗内孔的工作,这个活计想想简单,动起手来还真不是那么容易,主要是设置和调整的功夫。首先要检查铣床主轴对台面的垂直度,用杠杆百分表装在主轴上,转动测量台面上的几点,并且调节立铣头的俯仰和旋转。机床精度保证后,是找正内孔圆周。还是用装在工作台上,结合百分表的读数一点点调节到位,最后锁紧工作台,同时设定零点。用镗头镗孔很简单,不叙。总共的设定时间,要有45分钟以上,和工作室的人说起,他们倒也风趣,"Welcome to our world".
镗玩内孔后,是加工十字头的工作。现在车床上切出全部外圆,黄铜非常易于切削,并且极易得到良好的表面质量。钻中心孔和螺纹底孔,攻丝。随后是上铣床铣出两边的让位槽,并钻,铰销孔和顶丝孔。
过程中有一点教训,即使有貌似很好的量具,也一定要试切!车十字头外圆的时候,原先是按照测量出来的导管内径尺寸车制,结果出来一试,非常松旷,明显是有一个度数有误。换了一把游标卡尺再测,结果相差0.005吋(0.127mm),怪不得会那么松。只好原件作废,重切一件。在单件加工的时候,量具自身可能带来相当程度的误差,不能盲目迷信之,还是要以试切后的配合为准。
镗完的内孔,表面质量已经不错,再加以研磨则更佳
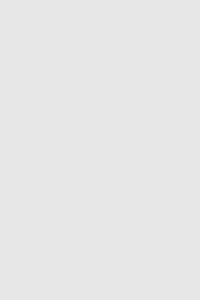
临时装配好后,“活塞运动”轻快灵活
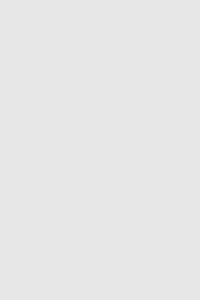
================================================================ 7月22日-8月1日 缸体,缸盖(共三件),活塞,活塞杆,活塞环
近期略微有点不在状态,加之好友携家属来,花了几天陪同一起游玩,故而更新松懈了。兹将一周来进展,一同更新之。
气缸体 设计中的缸体,是铸件,此处照例改成焊件,变成两块分别切削后装配而成。如图。缸体用圆钢车/镗而成,内孔绗磨形成网纹状纹理以便润滑,沟槽立铣出来,并在两端接近端部处开进气孔。配气部分另外用钢板立铣,形成与缸体同样曲率的圆弧,紧密配合之。两个部分本拟银焊起来,问题在于银焊难以在不填满沟槽的情形下,对三个通道相互形成气密。现在打算改成螺钉固定,用耐热密封胶密封中间。
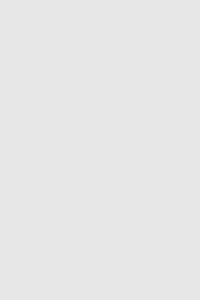
缸盖(透盖,闷盖,填料函压盖) 有了缸体尺寸作为参照,加工气缸盖。闷盖部分相对易于完成,车床,三爪卡盘上夹紧,先车法兰,止口处到尺寸,钻让位槽,再掉头车外侧部分。 透盖略复杂,因为有若干同轴度和垂直度要求需要同时保证。加工时颇费了些周折。原来的方案是先钻,铰内孔,再用心轴装夹车出止口和各处端面。结果好容易车出大样,压进心轴,在车床上顶住一试,转动时居然能看出明显的跳动。打表看出,心轴自身的弯曲量就达到0.004吋,上梁不正下梁歪,怪不得跳动不已。打表找出凸点,夹上台钳试着用铝管扳正,好不容易扳了个差不离,结果咔嗒一声,这坑爹的心轴居然断了。。。无奈,上四爪打表慢慢来罢。费了几把子力气,好歹找正了,车止口,车车法兰,车端面。掉头来车另一处的止口和法兰另一侧,还是同样的折腾。车完测量之,法兰两侧还是有一点不平行,不管它了,就这样罢。 填料函阶梯孔在车制透盖时完成,压盖单独制作,很容易,先车端面,外圆,钻,铰内孔,锯下后再掉头车平即可。三件完成后,在回转工作台上打螺纹通孔/底孔。
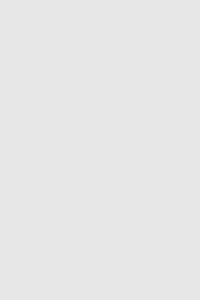
活塞,活塞杆 双作用式蒸汽机的活塞,就是一个圆饼子,车床上先车出大样,钻,铰孔。留部分余量等装上活塞杆后再切到尺寸。 原来设计中的活塞杆,完全是1/4吋的一根圆棒,两头攻丝,一头拧活塞一头拧十字头。这样的设计其实是有问题的。粗牙螺纹无法准确定心,尤其是在需要多次安装的情形下。因而改成活塞一侧用圆柱面定心,螺纹紧固,另一侧不变。一夹一顶先车到外圆尺寸,和透盖成滑动配合。装夹不动,车活塞孔配合面,车螺纹大径,套丝。 活塞和活塞杆两件装起来后,继续装回车床上,一夹一顶车外径到与气缸成间隙配合,车平端面。
活塞环 实际机器上的活塞环,多是特种铸铁或者钢质的,此处铸铁不易得,改用黄铜质的。车外圆到比气缸大1/1000吋,车内孔,用切断刀根据活塞环槽宽度切断,砂纸略加修磨。刚切断时黄铜尚硬,不易装入槽内,加热水蘸之可以使其软化。
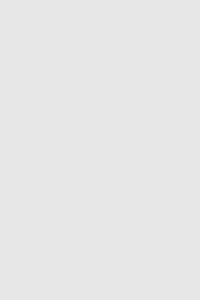
全部完成后,上油试装,转动尚灵便,至此底座-曲轴-连杆-十字头-活塞杆-活塞的尺寸链基本建立起来了,下一步是配气机构的加工
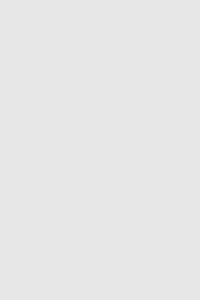
================================================================== 8月12日更新,滑阀座,滑阀室,滑阀,滑阀室盖,滑阀室填料压盖
一个星期的奋战以后,模型又小有进展。主要是配气部分零件的制作。
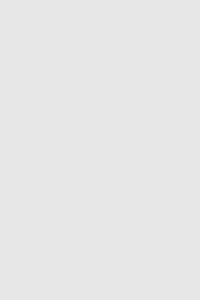
此图展示各个零件情形,分别是气缸体,滑阀座,滑阀室(填料压盖,导管),滑阀,滑阀室盖
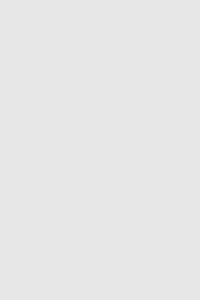
滑阀座 原始设计中,缸体是铸件铸件,俺照例改成加工后拼合的策略,气缸体一件,滑阀座一件。气道开在气缸体外圆上,而配气口开在滑阀座上,分别准确切削以后,再拼接。
滑阀座以方铁一块,先铣出大的轮廓尺寸,再用定尺寸(2吋)铣刀慢慢铣出弧形部分,随后在工作台上找正,并挖出进/排气口。
切成后,涂色测试两件接触情况,尚可。本拟银焊在一起,就此方案去咨询工作室的焊工师傅,答曰一方面气密难以保证,另外一方面,可能在焊接时,焊料流入并填满气道造成不必要的麻烦。讨论后认为,既然这两件的接触情况尚好,可以用螺钉链接之,接合面涂高温密封胶以保持气密。
滑阀座的平面部分,是与滑阀相配,进行配气工作所用。故而需要相当平整,需要与滑阀体配研到密合方好。
滑阀室和滑阀室盖 滑阀室是一个三边有孔的铁框子,本来不应该成为拦路虎的,结果在切制的时候却遇上了意外的问题。
整体的工艺,系用方钢一块,先切成矩形,挖中间方孔(先立铣成圆角方孔,再修锉之),打安装孔,攻丝,车床上找正切圆弧部分并钻,铰台阶孔。再定中心打进气孔。盖子在滑阀室制成后,用铝板配打孔。
结果,挖铣出大方孔以后,打安装孔时遇到了麻烦,M2.5螺纹,需要用Φ2.1的钻头钻螺纹底孔。打前几个孔将透的时候,钻头发出一点唧唧的摩擦声,我心想,不会这么快就钝了吧,这根新钻头才打了十几个孔而已,应该还能用下去。于是就一直接着用,打到倒数第二个的时候,只觉得控制进给的把手一松,钻头断在了孔里。原本只是头上的一小截,俺想。马上就要打透了,干脆强钻一下试试,于是强钻之。结果又是一声轻响,钻头齐孔口断了。此时心中真有草泥马在奔腾,后悔手贱去强打,这时候一天的劳动,基本告吹。想着打完最后一个孔,试试看能不能把断钻头取出来。翻过来一看,表面已经有点凸起,就在此处用中心钻钻透,拿断钻头磨尖敲击之,无效,加热敲击之,还是无效,打横贯孔,试图用钨钢铣刀切断高速钢残段,还是未果。无奈之中只能此件放弃,另切一件。带来的教训是:一旦察觉钻头切削不良,即使是新钻头也要果断更换之,否则一旦断裂,劳时费工不可胜计!贴图一张以为警醒。
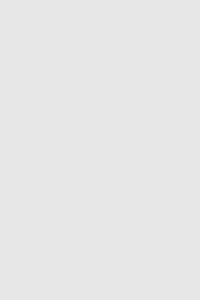
滑阀室完成后,在滑阀座,滑阀室盖,气缸体上打相应的孔,需要攻丝的则攻丝。关于多个零件打通孔,有其一般的规则。一般来说,借助机床标尺可以获得相当准确的位置。如果已有一个零件,要在另一零件上配打对应的孔,可以采用的实用方法有: 1,利用转移中心冲,这是一种成套的冲子,一端是尖头,圆柱部分则是与原来孔径相配,将其插入已有之孔,轻敲末端,则可在欲打孔零件上冲出印痕。可直接或小心用中心冲加深后,上钻床钻孔, 2,以已有孔之零件作为钻模。尤为适用于两零件孔径相同之时。两零件定位后夹紧,上钻床,以钻头伸入原有之孔后,再钻入欲打孔零件,即可得准确孔位。
滑阀室填料压盖和导套 均用黄铜质,车床一次装夹,车出装配部分外圆,钻铰内孔,并套丝。
此处想到一事,每次谈及螺纹加工,很多人不管三七二十一,一律称为“攻丝”,此叫法大不合适。小直径内孔螺纹,常用丝锥加工,一般称为攻丝。小直径外螺纹,多用板牙加工,一般称为套丝,攻受有别,实在是值得区分细致。车制/旋风铣等法不在此列。
滑阀 滑阀用黄铜块铣成,一面凹入以连通排气道,另一面铣出十字以容纳滑阀杆螺母,并可略作活动,以便在蒸气压力作用下能压紧滑阀座配合面。
配合面需要相当平整,装配时与滑阀座配研之。
|
蒸汽版田宫1:35 一战英国雄性坦克模型(带视频) [复制链接]
迷你双缸轴换气蒸汽机模型 尺寸:长度43MM,宽50MM,高25MM,重58G。飞轮直径18MM,轴直径2MM。气缸直径6MM。活塞行程4MM。铜管直径2.5mm。
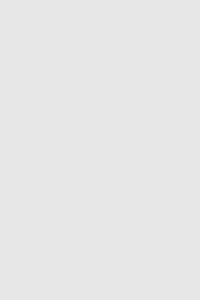 |
车型历史:美国经典-斯坦利蒸汽车。 利用高压蒸汽锅炉足够储存可以行驶45英里的热水。这款新车非常成功,成为当时美国无马车的经典。斯坦利蒸汽车成为了一时最流行的车型,美国生活的象征,到1927年方终止生产。 1:16比例模型车看起来很小,需要给它装上迷你锅炉,迷你蒸汽引擎,还有减速箱.燃料部分等.尽量不对原车做过多改动.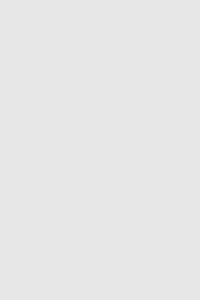
蒸汽爬虫机器人模型在这里,我们有一个小型蒸汽动力爬虫机器人,也许这是见过的最小的蒸汽模型。经测量它长度130MM ,宽110MM ,高90MM ,重量300G 。它是由铜和不锈钢。整体相当紧凑。后置一个迷你蒸汽引擎提供强劲的动力。它的前面有2毫升的燃油箱。动力经过锅杆减速通过中间齿轮与前后驱动齿轮同步.它的前面设计有一张小椅子,也许你会找到一个合适的小人操纵它。行走起来很有节凑感,相信你会喜欢和拥有它。工作时间约为5-10分钟。
|