本文从三个方面研究了锂电池极片的制备:
(1)基于常规浆料—涂布(slurry-based coating)方法,研究了不同混料工艺对浆料流变特性、极片形貌、力学和电化学性能的影响。
(2)研究浸渍沉淀相分离(immersion precipitation ,IP)工艺制备锂电池极片的可行性;
(3)基于静电喷雾沉积(electrostatic spray deposition,ESD)开发一种无溶剂干粉涂布技术(solvent-free dry-powder coating process)用于锂电池极片制备。
本篇为第一部分,关注点在于不用混料顺序(different mixing sequences)对锂电池NCM111正极片性能的影响。

图3 论文摘要
1. 电极原材料
NCM111正极极片制备所需材料如图4所示,活性材料(AM)来自优美科,粘结剂为PVDF(KF1100,吴羽),导电剂为超导炭黑(SP C65,Timcal),溶剂为NMP(巴斯夫)。浆料中固相质量百分比为NCM:CB:PVDF=92:4:4。

图4 NCM正极片原材料及品牌
2. 制浆工艺
采用4种不同的混料工艺制备NCM111正极片,不同制浆策略如图5所示,顺序1(sequence 1,SEQ1)的工艺特点为步骤1制备PVDF/NMP胶液,步骤 2加入CB导电剂粉料搅拌分散后步骤3加入NCM111粉末继续搅拌分散获得最终浆料,属于传统湿法工艺,导电剂和AM逐步加入。SEQ2步骤1同样是制胶,步骤2将AM和CB进行预干混(dry pre-mixing),步骤3将干粉混料加入胶液搅拌分散获得最终浆料。SEQ3与SEQ2前两步相同,步骤3将干粉混料加入NMP溶剂中搅拌分散,步骤4将胶液和步骤3中的溶液一起混合搅拌。SEQ4的特点是步骤2首先将CB加入NMP溶剂中分散,步骤3将胶液和CB/NMP溶液混合搅拌,步骤4加入AM颗粒后搅拌分散获得浆料。SEQ1和4中CB和AM分开搅拌分散,SEQ2和3中CB和AM进行了预干混处理。

图5 四种不同的制浆工艺简易流程图
在浆料不同制备步骤采用了不同的分散设备,同时对应的分散参数归纳如图6所示。所有工艺的第一步都是制胶,涉及PVDF在NMP溶剂中的溶解问题,如何提高PVDF的溶解性,这是一个问题,下次进行相关的总结(涉及PVDF粉料的粒径、PVDF聚合物类型、固含量控制,温度控制等等,吴羽的几款PVDF在聚合方式上好像有所区别)。SEQ1和SEQ4相似,导电炭黑C65率先加入NMP或胶液中,本质上没大的区别,SEQ4先在低粘度的NMP中进行PVDF的分散,效果被证明略优于SEQ1(PVDF胶液粘度高于NMP溶剂)。SEQ2和SEQ3共同点在于AM和CB进行预干混,预干混常常带来的效果是小的CB在大的AM表面形成包覆层,干混后加入PVDF胶液或NMP溶剂中。不同方法制备的浆料静置5min真空脱泡,随后进行涂布(涂布速度0.2m/min,Al箔厚度15um)和辊压。
图6 不同混料工艺过程对比
针对SEQ1进行工艺优化,主要涉及涂布间隙、浆料固含量的调整,图7为不同工艺验证试验结果,试验2被认为是满足厚度和面密度要求的结果,涂布极片厚度80um,面容量2mAh/cm2。此外对不同搅拌时间和辊压对电极厚度、孔隙率、压实密度进行了对比,结果表明搅拌时间对其影响较小,而辊压则显著提高了压实密度,降低孔隙率(如图8所示)。

图7 SEQ1涂布工艺优化验证结果

图8 搅拌时间及辊压对极片压实密度、孔隙率、面容量及厚度的影响
搅拌时间对NCM111正极片倍率性能和循环性能有较大影响(如图9所示),辊压前30min搅拌电极10C放电比容量最大,随搅拌时间的延长放电比容量显著衰减,循环性能也降低,辊压后则随搅拌时间的延长10C放电容量增加,循环性能则降低。对于这样现象, Mohanad AL-Shroofy的论文里没有具体的解释,个人认为辊压前极片孔隙率大,限制倍率性能的主要因素是电子导电即电极内部的导电网络,长时间搅拌易引起CB的团聚导致电极导电路径损失,倍率性能下降,NCM活性颗粒出现结构破坏。辊压后限制倍率性能的因素主要是孔隙率,30min试样孔隙率最小,离子导电受限,最终确认的搅拌时间为60min。

图9 不同搅拌时间对极片辊压前后电化学性能的影响
涂布间隙的影响主要影响极片单位涂覆量,即极片面密度的大小。湿膜干燥后辊压到相同厚度40um,涂布间隙越小,辊压前极片越薄,辊压压缩率越小;涂布间隙越大,极片初始厚度越大,辊压压缩率也越大。图10为不同涂布间隙极片在相同的辊缝辊压后压实密度、孔隙率和面密度的变化及倍率放电性能,从而确定最佳涂布间隙为200um。

图10 涂布间隙对电极物理性能和倍率性能的影响
同时Mohanad AL-Shroofy重复试验分析了工艺一致性问题,如图11所示组内和组间一致性较好,试验重复性、再现性好。

图11 不同批次试验重复性、再现性分析
3. 形貌结构分析
图12所示为优化工艺后的SEQ1(60min,200um涂布间隙)制得的正极片显微组织,结果表明PVDF/CB形成的导电剂/粘结剂聚合体均匀分布在NCM111活性颗粒之间。

图12 SEQ1对应正极片SEM显微组织及EDS面扫面照片
对于SEQ2,与SEQ1相比相同NMP含量时SEQ2浆料粘度较低,为了获得与SEQ1浆料相同的粘度,对SEQ2浆料固含量进行优化,图13为SEQ2浆料流变曲线和动态振荡剪切曲线,结果表明,随着固含量升高,浆料粘度增加,SEQ2中浆料的损失模量高于储存模量(G'>G'),浆料表现出流体特性(liguid-like)。
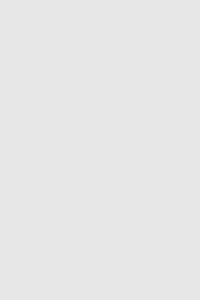
图13 SEQ2浆料不同固含量(SML)的流变性能
图14为SEQ2对应的辊压电极形貌照片,特征在于部分CB吸附在NCM111颗粒表面,同时CB/PVDF在NCM表面形成包覆层。图15为SEQ3极片显微组织,类似地在NCM表面包覆CB和PVDF附着层,此外一部分PVDF分布溶剂中,需要注意的是SEQ3桶SEQ2一样G'>G',表现流体特性,粘度较SEQ1低,对其固含量进行调节使其粘度与SEQ相同。图16为SEQ4对应极片显微组织,与SEQ1类似,CB/PVDF聚合体分布NCM颗粒间。图17为根据SEM组织给出的不同制浆工艺对应的各组分分布示意图。SEQ1和SEQ4结构类似,CB/PVDF形成的聚合体分布在NCM活性颗粒的间隙,SEQ2和SEQ3对应的极片中CB包覆在NCM表面,PVDF分布在颗粒表面及间隙中。
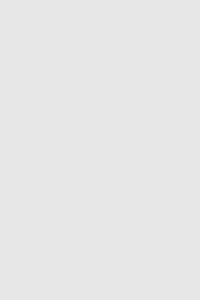
图14 SEQ2辊压极片SEM显微组织
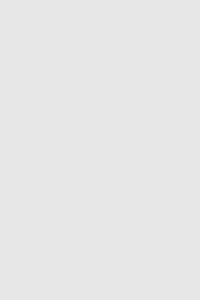
图15 SEQ3辊压极片SEM显微组织
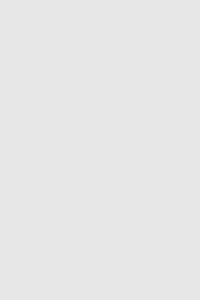
图16 SEQ4对应极片SEM显微组织照片
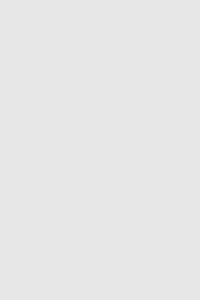
图17 不同制浆工艺对应极片中个组分的分布情况
下面对不同制浆工艺获得的浆料和极片进行对比分析,包括浆料的流变特性、极片电导率、极片力学性能及电化学性能几个方面。
(1)流变性能对比
为了满足涂布工艺要求,通过调节SEQ2和SEQ3中NMP的含量,获得与SEQ1和SEQ4相同的粘度(50S-1剪切速率下),最终的浆料配比和固含量如图18所示,图19为对应浆料的流变曲线,相同粘度下(50S-1)下SEQ1和SEQ4对应浆料固含量较低(55%左右),SEQ2和SEQ3浆料的固含量明显增加(70%左右),在低剪切区SEQ2和SEQ3浆料的粘度更小。由此可见,SEQ2和SEQ3分散效果明显强于SEQ1和SEQ4,浆料具有更好的流动性,振荡曲线也再次说明SEQ2/3为液流态(liquid-type),SEQ1/4为凝胶态(gel-type)。
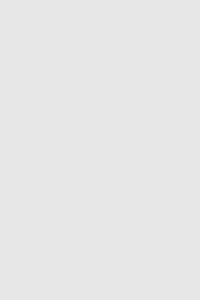
图18 不同制浆工艺浆料配比及固含量
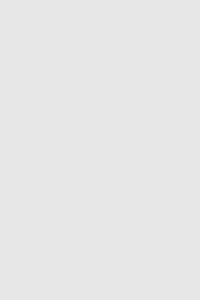
图19 不同制浆工艺对应浆料流变特性
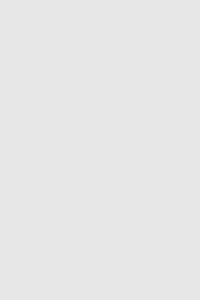
图20 不同制浆工艺动态振荡剪切曲线
(2)力学性能
对不同制浆工艺获得的极片进行纤维硬度测试,如图21所示(加载速度4um/s,压痕深度20um,压痕间隔250um)为不同制浆工艺对应极片硬度和弹性模量大小。SEQ2/3极片硬度和弹性模量高于SEQ1/4对应的极片。图22采用划痕试验对比不同极片的粘附性能,同样地,在SEQ2/3极片中颗粒间的粘附力大于SEQ1/4极片。电极力学性能的差异与内部粘结剂、活性颗粒和导电剂的分布有关,SEQ2/3中CB分布NCM表面,粘结剂分布在CB包覆的NCM颗粒之间,在SEQ1/4中CB/PVDF形成的聚合体分布在NCM颗粒间,由于CB与PVDF间的粘附力强于NCM与PVDF间的粘附力,因此SEQ2/3具有更好的力学性能。
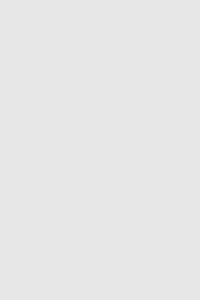
图21 不同制浆工艺对应极片的显微硬度和弹性模量
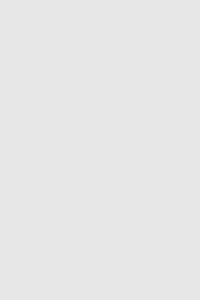
图22 极片划痕试验结果
(3)电极电导率
图23为不同工艺获得的极片电导率数据,SEQ2/3对应极片的电导率显著低于SEQ1/4极片电导率,主要源自PVDF的包覆抑制NCM颗粒间的电接触,电阻导电性能显著下降。Werner Bauer在研究预干混和导电剂分布对正极片性能的影响时也发现了类似的现象,粘结剂形成的包覆层减少了活性颗粒间的电接触。
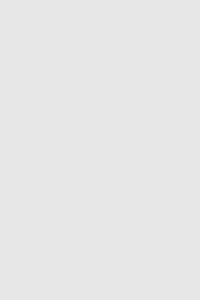
图23 不同制浆工艺对应电极电导率
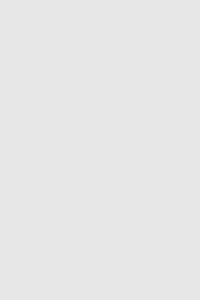
图24 不同混料工艺对浆料组分分布的影响(参考文献2)
(4)电化学性能
如图25所示为不同工艺对应极片的倍率性能和循环性能,SEQ4对应极片5C放电比容量最大,倍率性能最好,150次循环后SEQ1对应极片的容量保持率最高,循环性能最好。采用干法工艺值得的电极在电化学性能方面则没有明显优势。
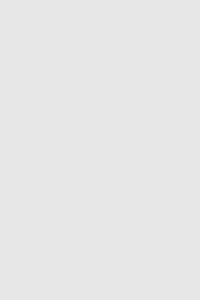
图25 不同制浆工艺极片倍率性能和循环性能
同样的结果在Werner Bauer的研究中也出现了,其提出的解决方案是添加额外导电剂。如图26所示,额外导电剂的加入可弥补PVDF包覆损失的长程电子导电。
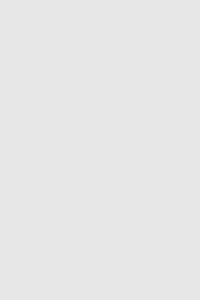
图26 不同制浆工艺中各组分分布示意图
总结
(1)AM和CB预干混形成CB包覆AM表面的组织结构,干粉混料加入PVDF粘结剂后形成的粘结剂包覆层降低了电极内部的长程导电,电极电导率下降,电极倍率性能和循环性能衰减。
(2)AM和CB预干混的优势在于同样固含量下其粘度小,流动性好,可提高浆料固含量满足涂布加工性,同时减少极片干燥时间,提高生产效率。
(3)AM/CB干混对应的制浆时间短,效率高;为了克服电化学性能的不足,可部分CB与AM干混,或添加额外导电剂。
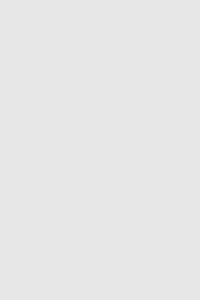
图27 美国肯塔基大学郑仰泽教授(2013年于上海大学)
[1].AL-Shroofy,MohanadN.,'UNDERSTANDING AND IMPROVING MANUFACTURING PROCESSES FOR MAKING LITHIUM-ION BATTERY ELECTRODES' (2017). Theses and Dissertations--Chemical and Materials Engineering. 76.[2].Bauer W, Nötzel D, Wenzel V, et al. Influence of dry mixing and distribution of conductive additives in cathodes for lithium ion batteries[J]. Journal of Power Sources, 2015, 288: 359-367.