汽车白车身冷冲压用材料数据库已经广泛应用于一汽轿车现生产和待投产车型中,该材料数据库的应用,为新项目和现生产车型调试提供了可靠的技术支持,解决了应用老数据库时模拟分析不能还原现场成形状态,无法给予现在调试提供可靠的整改方案,增大了调试难度,而新的材料数据库的应用,彻底解决了以前的老大难问题,降低了供应商的工作难度。
一、引言
一汽轿车公司冲压件常用材料涉及到牌号127种 (同一牌号不同钢厂的材料计为不同钢种) 、材料规格600余种;而目前轿车公司已有的材料数据库较为陈旧, 应用旧材料数据库进行CAE模拟分析时, 模拟预判风险项与实际调试问题产生偏差, 如下页图1所示, 就给产品初期评审、供应商工艺审核、现场问题调试的技术支持带来了很大的麻烦, 可以看出陈旧的材料数据库已经影响甚至阻碍了有限元模拟在指导产品设计和工
二、数据库技术内容
一个准确的材料数据库的建立一般包括三方面的工作:材料数据的收集整理、材料性能参数实验、材料卡片制作。
(1)材料数据库整理
目前轿车公司应用的钢种较多, 同一种钢种又存在不同批次, 由于钢厂供应用于生产的钢板每批次性能参数会存在一个浮动, 无法保证性能参数的稳定性, 因此采用哪个批次的钢板作为实验对象就是一大难题, 为解决这个问题对公司去年一整年的板材进货进行了统计, 通过对屈服强度的观察, 找出频率最高的板材作为实验试样。如下页图2。
应用这种统计方法针对轿车公司车型应用的127种 (同一牌号不同钢厂的材料计为不同钢种) 钢种进行梳理, 每种钢种取3种料厚, 从而确定试样所用钢板。
(2)实验参数测试
在应用CAE技术模拟分析时, 评判成形性的几个重要指标主要有:开裂、起皱、减薄、失效、滑移线等, 而这些评价结果主要是由材料的n值、r值、成形时的摩擦系数所决定的, 在评价成形性时, 多结合成形极限曲线 (FLC曲线) 对结果进行评价, FLC曲线是由材料的主次应变拟合而成的一条可以反应金属成形性的曲线, 通常FLC曲线以上均为开裂。利用实验室现有试验设备开展单向拉伸性能试验、板材成形极限曲线试验、摩擦试验, 获得拉伸原始数据r0、r45、r90、摩擦系数、FLC数据等。如下页图3。
1.FLC实验数据的获得
步骤一:FLC所用试样一般为哑铃型试样, 为了描述完整的FLC我们通常取10组样品, 每组样品至少保证3个有效样本。试样如下页图4。应变量的测量主要是通过印在试样上的网格变形量来测量应变量的大小, 因此需要在试样上进行网格划分, 通常网格尺寸取一倍的料厚, 印制的网格需要保持良好的对比度, 注意不要留下刻痕以免影响最终结果, 当采用铝试样时, 铝板的导电性差, 易氧化, 传统的方法无法进行铝板网格的印制, 我们不断地尝试最后找到了合适的腐蚀液和电流参数, 最终确认了一套铝板的网格印制方法。

图1 同一种材料不同材料卡片分析结果

图2 材料统计情况

图3 实验概况
步骤二:使用成形机对试样进行Nakajima试验, 分析计算得出该拉伸状态下极限应变点即破裂前瞬间的极限应变点, 通过加工不同形状的试样模拟不同的拉伸状态, 并得到一系列极限应变点, 将这些点连接在一起就得到了FLC曲线, 如下页图5。
步骤三:FLC曲线的验证, 在实验过程中由于试样断裂位置不理想, 断裂方向不正确, 分析图片选择不恰当均会导致FLC曲线的不正确, 如下图6。
图6中1点由于破裂位置偏, 导致极限应变点比实际值低, 曲线有不正常的波峰, 图6中2区域两点由于选择分析图片不恰当, 导致两点Y值相近, 曲线出现平直部分。针对图中1位置提出应变分布最高点偏移法, 通过已得到的准确值, 计算得出应变最高点与拟合抛物线最高点差值的平均值, 应用这个值对相应的点进行偏移从而得到准确的拟合点。
2、材料硬化曲线和屈服面的获得及力学性能测试
材料在塑性成形过程中屈服应力增加的行为叫做硬化。可用硬化曲线来描述塑性变形过程中的硬化行为。硬化曲线的形式和应力-应变曲线一致, 可通过平行板材轧制方向的材料力学性能测试获得真实应力-应变曲线, 并在软件中拟合获得硬化曲线。下图7为典型材料的应力-应变曲线和硬化曲线。
材料屈服面可以反映在受力情况下材料的流动状态。Autoform中自带三个屈服模型, 可通过导入0°、45°、90°三个方向的初始屈服应力和r值自动计算屈服面。在本项目中, 通过进行板材0°、45°、90°的单向拉伸实验可一次性获得材料的屈服强度、抗拉强度、均匀延伸率、断裂延伸率、n值和r值同时导出应力-应变曲线。拉伸实验方法和实验标准按照GBT-228执行, 为了保证实验数据的可靠性和实验条件的一致性, 规定了不同钢种的实验条件, 具体见下页表1。

图4 试样简图
对于每一种材料, 每个方向取3个样品, 取最小值作为生成材料数据卡片的原始数据。
3、摩擦系数
金属薄板带在成形过程中会与模具之间产生摩擦, 摩擦力的大小与表面粗糙度和接触压力有关。摩擦系数是指在一定试验条件下 (载荷、润滑条件、试验温度、试验速度) 金属薄板带与模具之间产生的摩擦力和作用在其一表面上法向力的比值。每种材料测试试样不少于3个, 一般取4个试样, 通过设定的压力以及拉力, 通过对数据平均值的测定, 计算的摩擦系数。实验原理如下页图8。

图5 使用成形机对试样进行Nakajima试验

图6 存在误差的FLC曲线
(3) 材料卡片的制作
材料卡片的制作主要是通过AUTOFORM软件完成的, 如下图9。
步骤一:设置材料名称和详细信息, 在material name文本框中输入需定制材料的名称, 右击comments域可在弹出的文本框中添加材料的附加信息。
步骤二:定义弹性性能和密度参数。Autoform提供了两种材料类型, 分别是钢 (steel) 和铝 (Al) , 点击名称为钢或铝的按钮即可确定材料类型, 同时系统会根据材料类型自动调整后续涉及的系统推荐参数值和材料模型, 具体信息如下表2所示。

图7 典型材料的应力-应变曲线和硬化曲线
表1 不同钢种的试验条件


图8 实验原理图
其中杨氏模量和泊松比可利用电子万能拉力试验机测出。
步骤三:定义硬化曲线。硬化曲线:AUTOFORM采用的硬化曲线是基于真实应力应变拟合得来的, 硬化曲线能反映试样变形的瞬时状态, 具有各阶段可加性等优点, 并且只反映随行变形阶段的情况。
步骤四:定义屈服准则 (目前统一采用BBC模型) Autoform中使用的屈服面模型为Hill, Barlet和BBC steel和BBC Alu。各模型的适用范围和参数取值详见下页表3。
r0、r45、r90为与轧制方向成0°、45°、90°三个方向截取拉伸试样测得的r值, σ0、σ45、σ90为三个方向的初始屈服应力。
rm为塑性应变比的加权平均值rm= (r0+2r45+r90) /4
M:拟合系数。
Biax:双轴应力因子
通过研究发现不同屈服准则拟合出来材料卡片在满足适用范围的条件下, 对实际模拟分析结果产生的误差可以忽略不记。
步骤五:定义成形极限曲线 (FLC) (autoform中默认的是真实应变值, 真实应变=ln (1+工程应变/100) ) 。
步骤六:导出数据库文件。点击FILE按钮, 选择EXPORT mat或EXPORT mtb可导出生成的材料库文件, 将材料库文件整理汇总, 从而完成材料数据库的建立。
三、主要技术创新点
(1)优化软钢及薄板的FLC试验方法
由于软钢在FLC试验过程中顶出高度较大, 试样无法断裂在中间区域, 采用传统的抛物线拟合法和应变分布最高点法, 如在试样中出现失效断裂位置偏移较大或试样中出现二次断裂则无法得到准确拟合点来确定FLC曲线。通过探索, 我们创新的提出应变分布最高点偏移法, 通过已得到的准确值, 计算得出应变最高点与拟合抛物线最高点差值的平均值, 通过此平均值对失效断裂位置偏移较大无法得到准确值的试样进行人工偏移并结合传统的抛物线拟合法, 可更加确认的得到软钢的FLC曲线。

图9 制作材料卡片的Autoform软件
表2 两种材料的弹性性能和密度参数
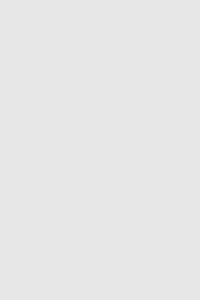
(2) 铝板的FLC试验网格印制创新
由于铝板具有导电性差、易氧化的特点, 在电化学腐蚀印制FLC试验网格时, 采用传统的腐蚀液和腐蚀方法不能得到清晰的网格。我们通过尝试不同的腐蚀液和电流参数, 最终确认了一套铝板的网格印制方法, 可得到清晰度更好、灰度更深的网格, 大大提高了软件提取网格的精确度。
(3)完成的材料数据库建立方法
通过不断的探索, 一汽轿车已经形成了一套完善的材料数据库建设方法, 该材料数据库建立方法同样适用于其他整车厂。
四、与当前国内外同类技术比较
成熟的冲压CAE分析所应用的材料数据库目前主要都是由各大钢厂负责构建, 而整车厂在数据库建立方面由于多方面的原因总体实力相对薄弱, 在CAE分析时多直接应用钢厂提供的材料数据, 很难对钢厂提供材料数据的准确性进行验证, 掌握材料数据库的建立手段对整车厂来说具有重要意义, 一方面可以验证钢厂提供材料数据库的准确性, 另一方面可以及时对现有数据库进行更新维护, 保证数据库的时效性。
表3 各模型的适用范围和参数取值
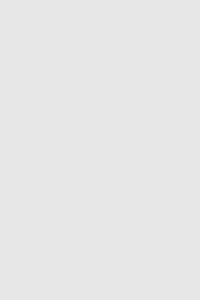
表4 定义成形极限曲线方法
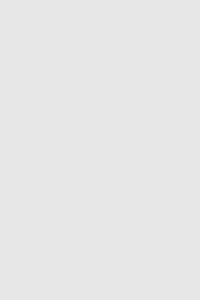
五、小结
新建的材料数据库已经广泛应用于一汽轿车现生产和待投产车型中, 该材料数据库的应用, 为新项目和现生产车型调试提供了可靠的技术支持, 解决了应用老数据库时模拟分析不能还原现场成形状态, 无法给予现在调试提供可靠的整改方案, 增大了调试难度, 而新的材料数据库的应用, 彻底解决了以前的老大难问题, 降低了供应商的工作难度, 由于整改方案可以迅速准确地给出, 大量节约了人力物力, 提高了工作效率, 使得供应商可以保质保量的在项目节点之前完成模具交接工作。同时新材料数据库的建立, 使得供应商可以在DL图工艺设计前期更快的识别可能存在的问题, 从而在工艺设计初期就可以将问题解决, 减少了后期的工作难度, 加快了项目的整体进度。